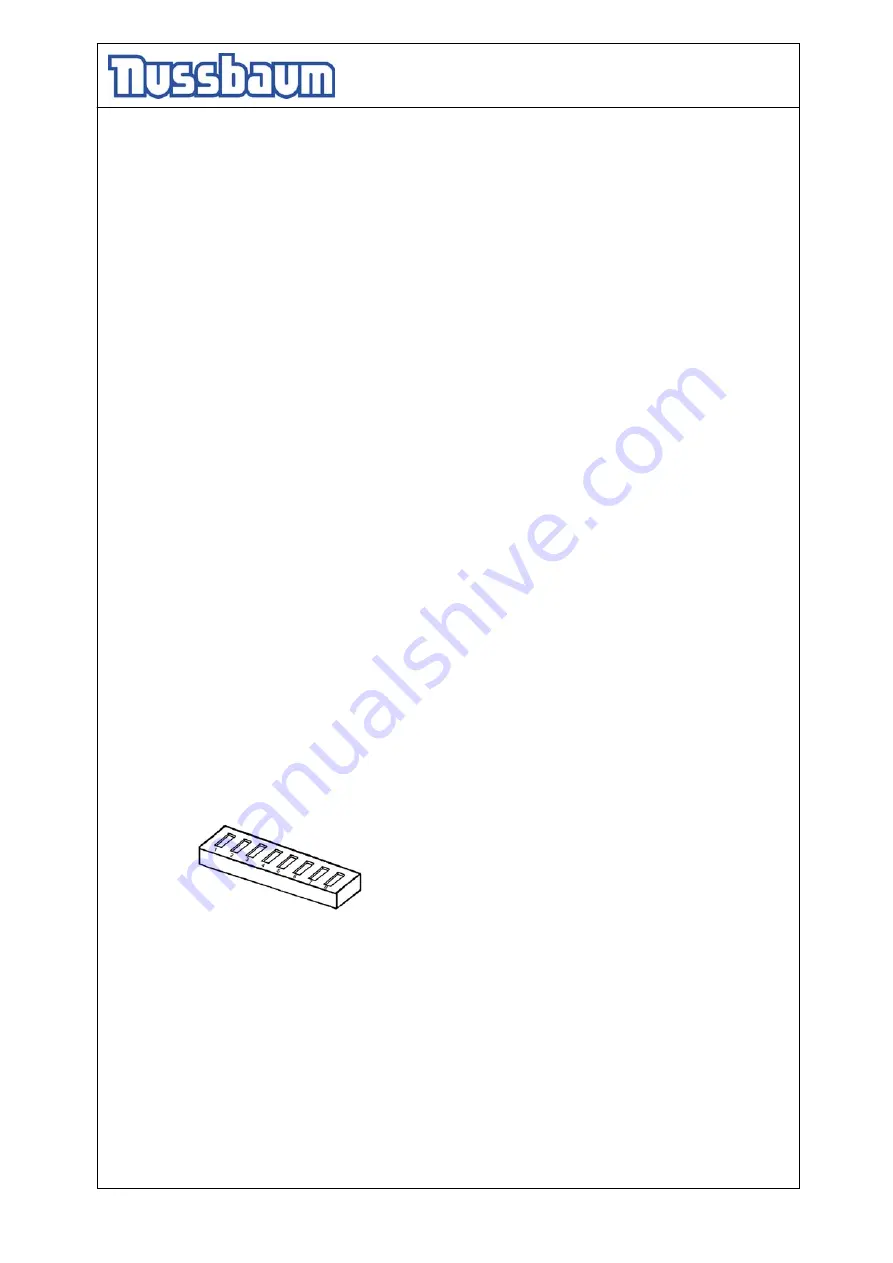
Operating Instruction and Documentation
UNI-LIFT 5000 CLT / Plus
- 21 -
• Lift the vehicle on the working height.
• Observe the complete process.
5.4 Lowering the vehicle with the wheel free lift
• Check the dangerous places of the lift and be sure that there are no objects or
people in the immediate area of the lift or on the lift.
• Lower the vehicle to the working height or until the platform reaches the lowest
point; press the button „lowering“ (R.F.H.)
• Before the lift reaches the lowest position, it stops (approx. 150 mm).
Let off the button „lowering”. Control the dangerous places. Press the button
again. You hear an acoustic signal until the lift reaches the lowest position
• When the lift is in its lowest position, remove the polymer supports
• Drive the vehicle out of the lift if the lift (main lift) is in the lowest position.
5.5 Equalisation of the 2 rails (main lift)
• Press button „Equalize“ at the operation unit. The rails of the main lift equalize. It
is not possible to equalize the wheel free lift with this button.
5.6 Manual equalisation of the lift
• If the SST (Safety-Star-System) makes out a difference of approx. 40 mm, it will
stop the lift automatically.
• An equalisation has to be prepared
• Remove the top covers of the aggregate and the covers of the control box.
• In the control box unit you find the DIP-switches.
Dip-switch on the board in the box.
An access on the Dip-Switch is only allowed when
the main switch is switched off and only by
instructed, authorized technical staff.
• Dip-switch 5 (regulation ON/OFF).
• Dip-switch 1 (only platform 1 moveable).
• Dip-switch 2 (only platform 2 moveable).
• Dip-switch 7 (reset – zero the lift in the lowest position).
Enforce the equalisation:
• Equalize platform 1.
• Move the Dip Switch 5 on position “off” (regulation off).
• Move the Dip switch 1 on Position “on” (Dip switch 1 for platform 1).
Summary of Contents for UNI-LIFT 5000 CLT PLUS
Page 9: ...Operating Instruction and Documentation UNI LIFT 5000 CLT Plus 9 page for notice...
Page 12: ...Operating Instruction and Documentation UNI LIFT 5000 CLT Plus 12 3 3 Datasheet...
Page 13: ...Operating Instruction and Documentation UNI LIFT 5000 CLT Plus 13...
Page 14: ...Operating Instruction and Documentation UNI LIFT 5000 CLT Plus 14...
Page 15: ...Operating Instruction and Documentation UNI LIFT 5000 CLT Plus 15...
Page 16: ...Operating Instruction and Documentation UNI LIFT 5000 CLT Plus 16...
Page 17: ...Operating Instruction and Documentation UNI LIFT 5000 CLT Plus 17...
Page 18: ...Operating Instruction and Documentation UNI LIFT 5000 CLT Plus 18...