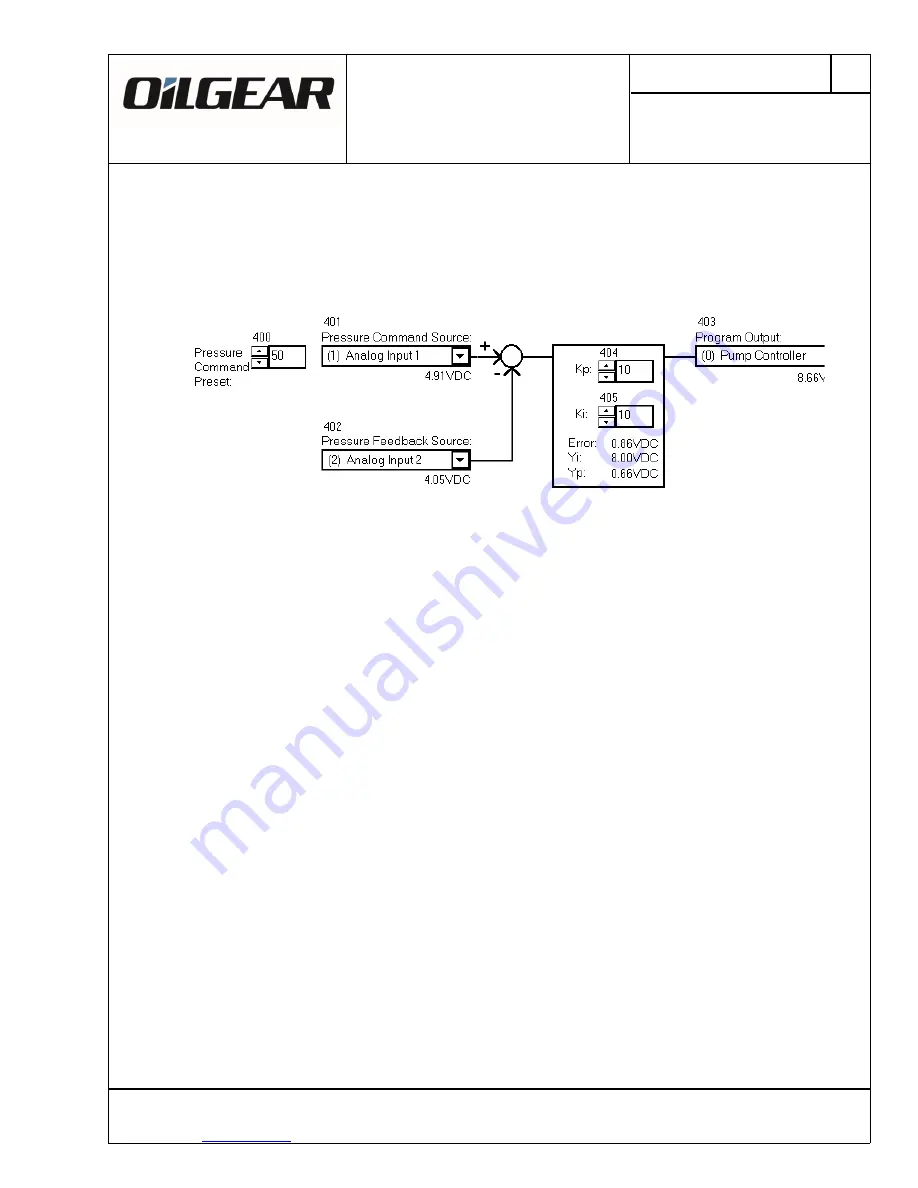
EPC
SERVO AMPLIFIER MODULE
Part Number L723888-3xx
ELECTRONIC
Telephone: (231) 929-1660
Oilgear
Fax:
(231) 929-7879
1424 International Dr
Issued May 31, 2018
Web Site:
www.oilgear.com
Traverse City, MI USA 4 9 6 8 6
Bulletin 836260F
14
Program Overview
: The Pressure Control Program is a straightforward PI control
algorithm. Comparing the command to the feedback value produces an error value.
The error is multiplied by the KP and KI constants to produce the Yp and Yi
contributions to the program output.
Figure 4: Pressure Control
Program
Example
: Figure 4 shows the Program 1 Form for Pressure Control. The Pressure
Command Source is Analog Input 1 (program item 401=1) and the Pressure Feedback
Source is Analog Input 2 (program item 402=2). The Pressure Command Preset has a
value of 50% (program item 400=50) although it is not used for this particular example.
The error signal is produced by comparing the command to the feedback signals:
4.91V - 4.05V = 0.86V. The Yi and Yp signals are produced from the PI controller and the
program output is roughly equal to their sum: 8.00V + 0.66V = 8.66V. The Program
Output is set to the Pump Controller (program item 403=0).