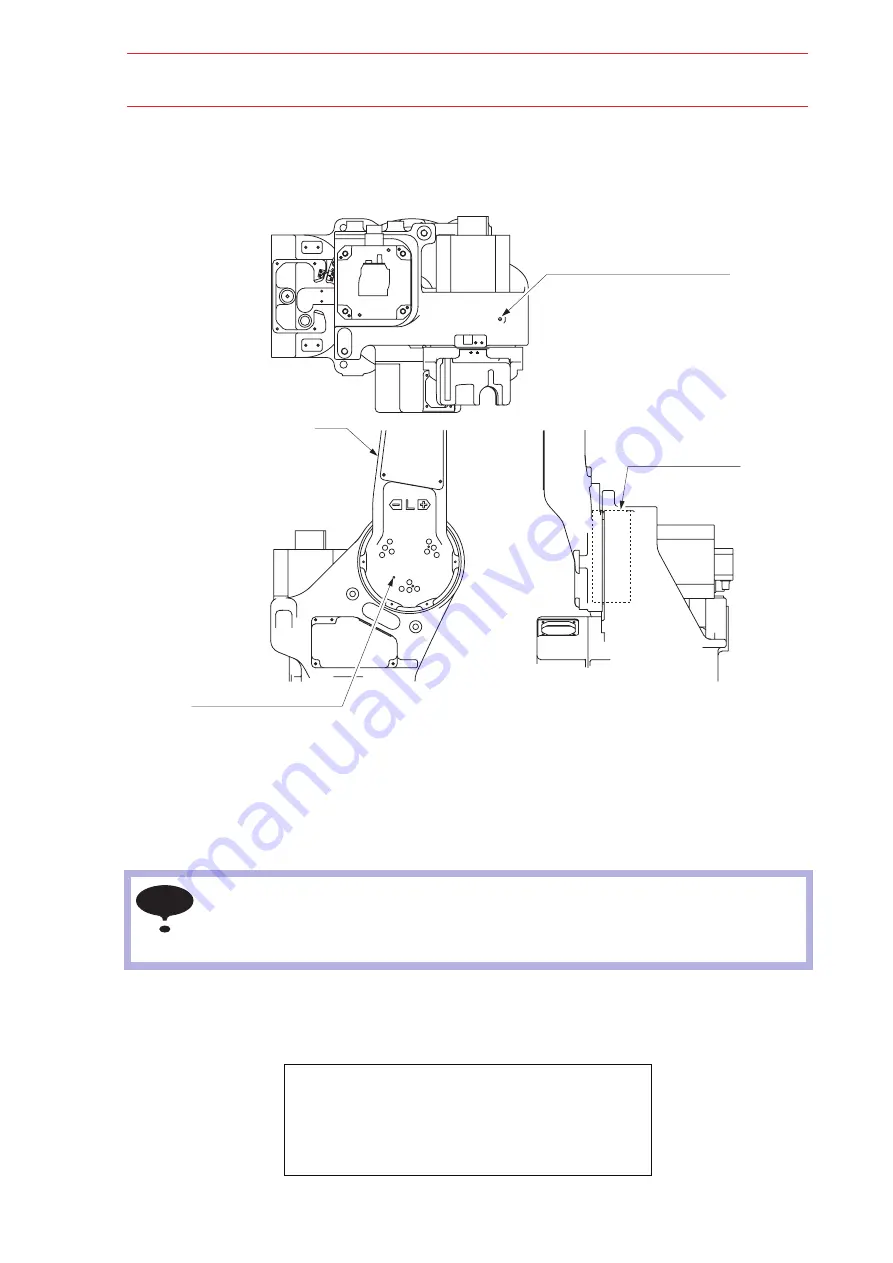
9.3 Notes on Grease Replenishment/Exchange Procedures
9-9
HW0484074
HW0484074
9.3.2
Grease Replenishment/Exchange for L-axis Speed
Reducer
Fig. 23 L-axis Speed Reducer
T
Grease Replenishment (Refer to "Fig. 23 L-axis Speed Reducer")
1. Posture the L-arm vertical to the ground.
2. Remove the hexagon socket head plug PT1/8 from the grease exhaust port.
3. Remove the hexagon socket head cap screw M6 from the grease inlet and install the
grease zerk A-MT6 x 1. (The grease zerk is delivered with the manipulator.)
4. Inject grease from the grease inlet using a grease gun.
• If grease is injected with the plug on, the grease will go inside the motor and may cause a
damage. Make sure to remove the plug before the grease injection.
• Do not install a joint, a hose, etc. to the grease exhaust port. Failure to observe this
instruction may result in damage to the motor due to coming off of an oil seal.
Grease type: VIGO Grease RE No. 0
Amount of grease: 150 cc
(300 cc for 1st supply)
Air supply pressure of grease pump: 0.3 MPa or less
Grease injection rate: 8 g/s or less
Grease exhaust port
(Hexagon socket head plug PT1/8)
L-arm
Grease inlet
(Hexagon socket head cap screw M6)
L-axis speed reducer
NOTE
47/59