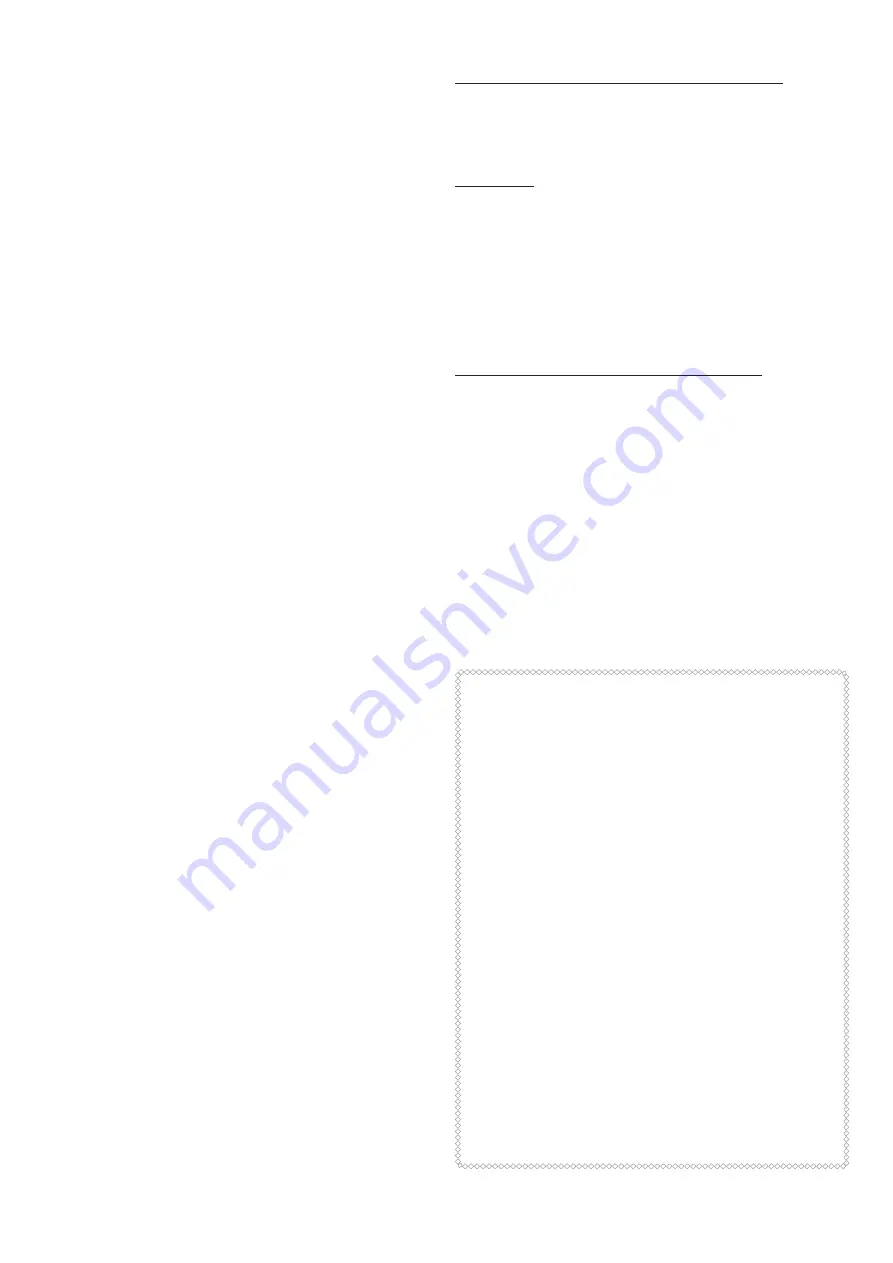
9
FOR THE ENGINEER - STARTING UP THE
APPLIANCE AND FINAL CHECKS
Start the appliance by following the directions given in section “Usage” page 7, checking
that the appliance is working correctly. Pay special attention to the colour of the flames
ensuring there is no yellow- ness which would indicate burner venturis blocked by
insect matter.
Check the gas operating pressures with the heater under full power at the inlet pres-
sure nipple located on the right hand side of the gas body valve stem.
Check the burner pressure with the heater at full load at the test nipple located on
the left hand side of the main gas valve body be- low the main burner. These pressures
must at least be equal those specified in this manual in order to achieve the desired
performance specified in this manual.
These gas water heaters are set in the factory for use with the gas they are intended
to burn. The gas for which each appliance is set is indicated on the packaging and on
the data plate of the heater itself
Check the flue for spillage: close all the doors and windows in the room containing
the water heater. If there are any fans or extractors in the room then these must be
turned on full. Light any other open flued appliances such as fires of gas hobs. Turn the
water heater on by opening a hot tap on full burn and run for 5 minutes to allow the
flue to warm up.
Hold a smoke match to the side of the opening of the draught diver- tor using an
extended holder, making sure that the end of the match is located centrally in the
draught divertor.
The smoke should be pulled up the flue and not back into the room. If spillage is de-
tected, run the appliance for a further 10 minutes and then repeat the test. If spillage
is still detected then check the flue for blockages, check that the correct flue terminal
is fitted and that the correct ventilation is fitted at a low and high level. Also check the
ventilation has not been blocked.
LOOKING AFTER THE APPLIANCE
• PRECAUTIONS
– Against furring up (lime scale)
If the appliance is installed in an area with very hard water, with time, the following
may occur:
– A fall in the hot water temperature, or
– A reduction in the hot water flow.
This means that the heat exchanger may be furred up, creating the above situations
Note: De-furring/descaling should be carried out using proprietary agent or dilute
hydrochloric acid. It is recommended to circulate the descaling fluid around the heat
exchanger in order to speed up the process.
• MINIMUM ANNUAL MAINTENANCE
Gas water heaters are rugged pieces of equipment which are designed to work for
a long time with minimum maintenance requirements. The only regular maintenance
required is the (annual) cleaning of the heating body and the burner. If the appliance
is installed in a caravan it is advised that this is done at the beginning of each season.
• CLEANING THE MAIN BURNER
To carry out the annual cleaning of the burner, proceed as follows:
– Turn off the gas supply, remove the cover and remove the burner.
– Clean the surface of the burner heads gently with a brush and vacuum cleaner. Then
blow through them to remove any particles of dust loosened du- ring the brushing
operation.
– Check the venturis in the main burner for contamination from insects and spiders
webs.
• CLEANING THE HEAT EXCHANGER
To carry out the annual cleaning of the heating body, proceed as follows:
– Turn off the gas supply
– Turn off the supply of water to the appliance by turning off the appliance water
supply.
– Turn on all the hot water taps to empty all the pipes.
– Remove the heating body and clean it by gently brushing the fins. Soot, if found,
should be removed by washing, and the cause of the sooting investigated.
• CLEANING THE PILOT
If the pilot light flame is yellow and the safety valve takes a long time to open, this
means that either the pilot injector or pilot burner is partially blocked.
The pilot injector may be blocked with contaminants carried within the gas, whilst the
pilot burner is more likely to be contaminated by insects (spiders / egg sacs)
N.B. No attempt should be made to clear blocked or partially blocked pilot injectors
by using wire. If blowing through the injector or immersing in solvent fails to clear the
restriction, then a new injector should be fitted.
When the pilot is working normally the flame should be a stable blue coloured cone
shape. To clean the pilot burner, proceed as follows:
– Turn off the gas supply, remove the front cover. Remove the pilot injector, by sla-
ckening the supply pipe nut first, and unscrewing the pilot injector from the pilot
burner
– Remove the contamination from within the pilot burner using a pipe cleaner, and
blow through to remove any further debris.
– Replace the pilot injector, ensuring that the washers are properly fitted.
WINTERISATION
Winterisation of Holiday Homes That Have a Water Heater
Fresh water freezes at 0°C and expands by 9% with a significant force that will
destroy:
• Pipe work
• Water heater components
• Taps, and shower valves
DRAIN DOWN
If you leave fresh water in your caravan system over the winter you will run the
risk of damage. This can only be avoided by removing the fresh water from the
system – we call this a “drain down”. You may wish to drain down the fresh water
system yourself using the procedure in the next section but we STRONGLY RE-
COMMEND that you have this carried out by an experienced engineer as many
caravan systems can only be completely drained by blowing the water out and this
requires specialist equipment. View the charge for a drain down as a mini insuran-
ce policy and always ask the engineer if he has the equipment to blow the water
out. The two most common parts to be damaged by frost on a water heater are
the water control assembly and heat exchanger and the shower valve can also be
damaged by frost and the costs to replace these can be expensive, see our website
for water heater spare prices.
Drain Down Procedure – without specialist equipment
• Turn off the fresh water supply stop cock outside the Holiday Home
• Disconnect the fresh water feed outside the home if possible as this protects
from flooding due to stop cock failure
• Open all hot and cold taps and shower valves and place the shower head in the tray
• Use the Holiday Home Owner’s Handbook to locate all the fresh water drain
cocks under the van – some of these may not be obvious
• Open these drain cocks
This procedure does not guarantee that all the fresh water will leave the system.
Most modern homes have double check valves in the TMV2 shower mixers and
these trap fresh water and stop the flow of water around the system once the
drain cocks and taps are open. It may appear that all the water has left the system,
but beware! This pitfall can be avoided by removing the shower mixer valve/valves
from the system after the cold water supply has been switched off and the drain
cocks opened. Many manufacturers provide access panels and these may make the
removal of shower mixers easier. Removal of some shower mixers requires the
use of special tools. In addition, pipe work layouts can cause air locks leaving water
inside vulnerable components such as the water heater or shower mixer.
Re-commissioning the home is a reverse of the above procedure.
This drain down procedure may work but the only way to be sure is to blow the
water out using compressed air at 3 bar maximum pressure.
WARRANTY
The water heater is guaranteed against manufacturing defects for one year
from first commissioning date. However the guarantee is subject to proof of
commissioning in accordance with the gas safety (Installation and Use) act of
1998. The guarantee does not cover defects caused by lack of maintenance.
Morco Products Ltd. warranty will cover parts and labour if the appliance has
been fitted as part of the original equipment in a caravan holiday home or
leisure accommodation vehicle.
Appliances distributed as non original equipment either directly from Morco
Products Ltd. or other merchants are subject to a return to base policy for
repair and return.
As an alternative to returning the appliance for repair we will supply spare
parts and advice for defective appliances on the provision
that we can talk to the competent registered gas safe engineer involved in
the fitting or repair of the defective appliance. Under this approach, no com-
pensation will be offered for labour involved in the removal and refitting of
the appliance or for any work / travelling involved in the fitting of spare parts.
Exclusions from warranty
- Damage caused by frost
- Scaling up of the heat exchanger
- Blocked pilot injectors
- Insect or debris in the burner or heat exchanger
- Blocked gas or water filters
- Incorrect operation caused by damaged mixer taps or shower TMV2
- Incorrect installation of the appliance or flue
- Low water pressure
Please note that proof of commissioning for the purposes of this
warranty is a copy of the commissioning certificate
as filled out by the Gas Safe Engineer or other qualified personnel.