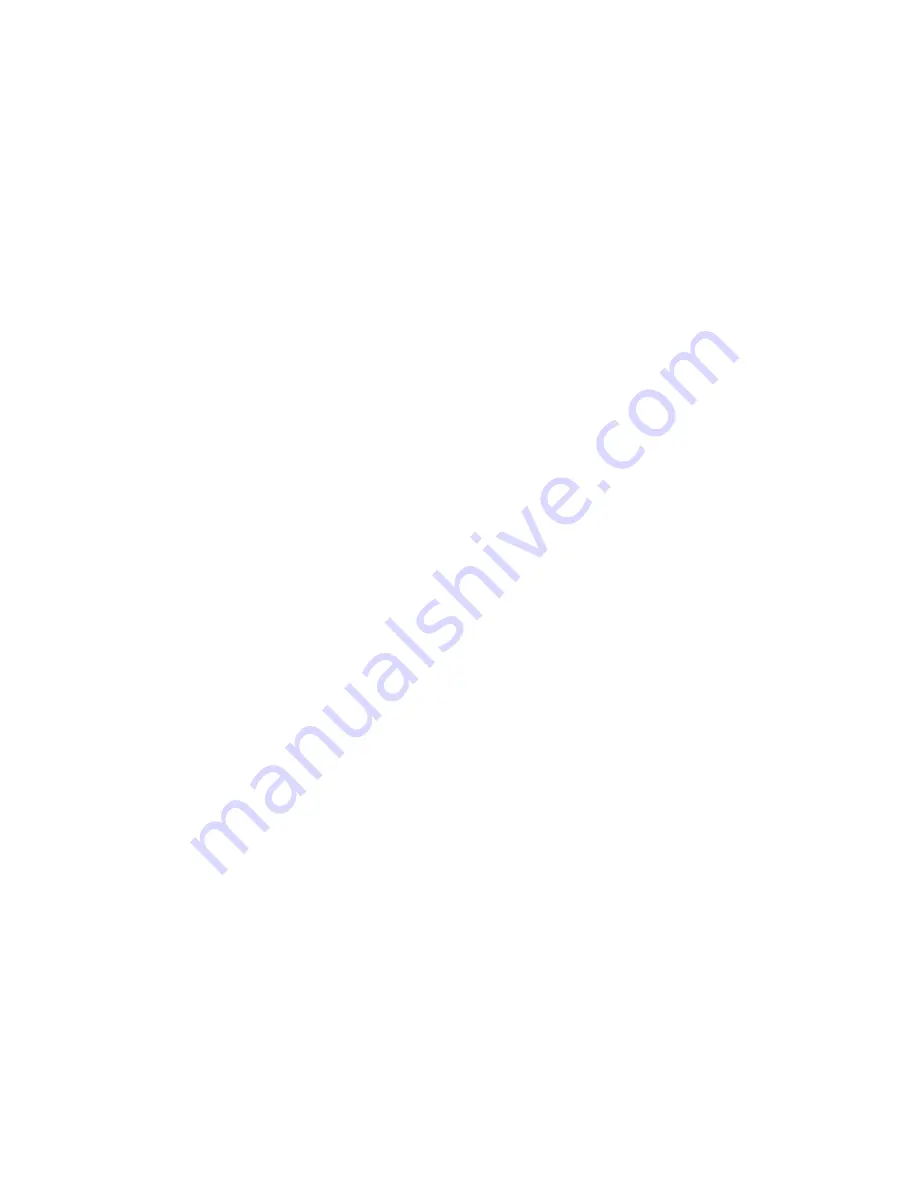
RADIOBEACON TRANSMITTER
ND500II (125 WATTS) DOUBLE SIDEBAND - NO VOICE
Page 5-5
15 September 2003
(l)
Disconnect test leads of variable DC power
supply.
(m) Install the shunt post on position ‘A’ of header
E5 on the RF synthesizer PWB A9.
(n)
Set
POWER
switch S3 to
ON
and observe that
requirements of steps (f), (g) and (h) are met.
(o)
Connect a frequency counter between RF drive
test point A2TP4 and ground.
(p)
Frequency counter indication should be within
0.0005 percent of assigned RF carrier
frequency. If necessary, set switches S1
through S5 on the RF synthesizer PWB (A9).
(q)
Disconnect frequency counter and connect an
oscilloscope between RF drive test point
A2TP4 and ground.
(r)
Oscilloscope indication should be similar to the
waveform depicted in example 'C' (carrier
frequencies between 190 and 849 kHz) or ‘D’
(carrier frequencies between 850 kHz and 1800
kHz) of figure 6-1. The waveform should be
between 46 and 60 volts peak-to-peak.
(s)
Disconnect oscilloscope from A2TP4.
(t)
Connect a digital multimeter, set to measure
DC volts, between the cathode of A2CR3 (+)
and ground.
(u)
Digital multimeter indication should be between
23.0 and 33.0V.
(v)
Disconnect digital multimeter from A2CR3.
5.3.4
PULSE WIDTH MODULATOR/
MOD DRIVE ALARM CHECK
: Verify the
frequency and ramp of the variable pulse width
modulator circuit are their required levels and the
mod drive-alarm circuit is functioning, as follows:
(a)
Verify the requirements of paragraph 5.3.2
have been completed, paying particular
attention to the requirements of paragraph
5.3.2.2.
(b)
Adjust
RAMP ADJ
potentiometer A4R26 fully
clockwise.
(c)
Connect a shorting jumper across resistor
A4R27.
(d)
Set or verify switches are set as tabulated for
Calibration Setting
in table 4-1.
(e)
Connect a frequency counter between ramp
integrator test point A4TP3 and ground.
(f)
Frequency counter indication should be between
69.8 and 70.2kHz.
(g)
If necessary, adjust
PWM FREQ
trimmer
capacitor A4C11 to meet requirements of step
(f).
(h)
Disconnect frequency counter from A4TP3.
(i)
Connect an oscilloscope between balance drive
test point A4TP4 and ground.
(j)
Simultaneously monitor oscilloscope waveform
and slowly adjust
O/P PWR
potentiometer
A4R31 clockwise until
MOD DRIVE
ALARM
lamp DS3 just turns on.
(k)
Oscilloscope waveform observed in step (j)
shall be a rectangular waveform and the
duration of the positive going portion of the
waveform shall increase as
O/P PWR
potentiometer A4R31 is adjusted clockwise (see
example 'I' of figure 6-1).
(l)
The mod drive-alarm threshold (when
MOD
DRIVE ALARM
lamp DS3 just turns on) shall
occur when the positive going portion of the
rectangular waveform observed in step (j) is
between sixty and seventy percent of the
complete waveform period.
(m) Set
POWER
switch S3 to
OFF
.
(n)
Disconnect oscilloscope from A4TP4.
(o)
Set
O/P PWR
potentiometer A4R31 fully
counter clockwise.
(p)
Remove shorting jumper from resistor A4R27.