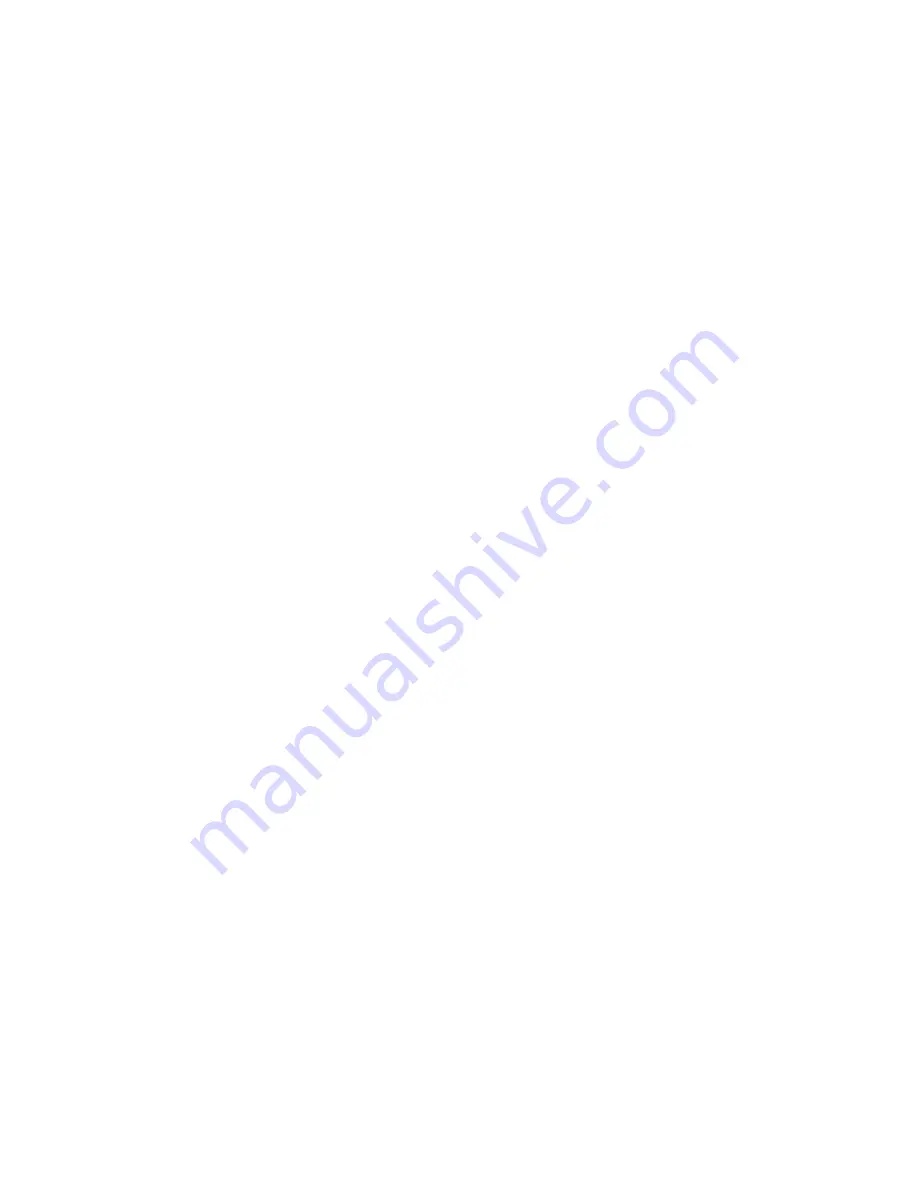
Page 512
4. Start the pump and make any
final adjustments to the adjusting
nut and the M6 bolts holding the
casing on. These bolts must be
torqued to about 7-11 ft. lbs. to
obtain proper performance.
5. Check for leaks on pump
and piping. Special attention
should be given to the seal area
where the motor shaft enters the
motor bracket.
6. Under pressure, the impeller will
find its “hydraulic” balance.
7. Using an amprobe or similar de-
vice, check for motor overload.
8. While the impeller is seating, it
is common to experience some
variance in Amp readings. After a
run-in period the readings should
level off.
This completes the adjustment and
testing phase. The pump is ready for
service.