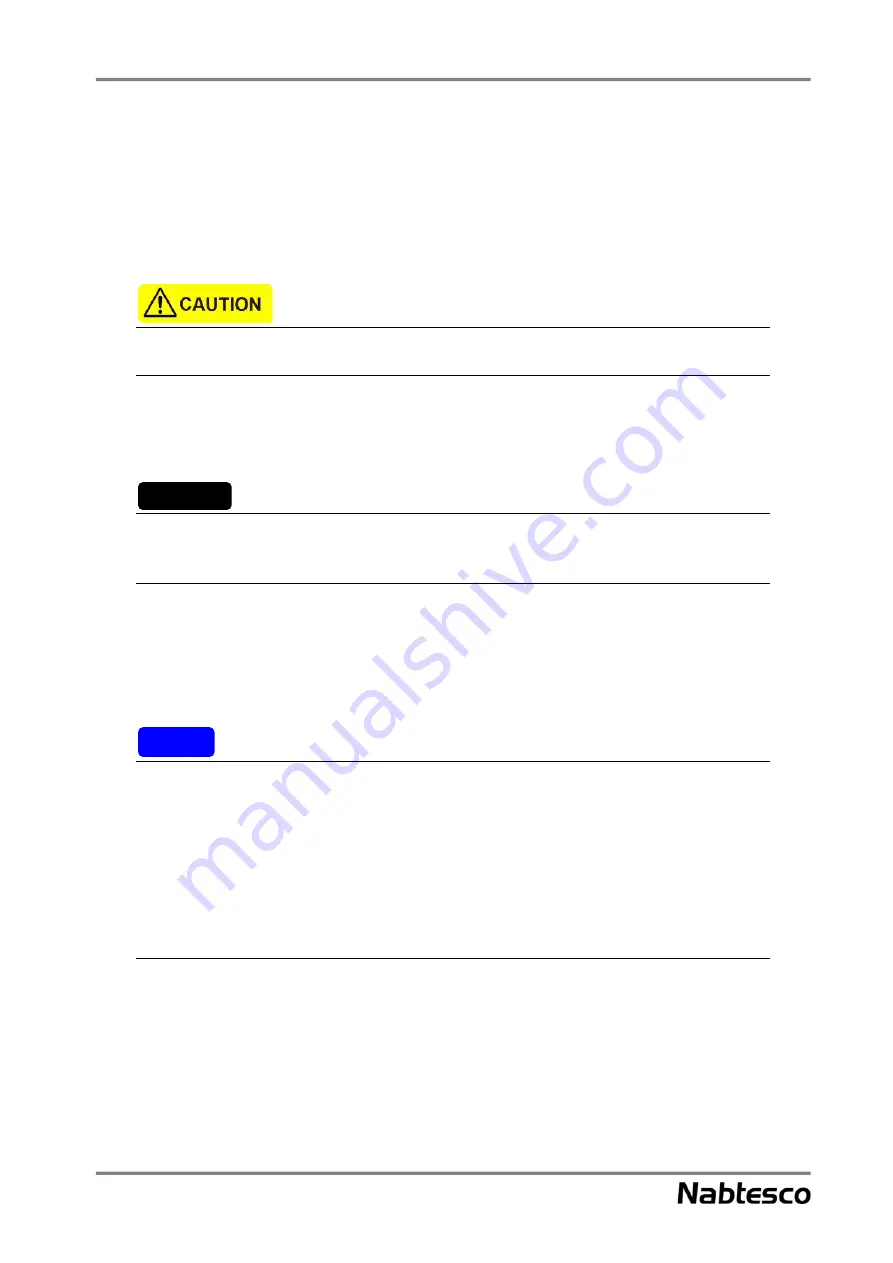
Chapter 6 Filling the Lubricant
37
6.3. Lubricant filling procedure
This section describes how to fill the lubricant.
Perform steps 1 to 7 by taking care regarding the following precautions.
• When handling the lubricant, be sure to wear protective goggles and rubber gloves.
If the lubricant gets in your eyes or touches your skin, it could cause inflammation.
Step 1
Remove both of the plugs for injecting/draining grease, and attach a grease nipple, etc., and then
attach the injector.
If the filler is attached with the supply side down, air is less likely to accumulate in the reduction gear,
which facilitates the lubricant filling procedure.
Step 2
Fill the specified lubricant using the filler.
• When filling the lubricant, be sure to remove the plug for injecting/draining grease on the drain side.
• When pneumatic pressure is used for filling the lubricant, set the pressure below 0.03 MPa.
If you fail to remove the plug for injecting/draining grease on the drain side, the internal pressure
increases. As a result, the oil seal could fall off or the oil seal lip could be reversed.
If the internal pressure of the reduction gear increases, an oil seal could fall off or lubricant could
leak.
The shape of the reduction gear may differ from the illustration in Fig. 6-3 above, depending on the
ordered specifications. For details on the shape, refer to the catalog and the separately provided
“External dimensions” drawings and specification sheet.
Step 3
If the lubricant overflows from the tapped hole for injecting/draining grease on the drain side during
filling, temporarily stop the filling.
Step 4
Remove the filler from the grease nipple and plug the tapped hole for injecting/draining grease on
both the greasing and drain sides.
Important
Note