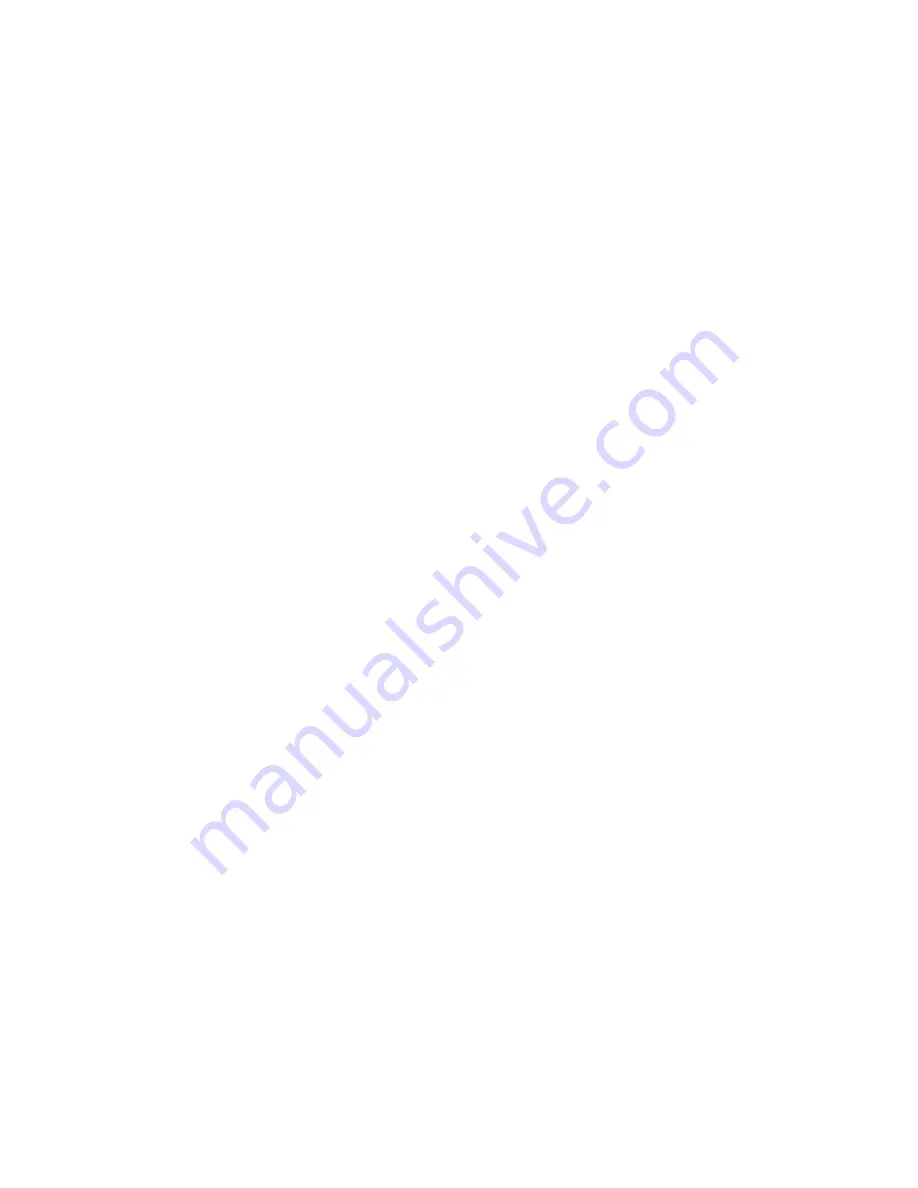
952.5-0000010 OM
3
CONTENT
1 TRACTOR DESCRIPTION AND OPERATION
..................................................................11
1.1 Tractor assignment
...............................................................................................................11
1.2 Technical specifications
.......................................................................................................12
1.3 Tractor composition
..............................................................................................................15
1.4 Vibration level at the operator's working place of the tractor “BELARUS-952.5”
.....................18
1.5 Noise level at the operator's working place of the tractor “BELARUS-952.5”
..................18
1.6 Tractor and its component marking
...................................................................................18
2 CONTROLS AND INSTRUMENTS
......................................................................................20
2.1 Layout of controls and instruments of the tractor
............................................................20
2.2 Switches of instrument board
.............................................................................................21
2.3 Upper shield unit of button switches and rear wiper switch
...........................................23
2.4 Cab heater and fan control
..................................................................................................24
2.5 Conditioner control
...............................................................................................................25
2.5.1 Conditioner control in conditioning mode
......................................................................25
2.5.2 Conditioner control in a heating mode
...........................................................................25
2.5.3 Cab ventilation
...................................................................................................................26
2.6 Instrument board
...................................................................................................................27
2.7 Pilot lamps unit
......................................................................................................................28
2.7.1 General information
..........................................................................................................28
2.7.2 Functioning algorithm of pilot lamp to indicate operation of heating plugs
....................29
2.8 Integrated indicator
...............................................................................................................30
2.8.1 General information
..........................................................................................................30
2.8.2 Assignment and operation principle of integrated indicator gauges
.........................30
2.8.3 Pilot lamps of the integrated indicator
............................................................................33
2.8.4 Description of testing the indicator performance
..........................................................34
2.8.5 Programming panel of integrated indicator
...................................................................34
2.9 Engine control panel
.............................................................................................................36
2.9.1 General information
..........................................................................................................36
2.9.2 Information display
............................................................................................................36
2.9.2.1 General information
.......................................................................................................36
2.9.2.2 Adjustment of brightness and sharpness of the information display
.....................37
2.9.2.3 Call up of changeable images and parameters on the screen of the information
display
...........................................................................................................................................37
2.10 Steering
................................................................................................................................40
2.10.1 General information
........................................................................................................40
2.10.2 Steering wheel adjustments
..........................................................................................40
2.11 Parking brake control
.........................................................................................................40
2.12 Handle for fuel feed manual control
................................................................................40
2.13 Tractor pedals
.....................................................................................................................41
2.14 Gear shifting
........................................................................................................................41
2.14.1 General information
........................................................................................................41
2.14.2 Gears shifting in the transmission with a double-lever GB control and speed-
increase gear unit
........................................................................................................................41
2.14.3 Gear shifting in transmission with a single-lever GB control and speed-increase
gear unit
........................................................................................................................................42
2.14.4 Gears shifting in transmission with double-lever GB control and reverse gear unit
........................................................................................................................................................44
2.14.5 Gears shifting in the transmission with a single-lever GB control and reverse gear
unit
.................................................................................................................................................45
2.15 Control panel for rear axle DL and rear PTO.
.......................................................................47