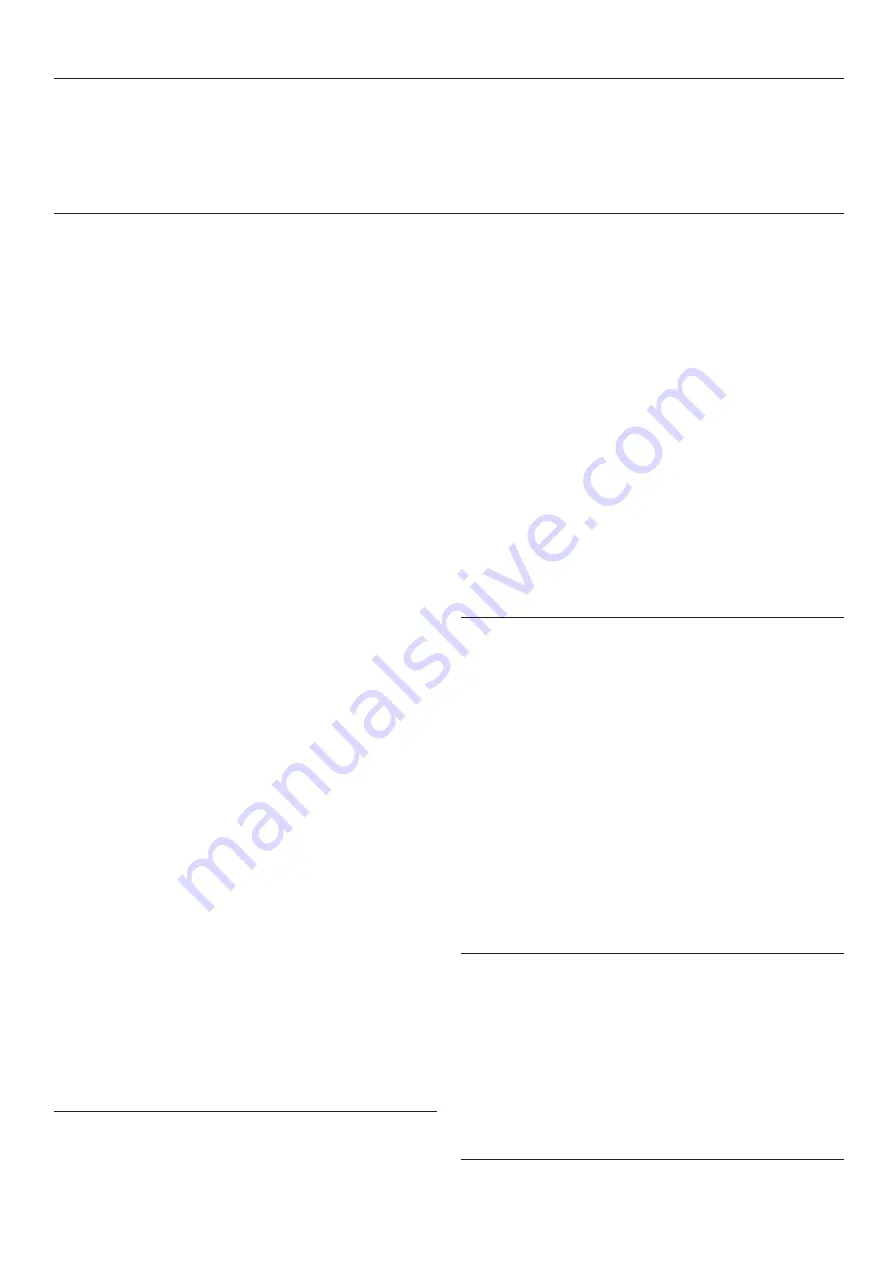
26
17. TROUBLEShOOTING AND FREQUENTLy ASKED QUESTIONS
If the performance of your shower deteriorates in service please follow the self help
items detailed below before seeking professional advice from the installer.
If the actions below fail to restore the shower performance you should initially contact
the person or company that installed the shower.
Q. Water does not flow when
start / stop button is pressed.
A.
Seven things to check:
- Check the mains circuit breaker and/or
fuse.
- Check the isolation pull cord or surface
mounted switch is on.
- Check the mains water supply is fully
open at the stop cock.
- Check that the local isolating valve is
fully open.
- Check the inlet filter on the shower is not
blocked (see page 25).
- If the “o – t” digits flash in the display the
unit is in over temperature mode, if the
water ceases to flow then the unit has
automatically shut down.
PURGING INSTRUCTIONS: It is
important to stand clear of the spray
from the handset as hot water will
initially be emitted.
• On the shower unit press and hold the
warmer (+) and cooler (-) buttons for a
minimum of 3 seconds until COLD water
flows into the shower and through to the
shower handset.
• When the water is free flowing and all
the air has purged through the system
press the start / stop button and this will
stop the water flow.
Q. Water too hOT.
A.
Five possible reasons:
- Select a cooler temperature by pressing
the cooler (-) button.
- Clean the shower handset of any dirt or
debris.
- Check that the mains water stop valve is
fully on.
- Check the inlet filter on the shower (see
page 25)
- Check that the local isolating valve is
fully open.
Q. Water too COLD.
A.
Five things to check:
- Select a warmer temperature by
pressing the warmer (+) button.
- Confirm that there is sufficient water
pressure and flow available.
- Check to see if the “o – t” digits are
showing in the display (see page 24).
- If there is still no hot water contact MX
Customer Care.
Q. Power setting reduces
automatically.
A.
This is part of the shower units
thermostatic control operation and is
a safety feature to reduce the risk of
scalding. This is most likely caused by low
water flow. See ‘Water too HOT’.