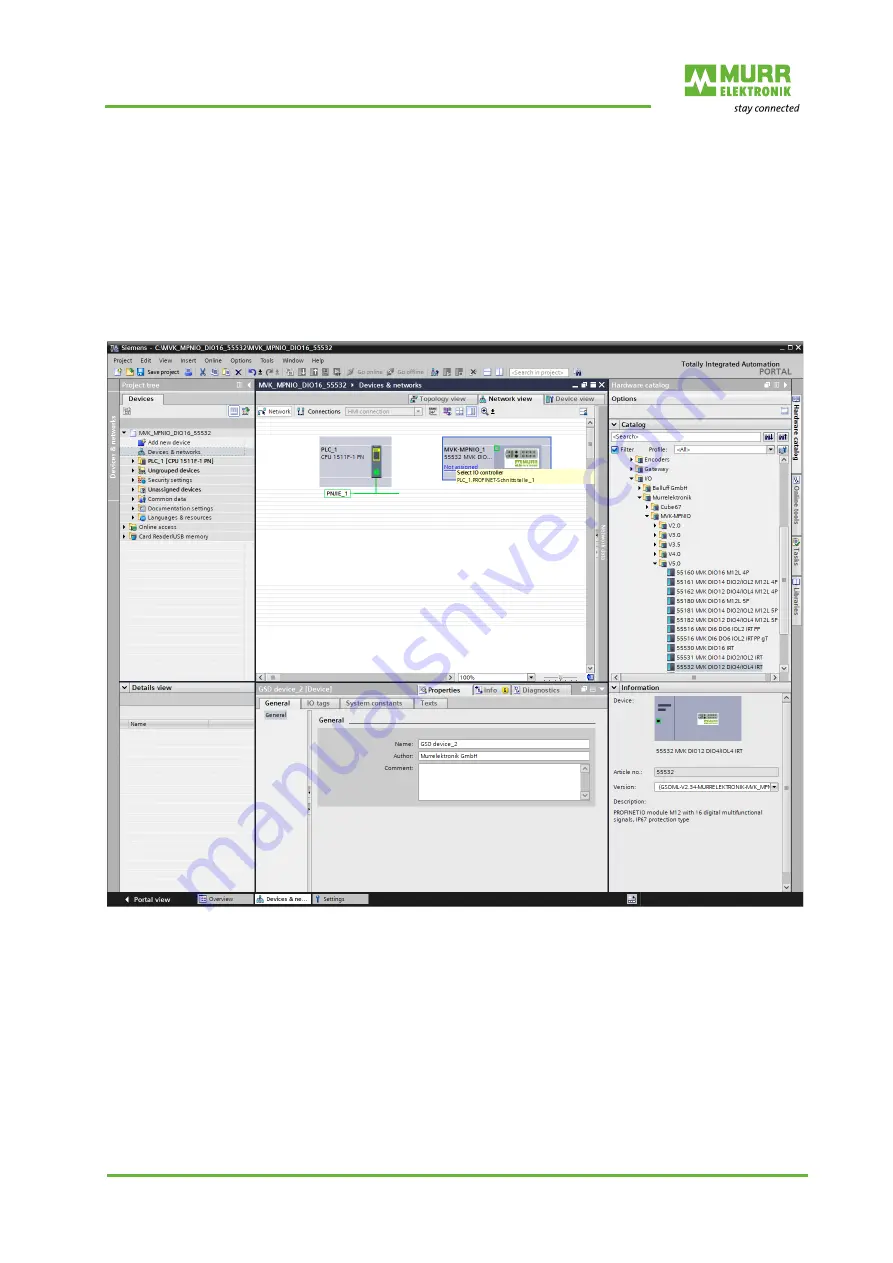
Start-up
User manual 55530_hdb_en_16
55 / 156
The
MVK-MPNIO
must be marked in the
TIA Portal
in the folder structure of
the hardware catalog under
Other field devices | PROFINET IO | IO | Murrelektronik |
MVK-MPNIO
|
V5.0
In the hardware catalog, mark the
MVK-MPNIO
module.
Drag and drop the entry to an empty area in the "Devices & networks" win-
dow.
Assign the module to a
new IO controller
Fig. 7-2: Assign the module to a new IO controller
On the module symbol, click
Not assigned
.
Select
PLC_1.PROFINET-Schnittstelle_1
. The module is assigned to an
IO controller.
For further configuration, double-click the module to select it.