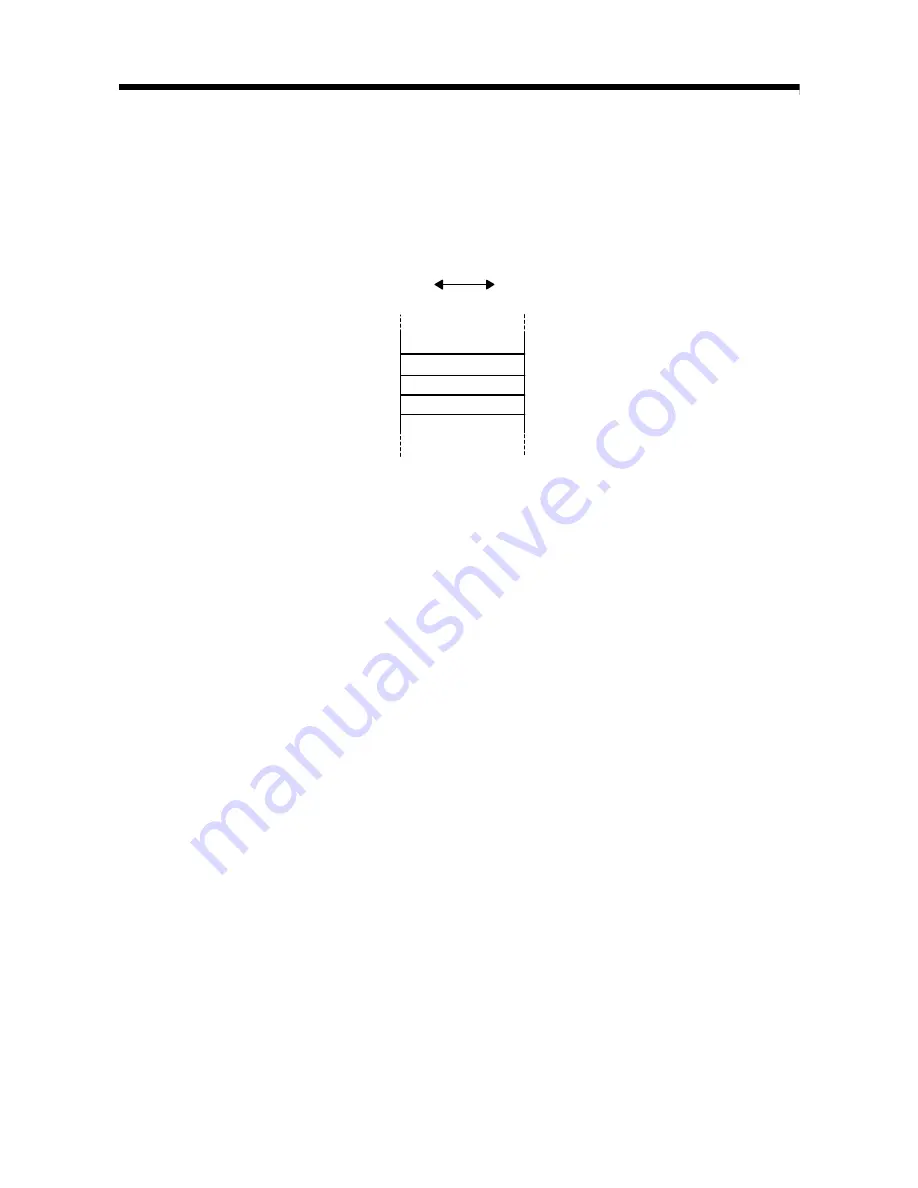
5 - 18
5 - 18
5. THINGS YOU NEED TO KNOW BEFORE PROGRAMMING
4. The number of accumulated writes is 100,000.
When the Manage Number of Writes command is executed with addition
specified and five as the number of writes [specified using command options
(Un
\
G5, Un
\
G4005)] in this state, for example, the error details storage area
(Un
\
G41, Un
\
G4041) status flag (bit 4) turns ON, and error detection (X5, XD)
turns ON.
Bit 0 (Lower)
(Upper) Bit 7
Address
0013
H
0012
H
0011
H
0010
H
000F
H
0
1
A
0
8
6