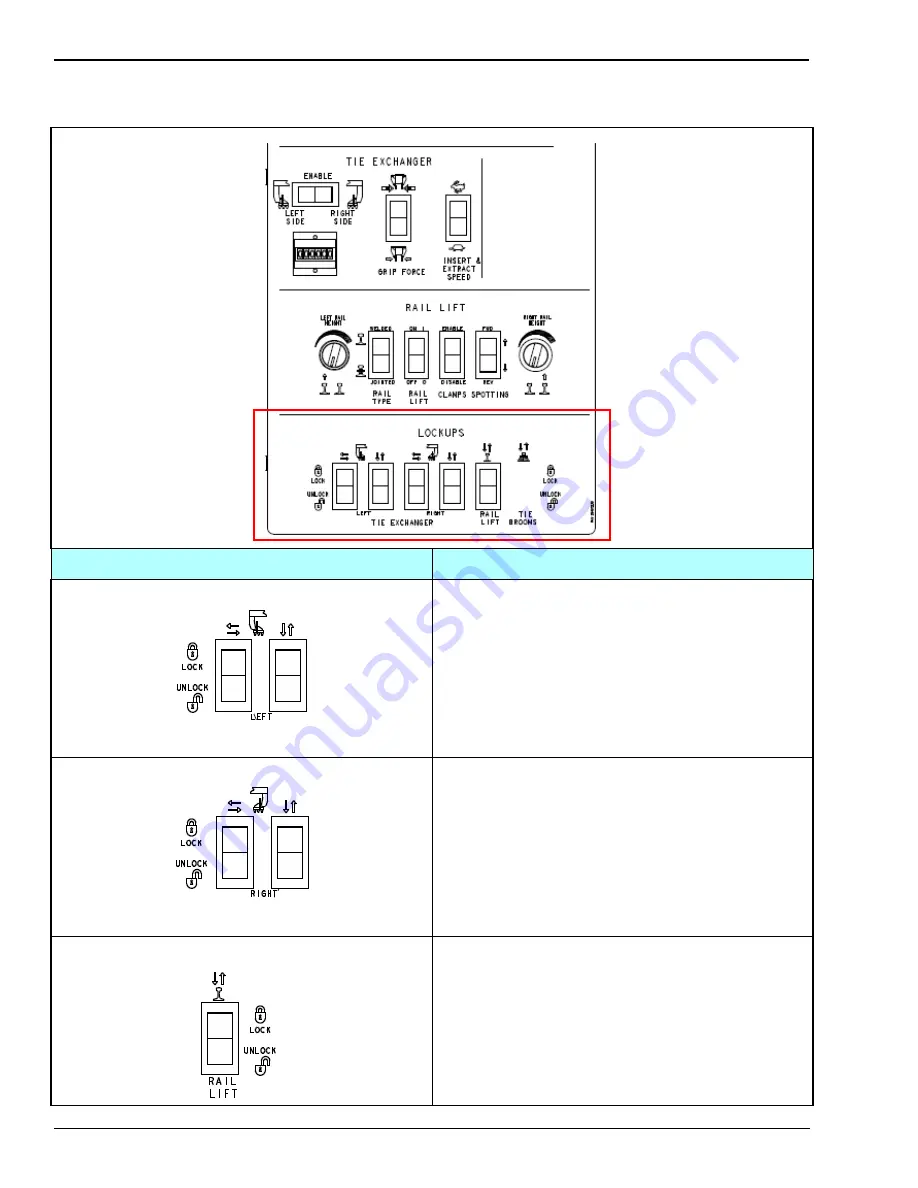
3-2 MAR 2016 49457610 TRIPP HD RevB
LOCKUPS
LOCKUP CONTROLS
CONTROL
DESCRIPTION
Left Tie Exchanger Lock and Unlock Switches
Located on the left side of the lock/unlock console,
these switches control the pneumatic locks on the left
side tie exchanger. One switch controls the up/down
movement; the other switch controls lateral movement.
LOCK: Controls the pneumatic cylinders to place the
mechanical locks on the hydraulic cylinders of the left
side.
UNLOCK: Controls the pneumatic cylinders to release
the mechanical locks on the hydraulic cylinders.
Right Tie Exchanger Lock and Unlock Switches
Located on the center of the lock/unlock console, these
switches control the pneumatic locks on the right side
tie exchanger. One switch controls the up/down
movement; the other switch controls lateral movement.
LOCK: Controls the pneumatic cylinders to place the
mechanical locks on the hydraulic cylinders on the
right side.
UNLOCK: Controls the pneumatic cylinders to release
the mechanical locks on the hydraulic cylinders.
Rail Lift Workhead Lock and Unlock Switches
Located on the right side of the lock/unlock console,
this switch controls the pneumatic locks on the rail lift
hydraulic cylinders.
LOCK: Controls the pneumatic cylinders to place
mechanical locks on the hydraulic lift cylinders.
UNLOCK: Controls the pneumatic cylinders to release
the mechanical locks on the hydraulic cylinders.
Summary of Contents for TRIPP HD
Page 6: ......
Page 10: ...Contents 4 MAR 2016 49457607 HD TRIPP RevB TABLE OF CONTENTS...
Page 18: ...1 8 MAR 2016 49457607 TRIPP HD RevB SAFETY INSTRUCTIONS AND INFORMATION...
Page 26: ...3 4 MAR 2016 49457610 TRIPP HD RevB LOCKUPS...
Page 32: ...4 6 MAR 2016 49457610 TRIPP HD RevB GENERAL MACHINE SPECIFICATIONS...
Page 52: ...5 20 MAR 2016 49457610 TRIPP HD RevB OPERATOR SYSTEM FAMILIARIZATION...
Page 60: ...7 2 MAR 2016 49457610 TRIPP HD RevB ROUTINE MAINTENANCE Figure 7 1 RAIL CLAMP LUBE CHART...
Page 62: ...7 4 MAR 2016 49457610 TRIPP HD RevB ROUTINE MAINTENANCE Figure 7 3 TIE EXCHANGER LUBE CHART...
Page 82: ...7 24 MAR 2016 49457610 TRIPP HD RevB ROUTINE MAINTENANCE...