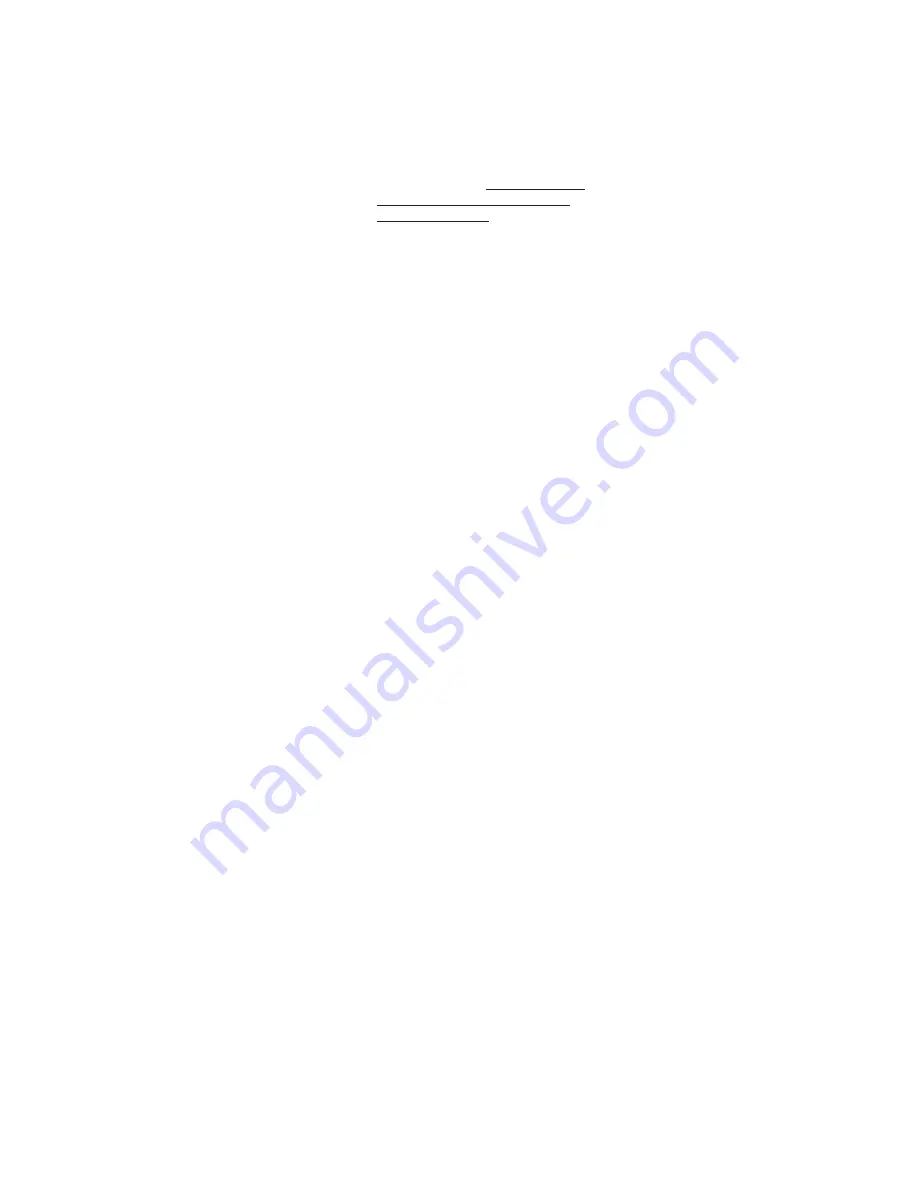
Page 511
9. Apply a thin coating of lubricant
to the o-ring groove in the casing
(#108). Place the casing (#108)
over the motor bracket with the
inlet and outlet ports in the 12
o’clock position. Install the four (4)
M6-1 bolts (#33). DO NOT torque
the bolts at this time as impeller
damage will result. Lightly snug
the bolts systematically, alternat-
ing diagonally across the casing
until the o-ring is seated and the
casing is snug against the impel-
ler. The pump should not turn by
hand at this time because the
casing is physically squeezing the
impeller against the motor bracket.
This condition is termed the “Zero
Clearance Position” and will be
important to setting the final per
-
formance adjustment in the next
step.
NOTE: If the position of the adjusting
nut was previously locked down or is
otherwise unchanged from the time
of disassembly and does not require
any adjustment, please proceed to
step 10f to complete reassembly.
10. Adjusting pump clearance and
setting performance.
a. Turn the adjusting nut (#110)
counter-clockwise and tighten
it firmly against the back of the
casing (#108) to set the zero
clearance position of the cas-
ing.
NOTE: Some early versions of the
adjusting nut (#110) have 60
notches while the current model
has 266. If you have a 60 notch
adjusting nut, divide the notch
adjustment references by five in
the following procedure.
b. Make a reference mark on
the casing next to one of the
notches on the adjusting nut.
This is the zero clearance start-
ing point.
c. Back off the four (4) M6-1 Bolts
(#33) a few turns.
d. Refer to the curve in Figure
5-2 to find the approximate
adjustment setting for your
application’s performance
needs.
b. Make sure that both the motor-
face and the feet of the motor
bracket are clean. Slide the
motor bracket over the shaft
onto the motor, making sure the
water stop is at the 12 o’clock
position.
c. Screw the motor bracket (#84)
to the motor using the motor
thru bolts (#19) in the back side
of the motor.
3. Install the rotating element (#12).
Lightly lubricate I.D. of the rotat-
ing element elastomer. Place
the clean rotating element on the
shaft sleeve with the carbon end
towards the seat. Place the spring
over the shaft, with the backing
plate up, and compress the spring
to locate the rotating element
against the seat. If this fails to
seat the rotating element gently
push the rotating element down
with a thin blade screwdriver being
careful not to damage the seat or
the rotating element.
4. Compress and hold the seal
spring slightly below the snap ring
groove and install the snap ring
(#4). Make sure the snap ring is
locked firmly into the groove.
5. Install the impeller key (#23) into
the shaft sleeve keyway.
6. Install the impeller (#11). The
impeller is a slip fit and should
slide on firmly but easily until it
stops against the impeller wear-
ing surface. Force should not
be required or used to install the
impeller in the correct position.
The impeller hub should be facing
out away from the motor bracket.
Refer to Figure 5-1.
7. If the adjusting nut (#110) was
moved or removed during disas-
sembly, install it now on the motor
bracket (#84) by threading it on
until it bottoms out on the motor
bracket.
8. Apply a thin coating of compat-
ible lubricant to the large “O” ring
(#7). Place the o-ring over the
motor bracket and slide it up to the
shoulder where the adjusting nut
is.
e. Start turning the adjusting nut
counter-clockwise the number
of notches indicated in Figure
5-2. The minimum casing clear-
ance is a total of .002” or 10
notches, (five notches equals
.001”). Note that if you find
the pump is over or under-
performing when returned to
service, you may return to
this procedure and make fine
adjustments to achieve the de-
sired pump output. Generally,
for a given system pressure,
turn the adjusting nut clockwise
if more flow is needed, counter-
clockwise if less flow is needed.
However, do not tighten the nut
below the 10 notch minimum
clearance or the pump will run
the risk of seizing. Refer to Fig-
ure 5-2 and make notes on the
diagram to record your adjust-
ment results.
f. Tighten the bolts systematically,
alternating diagonally across
the cover. DO NOT exceed 7-
11 ft. lbs. of torque or damage
to the pump may occur.
g. Turn the pump by hand. If
the pump turns, proceed to
Section 5E Testing and Final
Adjustment. If the pump will not
turn, loosen bolts and turn the
adjusting nut counter-clockwise
five to ten more notches as
described in steps 10 b through
f above. If the pump still fails to
turn by hand, remove the cas-
ing and impeller and inspect for
burrs or foreign material. Reas-
semble and readjust, beginning
with step 5.
5E Testing and Final Adjustment
The pump is now ready for installa-
tion. Final adjustments will be made
with the pump in operation.
1. Connect all piping and fill the
pump with fluid.
2. Reconnect the electrical connec-
tions, referring to the colored or
numbered tape used to mark the
wires during disassembly.
3. Make sure all valves are opened,
and fluid will flow through the
system.