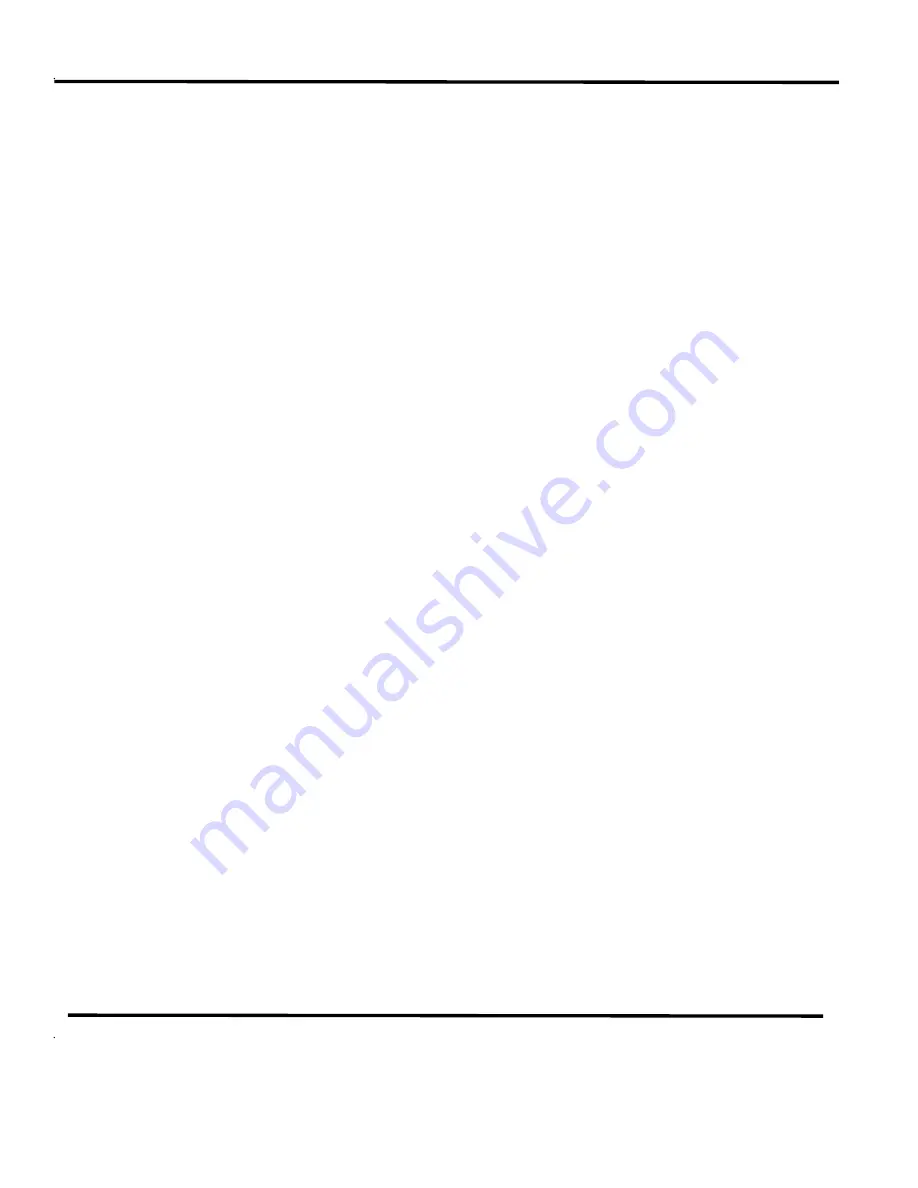
CHAPTER 1: SYSTEM DESCRIPTION
MODEL 250DP DUAL PULSE
RESISTANCE WELDING POWER SUPPLY
1-2
990-280
You can program up to 128 weld schedules and save them in battery backup memory. A built-in schedule
protection feature protects weld schedules from unauthorized or inadvertent changes. Schedule 0 serves as a
scratch-pad which anyone can use to perform occasional jobs without jeopardizing the integrity of the
production line. The exclusive weld fire lockout feature guarantees that weld quality is independent of line
voltage fluctuations and the speed at which the power supply is operated.
Dual pulse
welding, an exclusive and unique feature of Unitek Peco power supplies, improves weld quality
and eliminates weld splash.
Dual pulse
means each weld is performed with two pulses with independent
energy levels. The first pulse displaces the plating or contamination and reforms the surface so that it is in
intimate contact with the electrode. The second pulse welds the base metals. You can also use the
automatic step feature to step to a new schedule, after a preset number of welds, in order to compensate for
electrode wear.
The optional built-in Unitek Peco Weld Sentry adds a weld monitoring capability to the 250DP which
improves process control by detecting subtle changes in voltage, current, and power. The remote schedule
feature allows the 250DP to reliably select weld schedules in automated applications.
The 250DP can be used with manual, user actuated, or air actuated weld heads. It is a multi-voltage unit
designed for operation at 100, 115, 208, or 230 VAC, 50/60 Hz.
Features
x
Multi-function microprocessor control provides repeatable process control and is compatible with air or
manually actuated weld heads. Facilitates multiple applications at a single work-station and protects
weld schedules from changes by unauthorized personnel.
x
Dual pulse welding eliminates weld splash. Improves weld quality, especially when welding plated
materials.
x
Three weld functions available:
– Basic
– Rollspot
(seam
weld)
– Sequence
Repeat.
x
User-friendly programming serves as a built-in manual, quickly guiding you through the most complex
programs. Menu-driven utilities make it easy to copy schedules and calibrate the power supply.
x
Two air valve drivers are provided to sequentially control two separate air operated weld heads. Air
Valve Driver 1 controls a 24 VAC or 115 VAC air actuated weld head. Air Valve Driver 2 is
programmed by Output Relay 1 (refer to the next-listed feature).
x
You can use two relays to provide status signals to external devices. You can also use Relay 1 to
program Air Valve Driver 2 to control a second 24 VAC air actuated weld head.