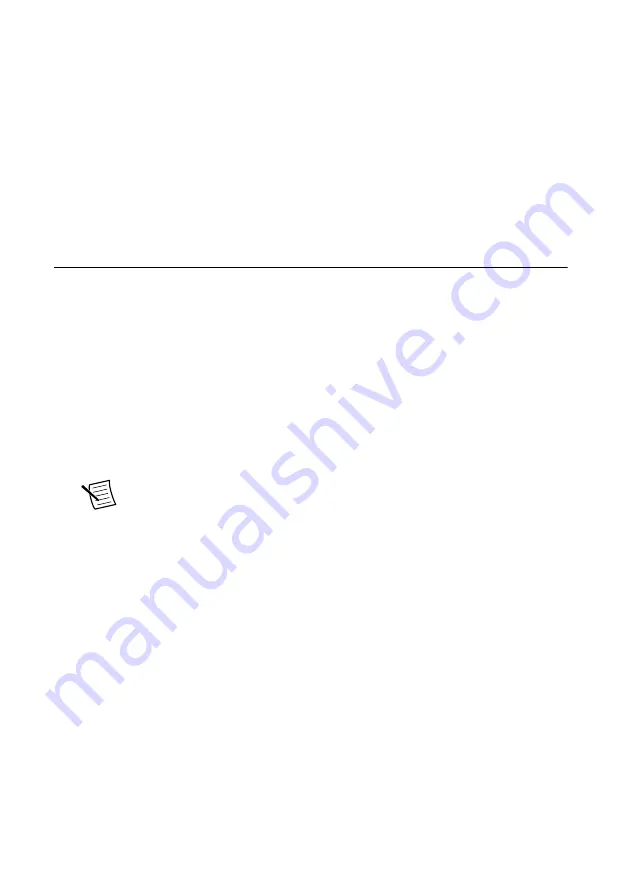
•
Keep connections to the device as short as possible. Long cables and wires act as
antennas, picking up extra noise that can affect measurements.
•
Verify that all connections to the device are secure.
•
Use shielded copper wire for all cable connections to the device. Use twisted-pairs wire
to eliminate noise and thermal offsets.
•
Maintain an ambient temperature of 23 ±5 °C. The device temperature will be greater
than the ambient temperature.
•
Keep relative humidity below 80%.
•
Allow a warm-up time of at least 10 minutes to ensure that the FieldDAQ device
measurement circuitry is at a stable operating temperature.
Calibration Procedure
The calibration process includes the following steps:
1.
on page 3
2.
3.
4.
on page 8
5.
on page 9
Initial Setup
Complete the following steps to set up the FieldDAQ device.
1.
Install the software and NI-DAQmx driver as outlined in the
FD-11613/11614 Quick
Start
.
Note
You must install NI-DAQmx 18.1 or later for device calibration support.
2.
Set up the FieldDAQ device as outlined in the
FD-11613/11614 Quick Start
.
3.
Configure the FieldDAQ device in Measurement & Automation Explorer (NI MAX) as
outlined in the
FD-11613/11614 Quick Start
.
4.
If the FieldDAQ device is not reserved automatically, select the device and click the
Reserve Network Device
button. Refer to
for more
information.
5.
Self-test your device in MAX by expanding
Devices and Interfaces
»
Network Devices
,
right-clicking your FieldDAQ device, and selecting
Self-Test
. Self-test performs a brief
test to determine successful device installation. When the self-test finishes, a message
indicates successful verification or if an error occurred. If an error occurs, refer to
Reserving the Device in MAX
When the FieldDAQ device is connected to a network, multiple users can access the device.
To perform any DAQ functionality on the device, including reset and self-test, you must
reserve the device in MAX. In MAX, an unreserved device or device reserved by another host
FD-11613/11614 Calibration Procedure
|
© National Instruments
|
3