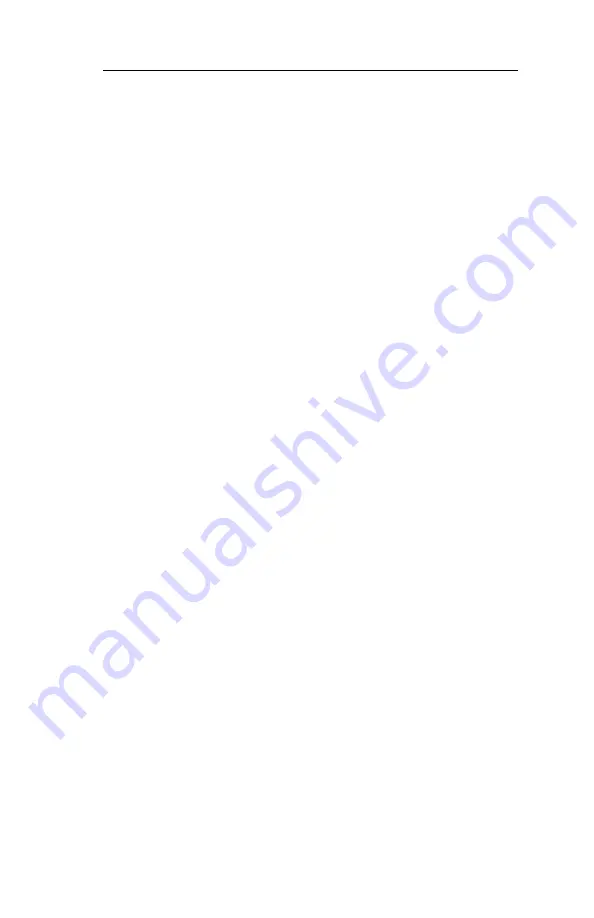
REPLACEMENT PROCEDURE FOR PARTS
IT IS RECOMMENDED THAT ALL OCEANAIRE UNITS BE SERVICED
BY A LICENSED TECHNICIAN
WARNING
—
TO AVOID INJURY, DISCONNECT UNIT POWER PRIOR
TO SERVICING
A. FAN MOTOR
1. Remove cabinet left-side panel (when looking at the front of the unit).
2. Evaporator fan motor
—
disconnect evaporator motor wires from evaporator fan
Contactor, fan speed rocker switch and run capacitor.
3.
For all model sizes 12, 18, 24, and 36
, remove the screws securing motor and
inlet-ring to blower housing (all screws are external and visible), and remove blower
wheel-motor assembly. Remove the blower wheel set screw and disassemble the
blower wheel from the motor shaft and remove the motor.
For model size 60
—
loosen blower wheel shaft set screw, and remove the screws
securing the motor mount to the blower housing.
4. Install new motor/motor mount assembly, reversing the removal procedure for above
models.
5. For Model size 60, confirm motor is wired for proper rotation.
B. THERMOSTAT (NO BATTERIES REQUIRED)
1. Along both sides of the thermostat, insert a small flat blade screwdriver in the groove.
With a twisting motion, remove the cover plate from the sub base. Make sure the small
thermistor located near the top of the casing for temperature sensing, is not bent or
damaged.
2. To remove the thermostat sub-base, remove the 2 mounting screws and the 4 wires
(black, red, white, green). Make sure the 4 wires do not fall into the cabinet. Install
sub-base by reversing removal procedure.
C. CONDENSATE ALARM LIGHT
To replace the Condensate Alarm Light, disconnect the wires from the lamp and bend
the tinnerman clip retaining light and pull out. Install new light, reversing the
procedure.
D. CONDENSATE PUMP
1. Remove brackets securing condensate pump in base pan.
2. Disconnect pump wire leads at Molex connectors. Remove retainer clamp and tubing.
3. Replace pump, install by reversing procedure.
E. HIGH PRESSURE SAFETY SWITCH
While facing unit, to access high pressure switch.
1. Size 18 and 24, remove rear panel. All other sizes, remove right side panel.
2. Remove flare nut that secures capillary to the refrigeration system high pressure
side. A Schrader valve is located in the discharge port, which allows removal without
losing the refrigerant charge.
3. Remove two screws that secure high pressure switch.
4. Disconnect wire leads from compressor contactor and condensate pump safety
switch.
5. Install new High Pressure Switch, and splice in new wire leads with existing control
wires. Then reverse in order to complete procedure.
To gain access to compressor and compressor run capacitor, remove left side panel.
17
Summary of Contents for PWC Series
Page 23: ...21 PIPING SCHEMATIC...
Page 24: ...22 WIRING SCHEMATIC FOR PWC1211 PWC1811 PWC2412 and PWC3612...
Page 25: ...23 WIRING SCHEMATIC FOR PWC6012 07182016...
Page 26: ...THREE PHASE MONITOR 24...
Page 27: ...25 WIRING SCHEMATIC FOR PWC3632...
Page 28: ...26 WIRING SCHEMATIC FOR PWC6032...
Page 29: ...27 WIRING SCHEMATIC FOR PWC3634 and PWC6034...
Page 31: ...TECH NOTES 29...