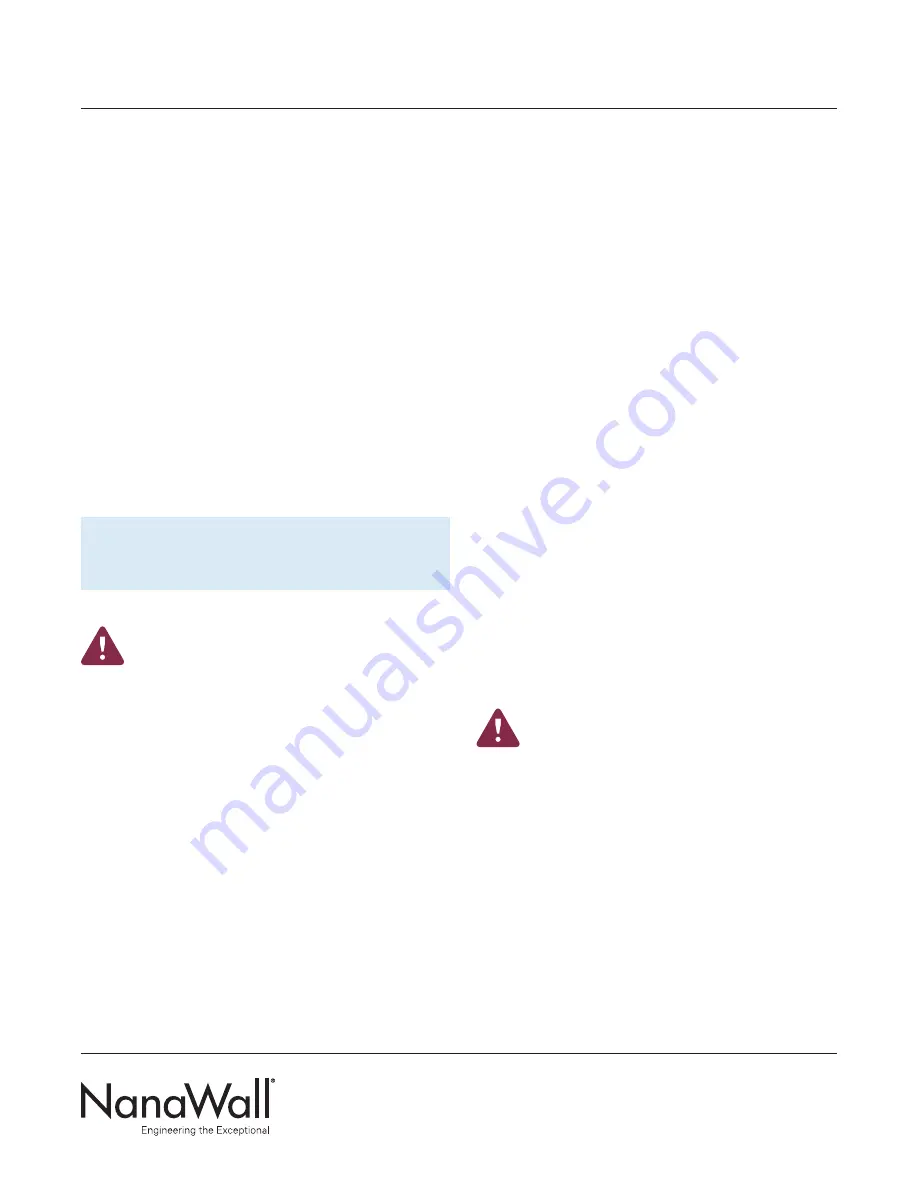
NANAWALL CSW75 OWNER’S MANUAL
8
Now drill the appropriate size hole for the pivot point.
If concrete, use a diamond core drill bit with the proper
diameter size.
Step B6
Install the “half” panel by setting it on top of the bottom
pivot point first and then attach it to the top pivot point
by pushing up the bolt of the top pivot point and screwing
it onto the shoe inside the top clamping profile. Before
you tighten the bolt and nut, measure the horizontal
reveal at the bottom and top and keep it consistent with
the rest of the panels.
Step B7
Now you can attach the half panel (Panel #1) to the
adjacent folding panel (Panel #2) by adding the hinge pin
as described under Step B2.
IMPORTANT:
DO NOT INSTALL ANY SINGLE/
DOUBLE ACTION END PANELS, YET.
Do not drill any additional holes for sockets,
pivot points and floor closers, yet!
C.
GAPS AND ADJUSTMENT
After inserting all the folding panels, operate the unit
and check the vertical and horizontal reveals. Check if
all panels are vertically straight and if you left enough
space for the single/double action end panel.
See Sheet
8 of the Installation Manual.
Between the folding panels
there should be an even gap of 2 mm (about 1/16
"
). Any
problems may be due to the head track not being
absolutely level.
The horizontal spacing between the bottom of a panel
and finish floor should be 7 mm (about 1/4
"
)
consistently
across the width of the opening and 23 mm (7/8
"
) at the
top.
If the gaps are not correct, then adjust the upper track
by removing or adding shims above the head track as
needed. The upper track has to be perfectly level.
If there are still issues on the gap between panels
and
the gap at the bottom not being correct, then
the
running carriages can be adjusted. The carriages on
the
panels are normally set from the factory to have
a gap
of 23 mm (7/8
"
) from the bottom of the head track to the
top of the top rail.
To adjust the height of the panels, use a 19 mm open jaw
wrench from the side. Clamp on the flat part of the bolt
that is located near the bottom of the roller with the
11 mm open jaw wrench and adjust the height.
Counter-clockwise rotation = less floor clearance;
clockwise rotation = more floor clearance.
See Sheet 8 of
the Installation Manual.
After final adjustments make sure to really tighten
down the nut.
After you adjusted all folding panels, measure the width
for the single action end panel (non-sliding) again
and make sure it fits into the opening.
Now you can start drilling holes for sockets!
Do not install the single/double action end
panel, yet!
D. SOCKETS
Holes in the floor for the sockets have to be made at
exact precise spots. There is no second chance if the hole
location is off.
See Sheet 9 of the Installation Manual.
With a laser, find the center line of the head track
on the floor along the length of the opening, and mark
it with a chalk line. Close the unit such that the panels
are in the correct closed positions.
Start with the panel