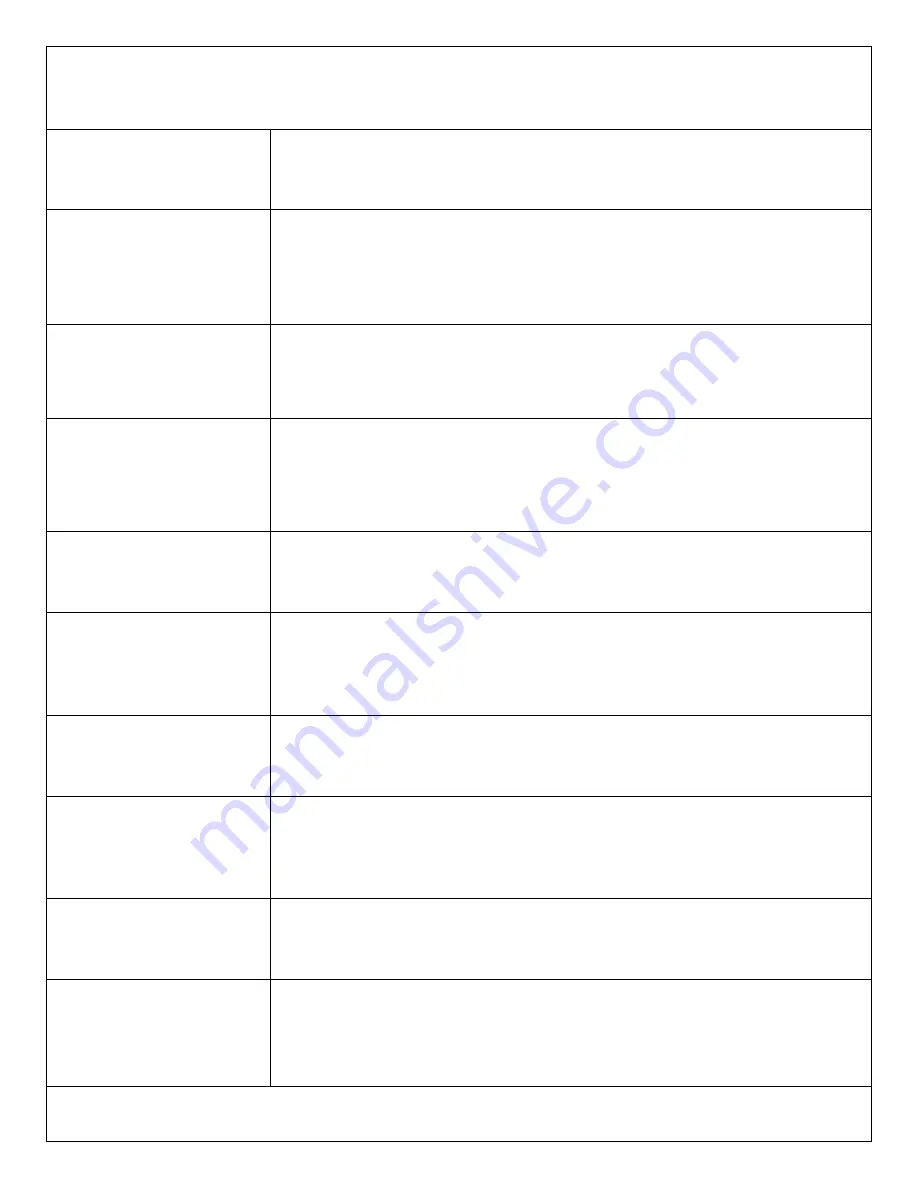
Effective 11/2010
19
Internal Components Description
Power Distribution Panel
The terminal board distributes electrical power to the different components of
the system.
Inlet Air Filter
The air filter keeps dust and dirt from entering the compressor and needs
to be changed twice a year in normal environments to maintain the unit
‟s
performance. It should be changed more often in dirty, oily areas.
Four (4) times a year is recommended.
PLC
The PLC (Programmable Logic Controller) processes inputs and outputs to and
from system components, and communicates with the touch screen. This is the
brain of the machine.
Back Pressure Regulator
Gauge
This gauge controls the balance between oxygen flow and oxygen purity.
Initial setting is between
45
psi (3.1 bar)
and
50 psi (3.4 bar)
. A higher back
pressure will increase purity but decrease storage tank pressure. A lower back
pressure will increase storage tank pressure but decrease purity. This regulator
will adjust the storage pressure and oxygen purity.
Air Storage Tank
Air from the air compressors is stored in this tank before going through the
sieve bed sets on the side of the machine. Normally this tank pressure holds
between
23 psi (1.6 bar)
and
26 psi (1.8 bar)
.
Air Compressor
The air compressors supply the feed air for the sieve beds. They are held in
place by four bolted rubber mounts and can be easily replaced when necessary.
They should work as designed for a minimum of 10,000 hours and will last
20,000 hours in many cases.
Air Pressure Transducer
The transducer gives a variable output current to the PLC at different pressures.
The PLC then communicates this signal to a virtual gauge in the touch screen.
Oxygen Generators
These generators contain the molecular sieve that performs the air separation
process. Exposing the internal sieve material to the atmosphere will cause
contamination. However, if the sieve becomes contaminated the beds can be
easily replaced.
Low Oxygen Pressure
Transducer
The transducer gives a variable output current to the PLC at different pressures.
The PLC then communicates this signal to a virtual gauge in the touch screen.
Oxygen Purity Sensor
The oxygen sensor gives a variable output current to the PLC at different levels
of oxygen purity. The PLC then communicates this signal to a virtual gauge in
the touch screen. See
Appendix Page IV
for details on how to make an
adjustment to this sensor.
Summary of Contents for MOGS - 100
Page 2: ......
Page 6: ......
Page 50: ...Effective 11 2010 44 MOGS 100 Filling Manifold Design Installation Optional...
Page 58: ......
Page 59: ...Appendix...
Page 60: ......