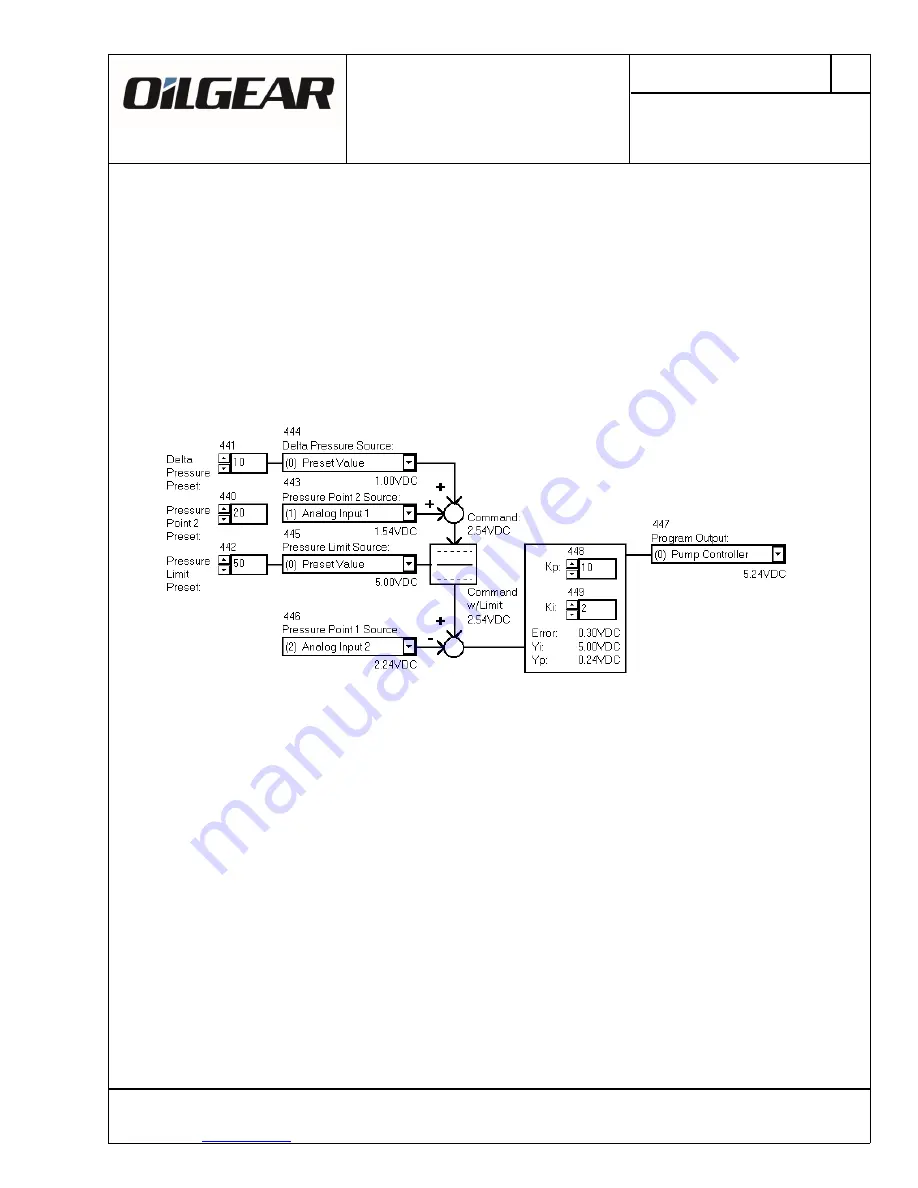
EPC
SERVO AMPLIFIER MODULE
Part Number L723888-3xx
ELECTRONIC
Telephone: (231) 929-1660
Oilgear
Fax:
(231) 929-7879
1424 International Dr
Issued May 31, 2018
Web Site:
www.oilgear.com
Traverse City, MI USA 4 9 6 8 6
Bulletin 836260F
20
Program Overview
: The Load Sense Control Program is one of the more complex control
algorithms supplied with the EPC. The goal of the load sense control is to maintain a pressure
difference across an orifice (refer to Figure 6). Typically, two pressure transducers would be used to
monitor two points in the hydraulic circuit. The pump flow would be controlled such that
P = P1 -
P2.
In addition to this basic control, a pressure limiter is added to ensure that the down-flow pressure at P2
does not reach a critical point. The controller command is the sum of the Point 2 Pressure and Delta
Pressure signals, limited by the Pressure Limit Command. Comparing this command with the Point 1
Pressure signal results in an error value. The error is multiplied by the KP and KI constants to
produce the Yp and Yi contributions to the program output signal.
Figure 7: Load Sense Program
Example
: Figure 7 shows Program 5 Form for Load Sense. The Delta Pressure Source is set to the
Delta Pressure Preset Value of 10% (program item 444=0 and program item 441=10). The Pressure
Point 2 Source is Analog Input 1 (program item 443=1), therefore the command is 1.00V
+1.54V = 2.54V.
The Pressure Limit Source is set to the Pressure Limit Preset Value of 50% (program item 445=0
and program item 442=50). In this case, the previous command value is not limited, since the
command (2.54V) is less than the Pressure Limit Command (5.00V).
The error signal is produced by comparing the Command to the Pressure Point 1 signals: 2.54V -
2.24V = 0.30V. The Yi and Yp signals are produced from the PI controller and the Program Output is
roughly equal to their sum: 5.00V + 0.24V = 5.24V. The Program Output is set to the Pump
Controller (program item 447=0).