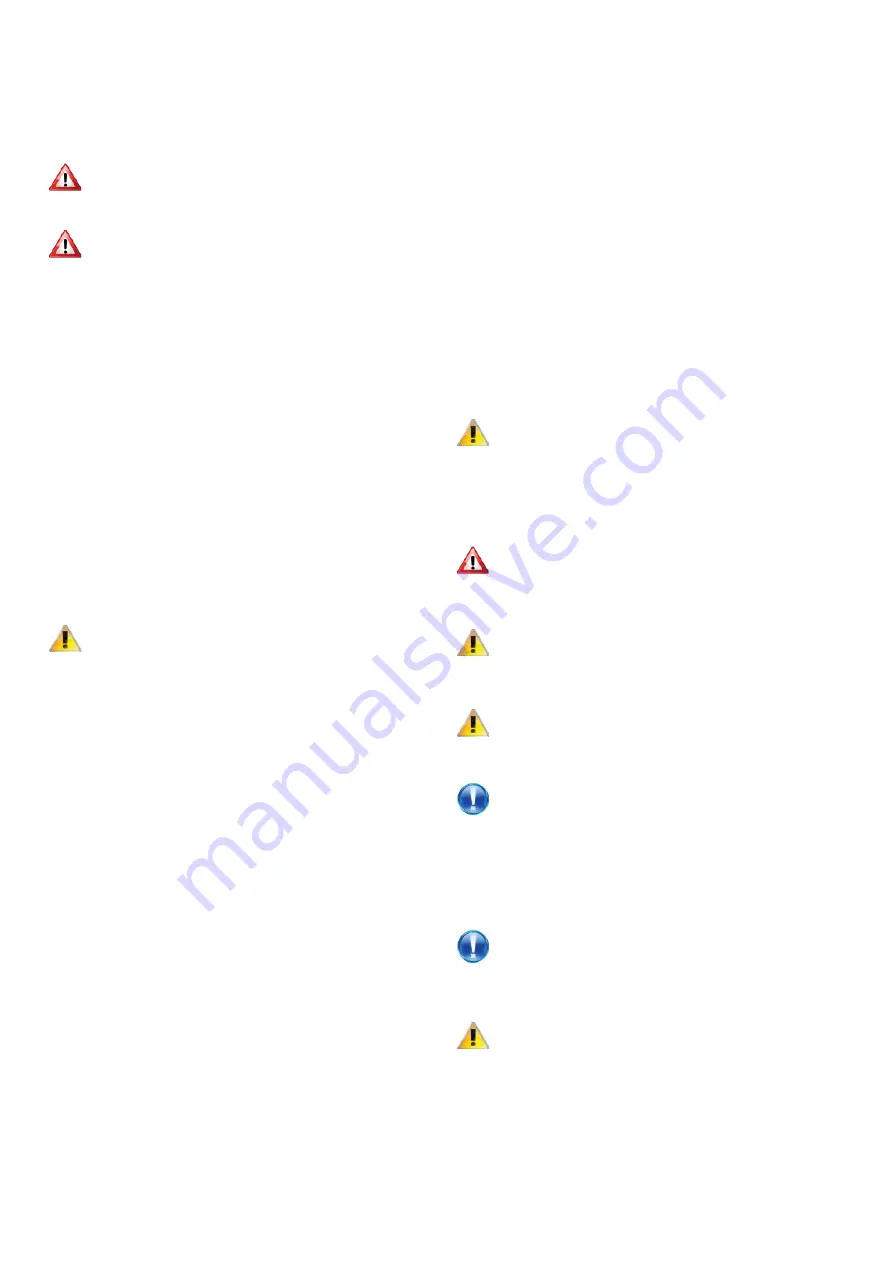
It is advisable to leave the tank unpainted on the inside, but
to paint the outside with a proprietary grade of anti-corrosive
paint.
Warning
A galvanised or open topped tank is strictly not allowed.
Warning
All oil storage tanks require a bund
The Control of Pollution Regulation (Oil Storage) 2001 should
be consulted prior to installation.
1.9.3 Single pipe system (gravity feed)
For installations where the oil tank is 200mm or more above
the level of the fuel pump the principle of gravity feed may be
used.
The draw off point for the supply to the burner must not be
positioned any lower than 100mm above the bottom of the
tank.
Where a return valve is fi tted this must be tamper proof to
prevent inadvertent operation.
C
aution
If the valve is closed when the pump is running the oil
pressure can be increased suffi
ciently so as to cause damage
to the seals within the pump.
The return oil should preferably be discharged through an
elbow onto a tank plate situated within the tank, this should
be positioned so as not to introduce air or air bubbles into the
draw off pipe.
1.9.4 Two pipe system
This is used where the oil storage tank is lower than the pump.
Access for the fuel feed to the burner should be via a suitable
tapping made in the top of the tank, and the fuel feed pipe
should extend to not less than 100mm above the bottom of
the tank.
A none return valve with a metal to metal seat should be
fi tted, especially if the return pipe work is terminated at a
level above the draw off tube. The non- return valve must be
removable for service and maintenance purposes, and the
return pipe from the pump must therefore be extended down
into the tank to the same level as the suction pipe.
The presence of a tamper proof isolating valve fi tted within
the return pipe is only required if there is a risk that oil will
siphon out of the tank if the return pipe is disconnected at the
pump during maintenance or servicing and if the none return
valve has been omitted.
1.9.5 Pressurised ring main system
This system is used to supply a number of units from a
common storage tank.
A booster pump is used to provide the pressure to push the oil
around the ring main and back to the tank.
Pressure reducing valves should be fi tted on the delivery pipe
to each heater to ensure that the pressure at the burner pump
is less than 6 psi.
Caution
The internal by-pass plug must be removed from the burner
pump when used in a pressurised ring main application.
1.9.6 Pipe work and fi ttings
Warning
Galvanised or plastic pipe work and fi ttings must not be used.
(see BS 5410 Part 1 1997)
Caution
All joints must be sealed properly, if necessary using PTFE tape
or other approved sealing media.
Caution
The pipe work must be eff ectively sealed so as to prevent the
ingress of air.
Note:
It is advisable to check all pipe work prior to installation to
ensure that there is no loose debris or scale present.
Black iron pipes can be hammered to assist in the removal of
these contaminants.
Note:
The oil feed to each heater must be fi tted with a fi re check
valve and isolating valve.
Caution
The fi re check valve must be operated by way of a fusible link
positioned so that it is above the burner.
Summary of Contents for Reznor 120
Page 28: ...Wiring Diagram 20 45 600 30 40 ON OFF Riello Burner Integral SC SZ 230 50 1ph...
Page 29: ...Wiring Diagram 20 45 601 60 85 ON OFF Riello Burner Integral SC SZ 230 50 1ph...
Page 30: ...Wiring Diagram 20 45 602 120 135 ON OFF Riello Burner Integral SC SZ 230 50 1ph...
Page 31: ...Wiring Diagram 20 45 603 60 300 ON OFF Riello Burner Integral SC SZ 415 50 3ph...
Page 32: ...Wiring Diagram 20 45 616 30 40 ON OFF Riello Burner Remote SC SZ 230 50 1ph...
Page 33: ...Wiring Diagram 20 45 617 60 85 ON OFF Riello Burner Remote SC SZ 230 50 1ph...
Page 34: ...Wiring Diagram 20 45 618 120 135 ON OFF Riello Burner Remote SC SZ 230 50 1ph...
Page 35: ...Wiring Diagram 20 45 619 60 300 ON OFF Riello Burner Remote SC SZ 415 50 3ph...
Page 36: ...Wiring Diagram 20 45 604 30 40 ON OFF Riello Burner Integral CP4 230 50 1ph...
Page 37: ...Wiring Diagram 20 45 605 60 85 ON OFF Riello Burner Integral CP4 230 50 1ph...
Page 38: ...Wiring Diagram 20 45 606 120 135 ON OFF Riello Burner Integral CP4 230 50 1ph...
Page 39: ...Wiring Diagram 20 45 607 60 300 ON OFF Riello Burner Integral CP4 415 50 3ph...
Page 40: ...Wiring Diagram 20 45 620 30 40 ON OFF Riello Burner Remote CP4 230 50 1ph...
Page 41: ...Wiring Diagram 20 45 621 60 85 ON OFF Riello Burner Remote CP4 230 50 1ph...
Page 42: ...Wiring Diagram 20 45 622 120 135 ON OFF Riello Burner Remote CP4 230 50 1ph...
Page 43: ...Wiring Diagram 20 45 623 60 300 ON OFF Riello Burner Remote CP4 415 50 3ph...
Page 44: ...Wiring Diagram 20 45 612 30 40 ON OFF Riello Burner No Controls 230 50 1ph...
Page 45: ...Wiring Diagram 20 45 613 60 85 ON OFF Riello Burner No Controls 230 50 1ph...
Page 46: ...Wiring Diagram 20 45 614 120 135 ON OFF Riello Burner No Controls 230 50 1ph...
Page 47: ...Wiring Diagram 20 45 615 60 300 ON OFF Riello Burner No Controls 415 50 3ph...
Page 55: ...5 Parts Lists...
Page 66: ...Notes...
Page 67: ...Notes...