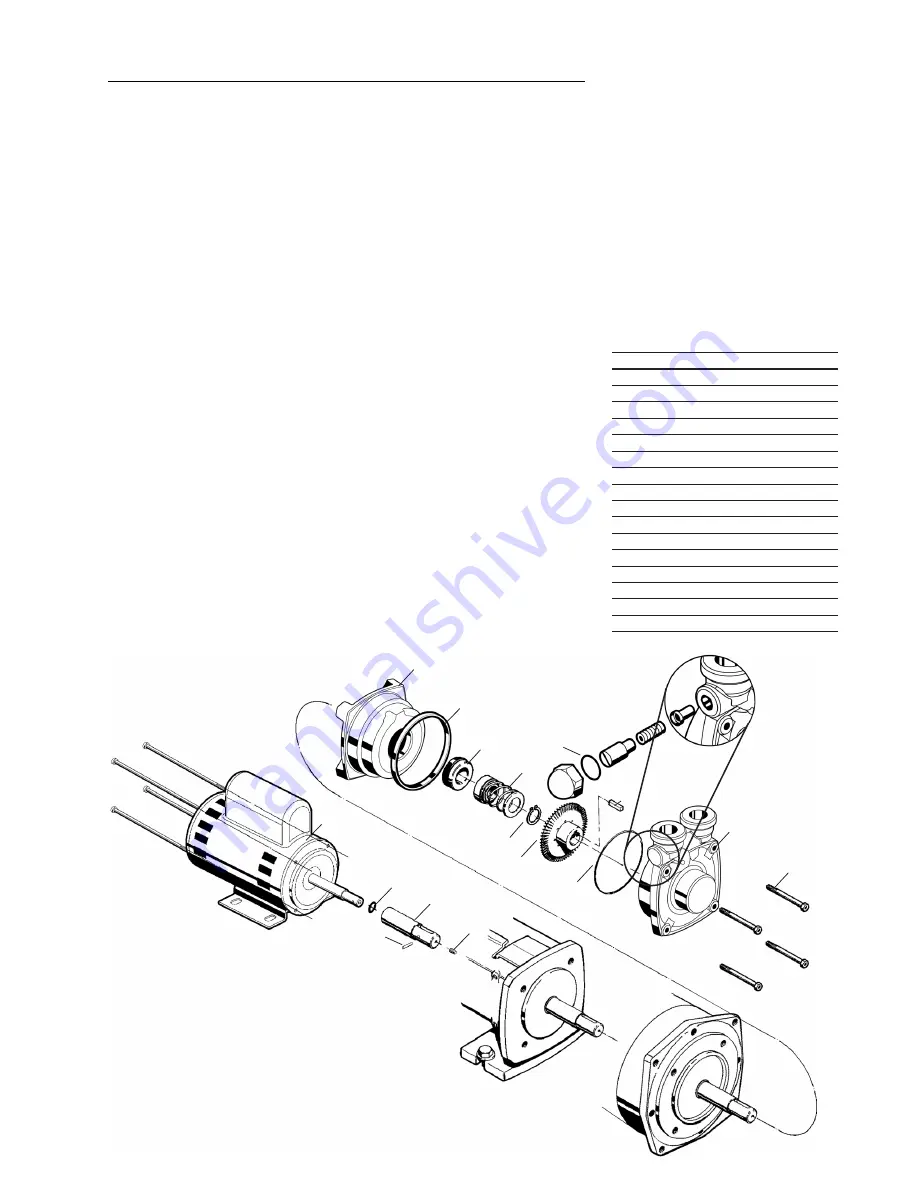
P31 PUMP ENDS
A. Preliminary
B. Disassembly
C. Inspection of Components
D. Reassembly
E. Testing and Final Adjustments
5A Preliminary
Before attempting any service on the
pump or motor, disconnect the elec-
trical power to the pump motor. If the
pump and motor are to be removed
as a unit, note the wiring configura
-
tion. Use colored or numbered tape
to mark the wire connections of the
motor and power source, for recon-
nection. If the pump is being used to
pump hot liquid, let the pump and liq-
uid cool before starting disassembly.
1. Disconnect the inlet and outlet pip-
ing before unbolting the pump and
motor. If the pipes are corroded,
use penetrating oil on the threads
to aid in removal.
2. Unbolt the motor from the base
and remove the unit. All work on
the unit should be performed on
an elevated workbench whenever
possible.
5B Disassembly
The following tools and equipment
are needed for disassembly/reas-
sembly of P31 Series Pumps:
1. Soft plastic or wooden mallet.
2. Small Punch.
3. 5mm hex wrench.
4. 3/16” hex wrench.
5. Snap ring pliers.
6. Penetrating oil.
7. 11/16” wood dowel (Approx. 6”
long.)
8. Thin blade screwdriver.
9. Cealube G, P-80, or glycol base
lubricant compatible with the pro-
cess fluid and O-ring elastomers.
(DO NOT use petroleum prod-
ucts.)
To disassemble the pump:
Refer to Figure 5-1 for reference to
the numbered parts in the procedures
below. Please note that the P31 is
an adjustable performance pump. It
has been preset at the factory for
your particular performance needs.
If you are disassembling for inspec-
tion or seal replacement only, you
may wish to mark or otherwise lock
the adjusting nut (#110) into place
(before disassembly) especially if you
are uncomfortable with the readjust-
ment procedures found in Section 5D
Step 10.
1. Remove all liquid from the pump.
Air blown through the pump will
remove fluid quickly.
2. Remove the four (4) M6-1 X
60mm bolts (#33) from the casing
(#108).
Page 509
Figure 5-1
125
84
12
4
11
23
7
108
33
8
88
19
72
NAME/DESCRIPTION
PART NO. QTY.
Motor Bracket
84
1
Casing
108
1
Adjusting Nut
110
1
“O” Ring/Casing
7
1
“O” Ring/ Relief Valve
7A
1
“O” Ring/Shaft Sleeve
8
1
Snap Ring
4
1
Impeller
11
1
Seal Rotating Element
12
1
Seal Stationary Seat
125
1
Setscrew
15
1
Thru Bolt/Casing
33
4
Thru Bolt/Motor
19
4
Shaft Sleeve
88
1
Shaft Sleeve Pin
72
1
Key/Impeller Drive
23
1
P31 CLOSE-COUPLED PUMP
110
P31 SERIES
5.
Service
15
7A