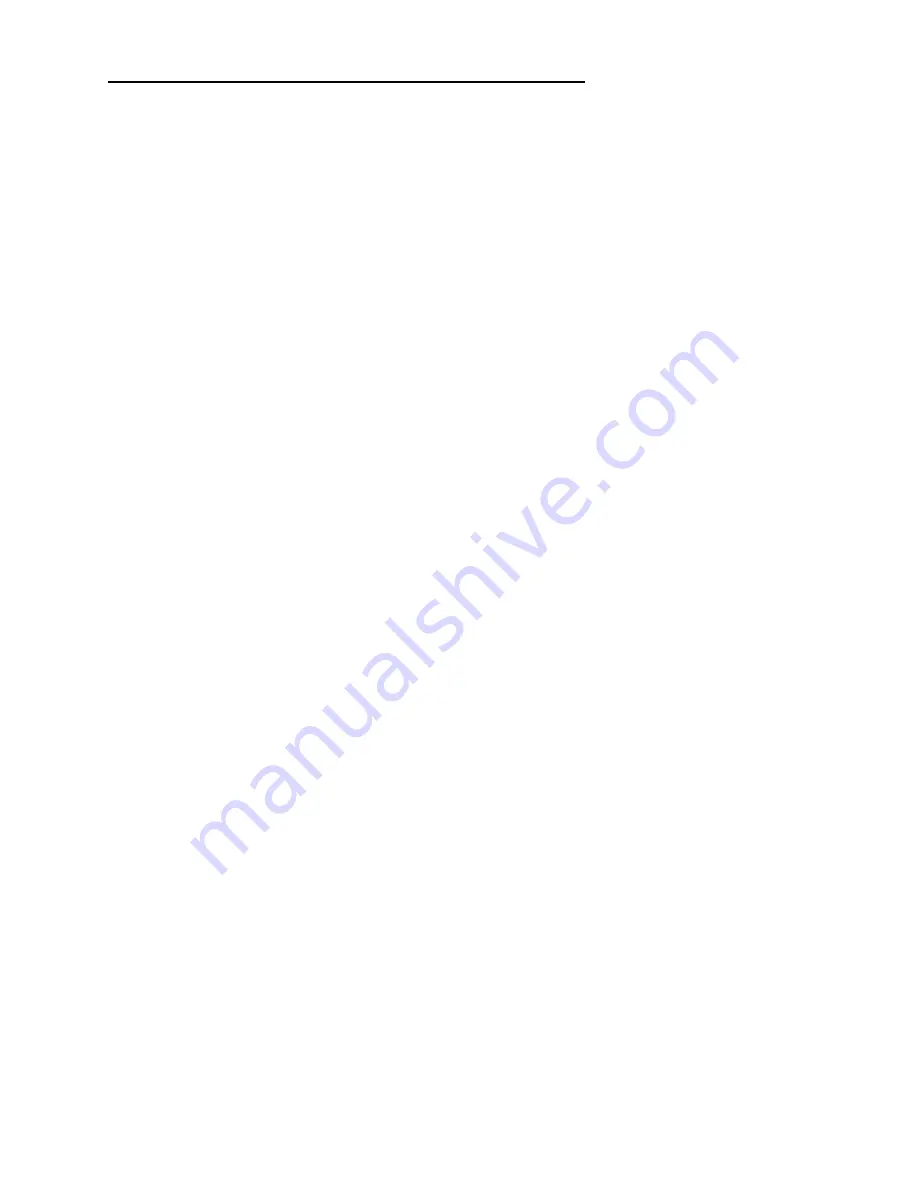
CLOSE COUPLED PUMPS
A. Location
B. Foundation
C. Piping
In order to insure that pumping equip-
ment is installed properly and to
obtain reliable pump operation, it is
recommended that only experienced,
qualified erecting engineers under
-
take this task. Read the instructions
thoroughly before beginning.
2A Location
The first consideration for locating
a pump is elevation. The lowest
possible elevation using the shortest
possible suction piping is usually the
best. Questions regarding possible
locations should be resolved by mak-
ing inlet head calculations including
all friction losses. The one producing
the highest inlet pressure should be
selected. One reason for this pre-
caution is that, the greater the inlet
pressure, the less likelihood of NPSH
problems. Also a flooded suction is
particularly helpful on start-up when
the seals or the entire pump can
be ruined because it is not properly
primed and purged of air.
A dry, easily accessible location is
also important. Allow ample clear-
ance around the unit for free air
circulation. If a dry location is not
available, the pump can be mounted
on a foundation, above the floor.
Specify motor enclosure, pump ma-
terials, or coatings to suit the worst
conditions expected. Place the pump
so that it can be easily inspected and
serviced during operation. Sufficient
head room should be provided, par-
ticularly when lifting devices will be
used for heavier assemblies.
2B Foundation
Baseplates alone are not rigid
enough to maintain alignment of
flexible-coupled units. The pump
foundation is used as a support for
the baseplate to maintain alignment
of the unit. If the baseplate is to be
grouted to the foundation, it is only
necessary to embed the edges. It is
unnecessary to completely fill under
the baseplate. DO NOT grout the
unit to the foundation until it has been
properly aligned.
The foundation must be a perma-
nent rigid installation of concrete or
other material of sufficient mass to
absorb all normal vibrations. Locate
the foundation bolts using a layout
or template in relation to the suction
and discharge piping. If concrete is
being used, foundation bolts of the
specified size can be enclosed in a
pipe sleeve two to three diameters
larger than the bolts to compensate
for minor variations in alignment.
Close-coupled pumps can be mount-
ed on a steel base prior to installation
or mounted directly to the foundation.
Place shims under one or more of the
motor feet so that strain and distor-
tion will not result when the mounting
bolts are tightened.
2C Piping
2C1 Piping Alignment
It is important that all piping be lined
up and not forced into place. Pumps
are precision pieces of equipment
and are subject to damage or re-
duced performance if heavy forces
are applied to the casing from mis-
aligned piping. It is recommended
that you begin piping at the pump.
If the lines are ended at the pump,
particularly if the last piece is cut a
little too short or long, the pump will
be forced to meet the pipe and strain
or distortion will result.
2C2 Piping Support
Never allow the pump to support
piping. Other means such as pipe
hangers and pipe supports should
be used to carry piping to avoid
misalignment and distortion. Consid-
eration should be
given to thermally induced expansion
and contraction, particularly in long
runs of straight pipe.
2C3 Piping Size
In general, inlet and outlet pipe sizes
should be equal to or
larger than those of the pump.
This should not, however, be the
determining factor. Many things
including installation and operating
costs are involved in the decision.
Careful use of the pipe and fitting
friction loss tables as shown in the
Hydraulic Institute manual along with
the appropriate pump performance
curve should be the basis for judge-
ments.
Page 505
P31 SERIES
2.
Installation