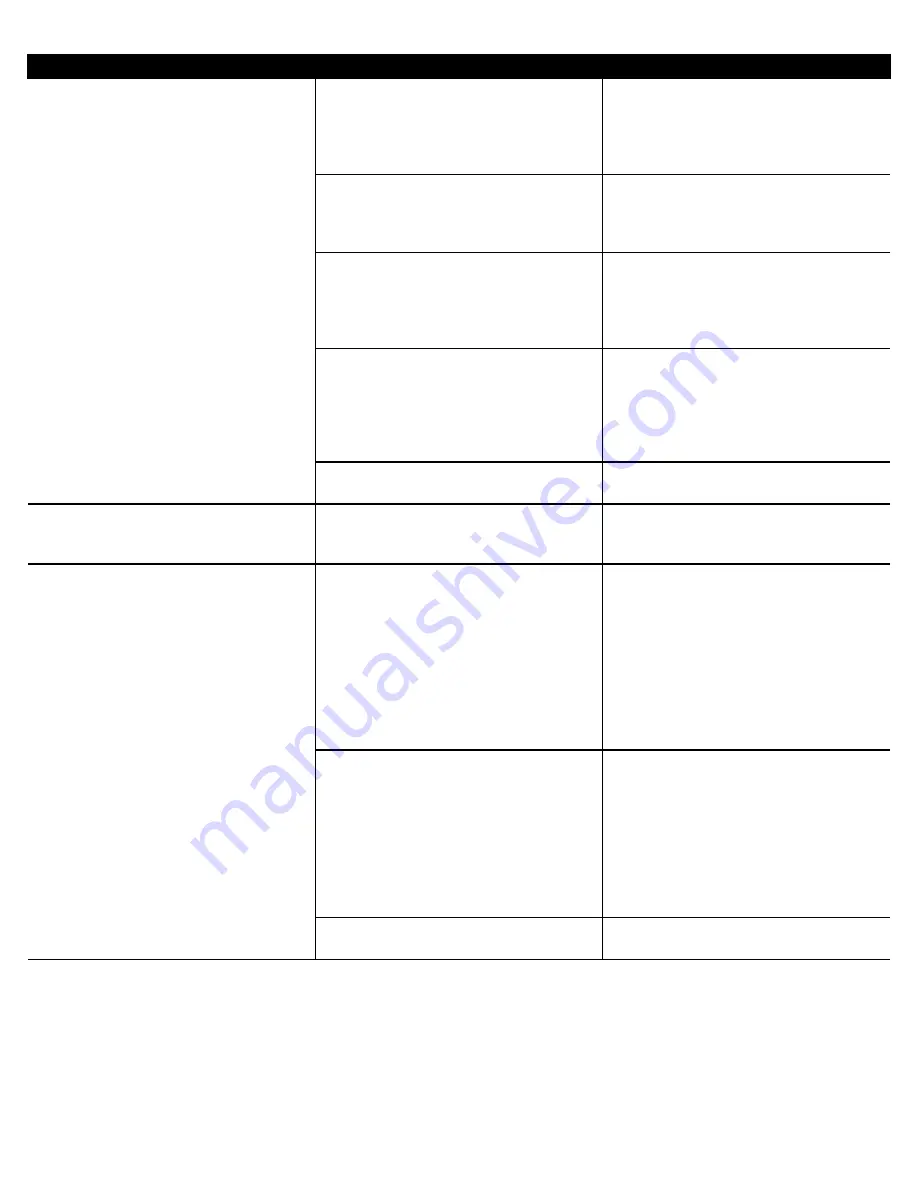
5
Condition/Problem
Things to Check
Solution
11.
Heart rate not displayed while using chest
strap (if equipped)
11.1
Transmitter not making good contact with
skin
Make sure heart rate monitor is under clothing,
against the skin, and as high under the pectoral
muscles as is comfortable. Use saline solution (sa-
liva or contact lens solution) to wet the electrode
areas on the sensor unit.
11.2
Electromagnetic interference
Turn off any television, AM radio, microwave, or
computer within 6 feet (2 meters) of the Mobia™
fitness machine. Try positioning the machine in
another area.
11.3
Chest strap transmitter
Test chest strap with another HR monitoring
device such as HR watch or a machine at a gym.
If transmitter has good skin contact and still is
not found to be emitting HR signal replace HR
TRANSMITTER.
11.4
HR receiver connection
If chest strap is known to work with other devices
and no sources of interference are present, or if
console has been tested with a Pulse Simulator
and is not receiving the signal, check HR receiver
connection at back of upper electronics board
(remove panel on underside of console for access).
11.5
Upper electronics
If above steps have not resolved issue replace
UPPER CONSOLE
12.
“Tick” sound once per revolution or scraping
noise from under treadle
12.1
Belt alignment
Belt seam may be contacting metal belt guide
under treadle. Slight adjustment of belt should
alleviate noise.
13.
Treadles don’t operate as expected
13.1
Customer perception
Some new owners may not realize that the
Treadles do not move up and down on their own.
Make sure that the customer understands that the
Treadle movement is generated by their walking
motion. Also make sure that they understand the
Treadles will not normally go through their full
range of motion as would a stepper; the Treadles
usually move only a few inches to cushion each
footstep. Customers should walk normally and not
try to force Treadle movement.
13.2
Hydraulic shocks
If customer feels that resistance is uneven from
one Treadle to the other, first start off with the in
-
tensity setting equal on each hydraulic. The white
dial indicator triangle on each hydraulic shock
should also be facing towards the user when they
are on the machine. Adjust one shock only in small
increments until Treadle travel matches. A higher
setting increases travel, while a lower setting
reduces it.
13.3
Treadle binding
If Treadles are “hanging up” as they pass each
other then replace friction block.