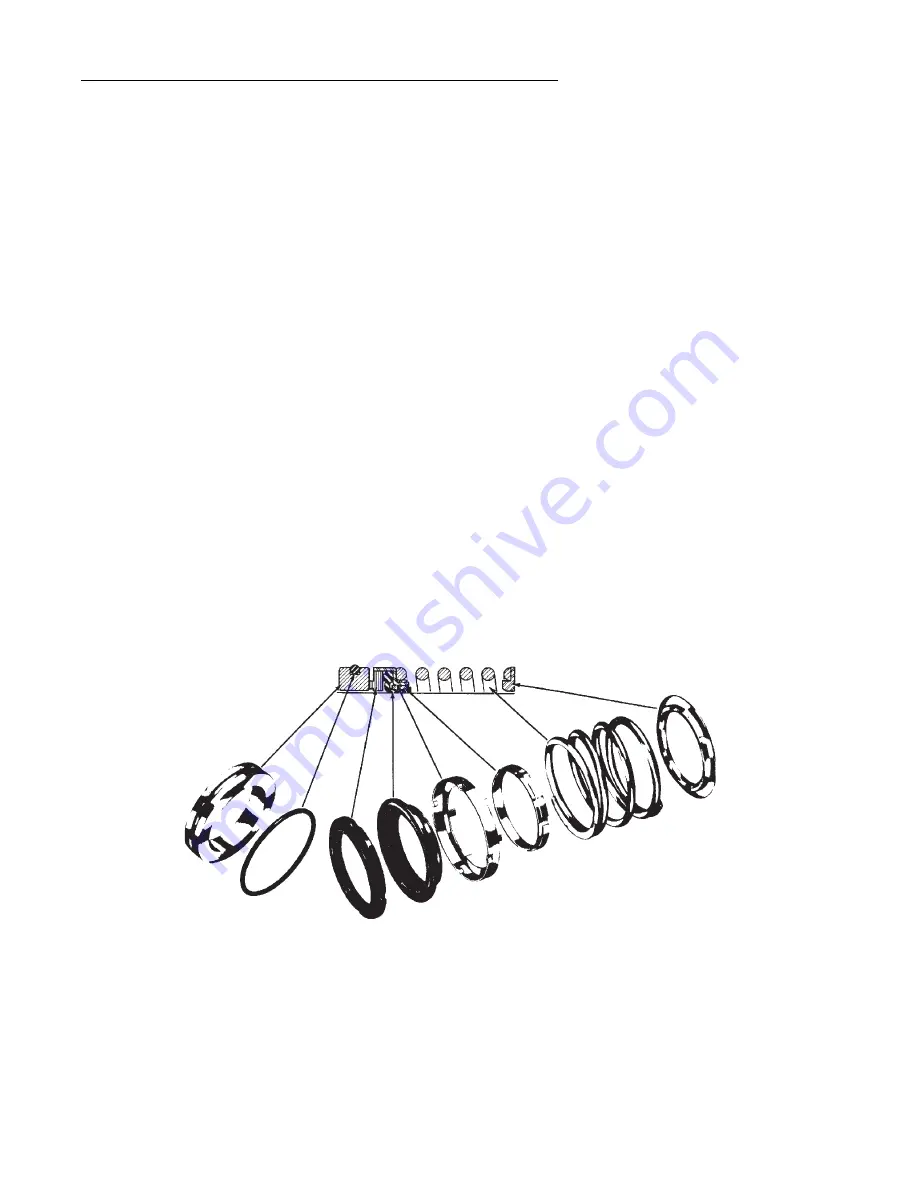
Page 508
P31 SERIES
4.
Maintenance
CLOSE COUPLED PUMPS
A.
Seals
B.
Flushing Lines
C.
Lubrication
4A Seals
Mechanical seals are used in MTH
Pumps to eliminate the maintenance
that is normally associated with pack-
ing boxes. This does not, however,
mean they can totally be ignored.
Check a new installation for seal
leakage.
Maintenance of seals consists
primarily of periodic observation,
looking for the first signs of failure.
An occasional drip that continues to
worsen is an indication that the seal
has failed and must be replaced.
Follow the appropriate Disassem-
bly/Assembly instructions. Always
shut down a pump with failed seals
as soon as possible. Leaky seals
are usually followed by motor bear-
ing failures and then possible pump
damage as rotating parts become
mis-aligned.
Where seal failures or minor fluid
leaks are not tolerable, consideration
should be given to switching to a
sealless leak-free design. Most MTH
pumps are available in a sealless
canned motor design. See the SP31.
4B Flushing Lines
External Flushing lines are not
an option on P31 pumps with
mechanical seals. There is an
external line available on the canned
motor SP31.
Figure 4-1
Seat
“O” Ring
Primary Ring or
Rotating Element
Flexible
Elastomer
Diaphragm
Retainer
Drive Ring
Spring
Spring
Holder
4C Lubrication
Sealed ball bearings are standard
in all MTH pumps and motors. The
maximum continuous operating
temperature for bearings is 375°F.
While it is not advisable to routinely
disassemble sealed bearings, it
is possible to removes the seals
during disassembly and determine
their condition. Use new bearings
for reassembly. While the pump is
in service, listen for unusual sounds
or changes in bearing noise. A
screwdriver held between the bearing
housing and your ear while the pump
is rotated by hand is sometimes
helpful if there is too much ambient
noise when the system is operating.