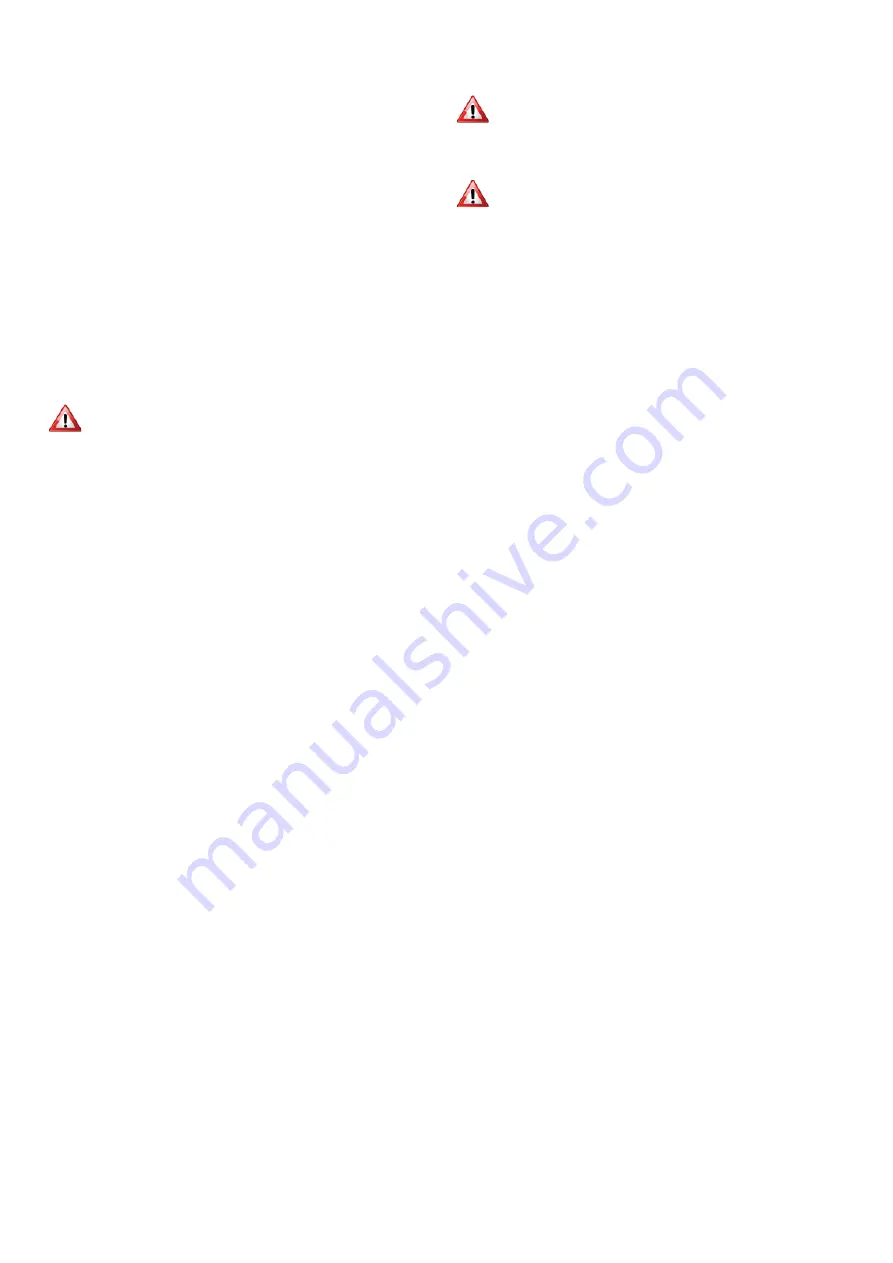
2.6
Oil Installation/connection
The oil tank must be positioned so that there is a fall of 7.5mm
(+/- 2.5mm) for every 30mm away from the outlet and towards
the sludge/drain valve, which must be sited at the lowest
point in the tank. If the tank is positioned on supports then
there must be an adequate protective layer between tank and
support to prevent damage or deterioration through
corrosion.
It is strongly suggested that reference is made to BS 5410 ; part
2 ; 1978.
It is also suggested that the installer is familiar with the detail
and requirements contained within sections 1.9 of this manual
prior to commencing installation.
Warning
Prolonged exposure and contact with Gas Oil can result in the
natural oils being removed from the skin, sensitisation can
result in dermatitis.
Always ensure that the appropriate personal protective
equipment is used.
2.7
Electrical Installation/connection
Cabinet heaters are available either for 415V 50Hz 3PH or 230V
50Hz 1PH supplies depending upon the model specifi ed.
It is recommended that reference is made to the wiring
diagrams contained within section 2.11 of this manual prior to
installation or connection to the supply. The electrical supply
must be as specifi ed and suitable for the heater, and must
be run within conduit to a point adjacent to the heater, and
be terminated to provide an isolation point that will prevent
remote or inadvertent activation.
Cables, conduit, and fi ttings that are used to make the
connection between the isolator and the heater must conform
to the appropriate IEE regulations.
All heaters are supplied fused and pre-wired, all must be
earthed.
Final connections for any additional external controls must be
completed on site, and must be carried out according to IEE
regulations.
Separate user information is provided for the time control unit
and the burner, and forms part of the product information
pack which accompanies every heater when despatched.
Warning
Always isolate from mains electrical supply before
commencing work on the heater.
Warning
Always ensure that the appropriate personal protective
equipment is used.
2.8
Air Distribution Installation
The materials selected must be of low heat capacity, and it is
preferable that all warm air ductwork is thermally insulated.
Where ducting may be subject to deterioration from exposure
to moisture or high humidity material selection and insulation
are prime considerations. Joints and seams must be airtight
and fastened securely and designed to remain so, even when
operating at high temperatures.
Adequate support must be designed into the layout of the
ductwork to ensure that the integrity of the seams and joints
is maintained. The support must be independent and
separate from the heater and the ducting, to allow for free
movement during expansion and contraction.
Where ducting passes through walls or partitions suffi
cient
clearance must be left, irrespective of any fi re stop
requirement, to allow for expansion and contraction. Failure to
adhere to these latter two points can result in the generation
and transmission of excess noise.
Where ducting is installed in concrete fl ooring a permanent
membrane must be used to isolate the ducting from the
corrosive eff ect of the alkaline salts within the concrete. Care
should be taken to ensure that soft insulation material does
not become compressed and thereby lose its insulation
eff ectiveness.
2.9
Warm Air Registers
In order that vertical temperature gradients are minimal
thereby providing a more even heat distribution, it is
preferable to install warm air registers at low wall levels or at
fl oor level, with the size, number, and position commensurate
with the requirement of the application.
To minimise noise levels the registers should be set away from
corners, additionally, a good seal between the register frame
and the wall is important, particularly on high level positions,
if unsightly staining through warm air/particulate deposition is
to be avoided.
Summary of Contents for Reznor 120
Page 28: ...Wiring Diagram 20 45 600 30 40 ON OFF Riello Burner Integral SC SZ 230 50 1ph...
Page 29: ...Wiring Diagram 20 45 601 60 85 ON OFF Riello Burner Integral SC SZ 230 50 1ph...
Page 30: ...Wiring Diagram 20 45 602 120 135 ON OFF Riello Burner Integral SC SZ 230 50 1ph...
Page 31: ...Wiring Diagram 20 45 603 60 300 ON OFF Riello Burner Integral SC SZ 415 50 3ph...
Page 32: ...Wiring Diagram 20 45 616 30 40 ON OFF Riello Burner Remote SC SZ 230 50 1ph...
Page 33: ...Wiring Diagram 20 45 617 60 85 ON OFF Riello Burner Remote SC SZ 230 50 1ph...
Page 34: ...Wiring Diagram 20 45 618 120 135 ON OFF Riello Burner Remote SC SZ 230 50 1ph...
Page 35: ...Wiring Diagram 20 45 619 60 300 ON OFF Riello Burner Remote SC SZ 415 50 3ph...
Page 36: ...Wiring Diagram 20 45 604 30 40 ON OFF Riello Burner Integral CP4 230 50 1ph...
Page 37: ...Wiring Diagram 20 45 605 60 85 ON OFF Riello Burner Integral CP4 230 50 1ph...
Page 38: ...Wiring Diagram 20 45 606 120 135 ON OFF Riello Burner Integral CP4 230 50 1ph...
Page 39: ...Wiring Diagram 20 45 607 60 300 ON OFF Riello Burner Integral CP4 415 50 3ph...
Page 40: ...Wiring Diagram 20 45 620 30 40 ON OFF Riello Burner Remote CP4 230 50 1ph...
Page 41: ...Wiring Diagram 20 45 621 60 85 ON OFF Riello Burner Remote CP4 230 50 1ph...
Page 42: ...Wiring Diagram 20 45 622 120 135 ON OFF Riello Burner Remote CP4 230 50 1ph...
Page 43: ...Wiring Diagram 20 45 623 60 300 ON OFF Riello Burner Remote CP4 415 50 3ph...
Page 44: ...Wiring Diagram 20 45 612 30 40 ON OFF Riello Burner No Controls 230 50 1ph...
Page 45: ...Wiring Diagram 20 45 613 60 85 ON OFF Riello Burner No Controls 230 50 1ph...
Page 46: ...Wiring Diagram 20 45 614 120 135 ON OFF Riello Burner No Controls 230 50 1ph...
Page 47: ...Wiring Diagram 20 45 615 60 300 ON OFF Riello Burner No Controls 415 50 3ph...
Page 55: ...5 Parts Lists...
Page 66: ...Notes...
Page 67: ...Notes...