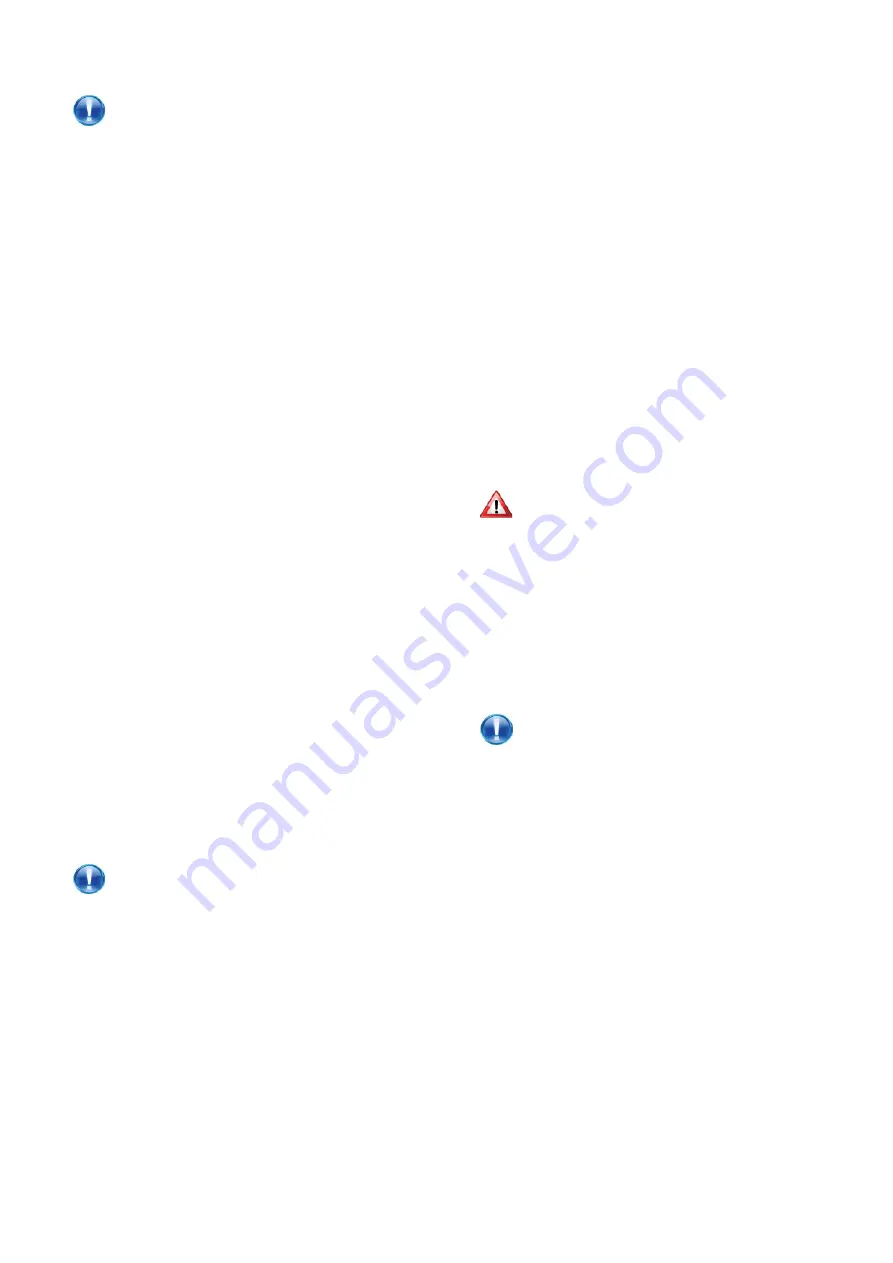
Note:
The maximum displacement at the mid point of the top edge
of the belt must not be greater than 16mm per metre of span,
when a force of 3kg is applied in a plane perpendicular to the
belt.
(a) Loosen fan motor securing bolts on chassis.
(b) Loosen fan motor slide adjustment bolt.
(c) Slide fan motor towards fan to slacken belts.
(d) Replace belts, pull fan motor away from fan until belts are
tight.
(e) Tighten adjustment bolt to hold motor.
(f) Tighten fan securing bolts ensuring that the fan is square
and the pulleys aligned.
(g) Check belt tension, making fi nal adjustments as necessary.
(h) Tighten and clamp fasteners to hold fan motor in position.
4.2.6 Heat Exchanger
The heat exchanger requires a visual inspection at least once
per year, this should be accompanied by cleaning.
It is recommended that a fl ue brush and vacuum cleaner be
used to facilitate this.
Access to the heat exchanger is gained through the removal of
the rear upper panel and heat shield.
Servicing and cleaning should be performed as follows:
(a) Remove brass nuts and cover from heat exchanger end
assembly to expose heat exchanger tubes.
(b) Remove any accumulated deposits from the tubes.
(c) Particular attention should be paid to the upper internal
surfaces of the tubes, where through convection heavier
deposition is likely to occur.
(d) Any deposits which may have accumulated within the
combustion chamber can be removed with a vacuum cleaner
once the burner is removed.
Note:
It is most important that a build up of deposits is not allowed
to occur as this can have an adverse eff ect upon the effi
ciency
of the heater and reduce the life of the heat exchanger.
(e) The heat exchanger and combustion chamber should be
visually inspected for signs of splits, cracks, and distortion.
(f) All gaskets should be checked to ensure that they continue
to provide a gas tight seal, if there is an element of doubt then
they should be replaced.
If the condition of the heat exchanger gives cause for concern
the suppliers Service Department should be advised pending
a more detailed examination. Details on rear page
4.2.7 Electrical Supply
All connections must be checked to ensure that they are
secure, and free from corrosion.
Terminals and connections should also be checked to ensure
that no stray strands are bridging terminals.
Electrical continuity should also be checked.
4.2.8 Oil Supply
The oil supply pipe work, tank, and fi ttings should all be
inspected to ensure that they are free from corrosion, and to
ensure that where brackets have been fi tted these remain
secure and off er adequate support.
The oil fi lter should be replaced with a new one, and the
system should be checked for leaks. If the oil level is such to
allow removal of any sludge or other contaminants form the
tank this too should be undertaken, particularly if there have
been problems of poor fi ring associated with contaminants
reaching the burner.
Warning
Any waste oil or sludge must be disposed of correctly. Never
dispose of it by dumping or tipping it down drains or into
watercourses where ground water can become polluted and
environmental damage caused.
4.2.9 Burner
Service requirements for the burner fi tted to the cabinet
heater are covered in the separate manual prepared by the
burner manufacturer.
Note:
It is most important that the burner is serviced regularly and
in accordance with the manufacturers instructions.
4.2.10 Air Delivery System
A visual inspection should be undertaken to ensure that the
air delivery system is in good order, that it remains adequately
supported and that the various joints are eff ectively sealed.
4.2.11 Report
A full and detailed service report should be prepared, it is
advised that the report is not completed until the heater has
been re-commissioned, where upon the completed report
can then be run through with the user.
4.3
Service Re-commissioning
The heater should be re-commissioned as follows, as per
section 3.1 through to section 3.4 inclusive.
This must be regarded as a necessary part of the heater
service. By the service engineer.
Summary of Contents for Reznor 120
Page 28: ...Wiring Diagram 20 45 600 30 40 ON OFF Riello Burner Integral SC SZ 230 50 1ph...
Page 29: ...Wiring Diagram 20 45 601 60 85 ON OFF Riello Burner Integral SC SZ 230 50 1ph...
Page 30: ...Wiring Diagram 20 45 602 120 135 ON OFF Riello Burner Integral SC SZ 230 50 1ph...
Page 31: ...Wiring Diagram 20 45 603 60 300 ON OFF Riello Burner Integral SC SZ 415 50 3ph...
Page 32: ...Wiring Diagram 20 45 616 30 40 ON OFF Riello Burner Remote SC SZ 230 50 1ph...
Page 33: ...Wiring Diagram 20 45 617 60 85 ON OFF Riello Burner Remote SC SZ 230 50 1ph...
Page 34: ...Wiring Diagram 20 45 618 120 135 ON OFF Riello Burner Remote SC SZ 230 50 1ph...
Page 35: ...Wiring Diagram 20 45 619 60 300 ON OFF Riello Burner Remote SC SZ 415 50 3ph...
Page 36: ...Wiring Diagram 20 45 604 30 40 ON OFF Riello Burner Integral CP4 230 50 1ph...
Page 37: ...Wiring Diagram 20 45 605 60 85 ON OFF Riello Burner Integral CP4 230 50 1ph...
Page 38: ...Wiring Diagram 20 45 606 120 135 ON OFF Riello Burner Integral CP4 230 50 1ph...
Page 39: ...Wiring Diagram 20 45 607 60 300 ON OFF Riello Burner Integral CP4 415 50 3ph...
Page 40: ...Wiring Diagram 20 45 620 30 40 ON OFF Riello Burner Remote CP4 230 50 1ph...
Page 41: ...Wiring Diagram 20 45 621 60 85 ON OFF Riello Burner Remote CP4 230 50 1ph...
Page 42: ...Wiring Diagram 20 45 622 120 135 ON OFF Riello Burner Remote CP4 230 50 1ph...
Page 43: ...Wiring Diagram 20 45 623 60 300 ON OFF Riello Burner Remote CP4 415 50 3ph...
Page 44: ...Wiring Diagram 20 45 612 30 40 ON OFF Riello Burner No Controls 230 50 1ph...
Page 45: ...Wiring Diagram 20 45 613 60 85 ON OFF Riello Burner No Controls 230 50 1ph...
Page 46: ...Wiring Diagram 20 45 614 120 135 ON OFF Riello Burner No Controls 230 50 1ph...
Page 47: ...Wiring Diagram 20 45 615 60 300 ON OFF Riello Burner No Controls 415 50 3ph...
Page 55: ...5 Parts Lists...
Page 66: ...Notes...
Page 67: ...Notes...