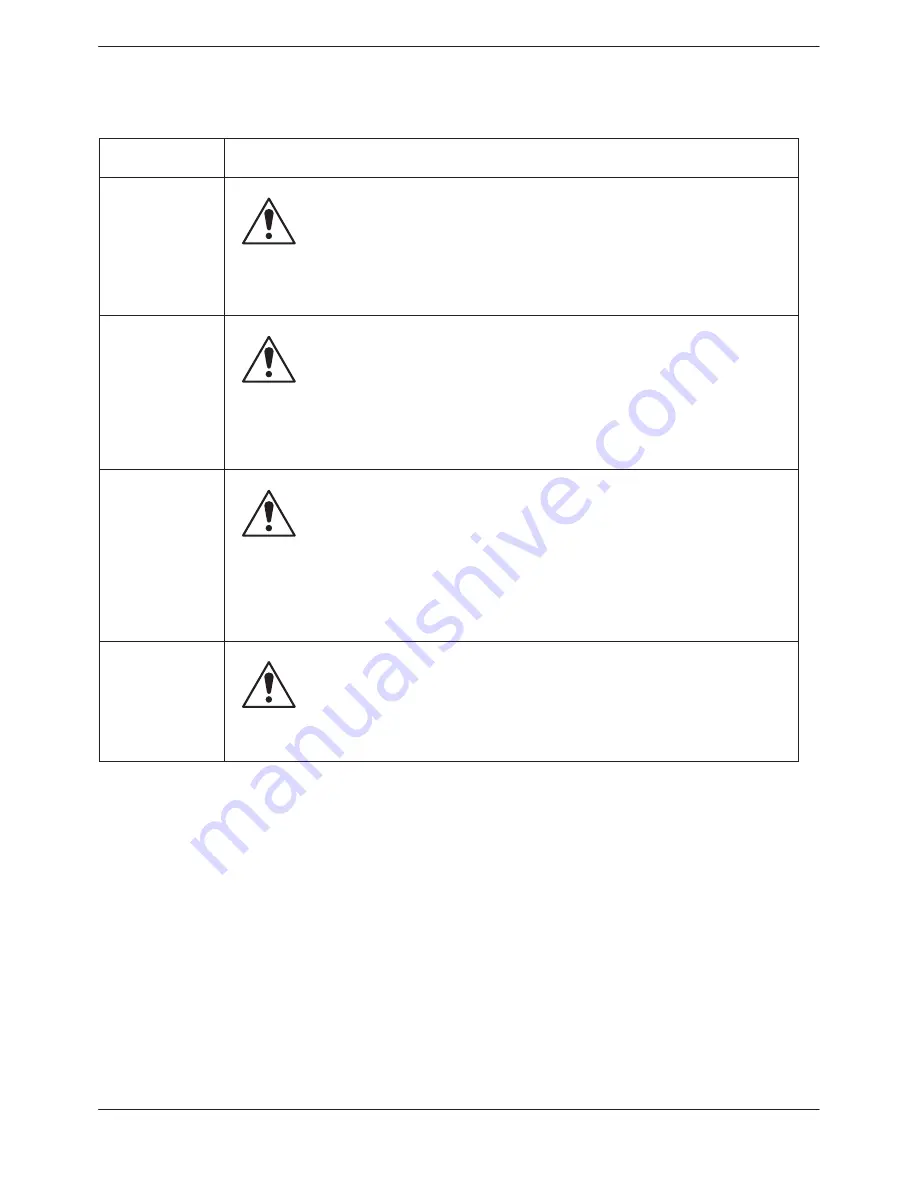
LA 404 Pattern Control System
8
Part 1037527
B
!
200
5
Nordson Corporation
Manual 66-LA404-MA-01
General Safety Warnings and Cautions
(contd)
Table 1 General Safety Warnings and Cautions
(contd)
Equipment
Type
Warning or Caution
HM, PC
WARNING:
Equipment starts automatically! Remote triggering
devices are used to control automatic hot melt guns. Before working
on or near an operating gun, disable the gun’s triggering device and
remove the air supply to the gun’s solenoid valve(s). Failure to
disable the gun’s triggering device and remove the supply of air to the
solenoid valve(s) can result in personal injury.
HM, CA, PC
WARNING:
Risk of electrocution! Even when switched off and
electrically isolated at the disconnect switch or circuit breaker, the
equipment may still be connected to energized auxiliary devices.
De-energize and electrically isolate all auxiliary devices before
servicing the equipment. Failure to properly isolate electrical power to
auxiliary equipment before servicing the equipment can result in
personal injury, including death.
CA
WARNING:
Risk of fire or explosion! Nordson cold adhesive
equipment is not rated for use in explosive environments and should
not be used with solvent-based adhesives that can create an
explosive atmosphere when processed. Refer to the MSDS for the
adhesive to determine its processing characteristics and limitations.
The use of incompatible solvent-based adhesives or the improper
processing of solvent-based adhesives can result in personal injury,
including death.
HM, CA, PC
WARNING:
Allow only personnel with appropriate training and
experience to operate or service the equipment. The use of untrained
or inexperienced personnel to operate or service the equipment can
result in injury, including death, to themselves and others and can
damage to the equipment.
Summary of Contents for LA 404
Page 28: ......