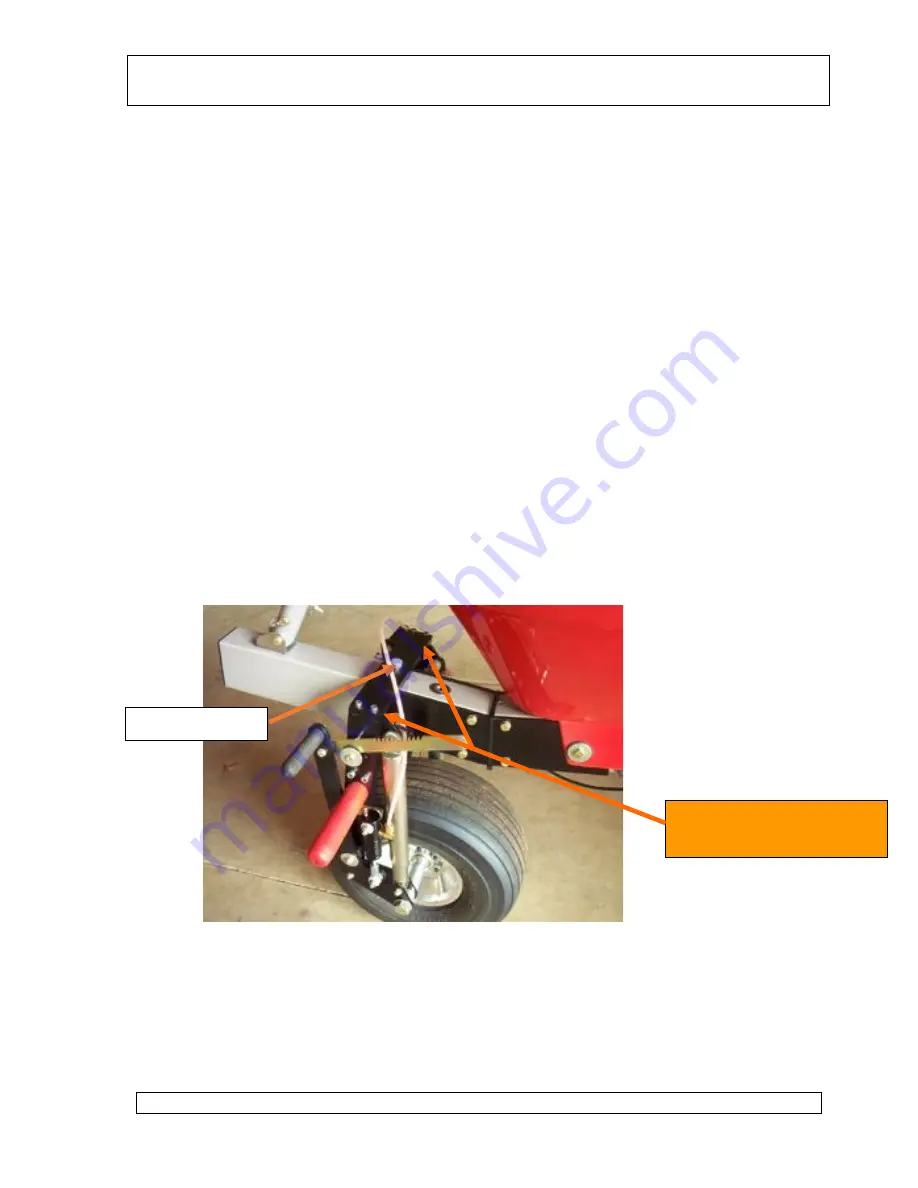
North&Wing&S,LSA&Maintenance&Manual&
Model:&Sport&X2&582&
Issue 3.2
Printed: July 16 2017
Page 65
4.3.8
&
Repair/Replace Front Fork Assembly
Skill Level:
LSR-M, A&P
Tools:
Hex wrenches
Materials:
Replacement parts
Task Description:
If the fork assembly is bent or twisted as may occur on a very hard landing, the fork arms or
top or bottom plates will have to be replaced as described below. Other parts connected to the
fork assembly can be replaced directly without having to remove the entire fork assembly.
1.
!
Remove front wheel as described in Section 4.3.7 above.
2.
!
Disconnect throttle cable and pull free of throttle pedal.
3.
!
Unbolt brake master cylinder at both ends and tie back from fork assembly. You will
have to route the brake line away from the fork assembly. DO NOT disconnect brake
hydraulic line.
4.
!
Remove nut from fork pivot bolt.
5.
!
Using 5/32” hex wrench, remove four hex head machine screws from top plate of fork
assembly. Support the fork assembly before removing the last screw as it will fall out
when all 4 screws are removed.
6.
!
Remove the pivot bolt from the root tube along with the top plate.
7.
!
Inspect all pieces to assure all damaged parts will be replaced.
8.
!
Re-assemble with new parts.
Hex bolts on top plate (4)
(5/32” Hex wrench)
Pivot Bolt