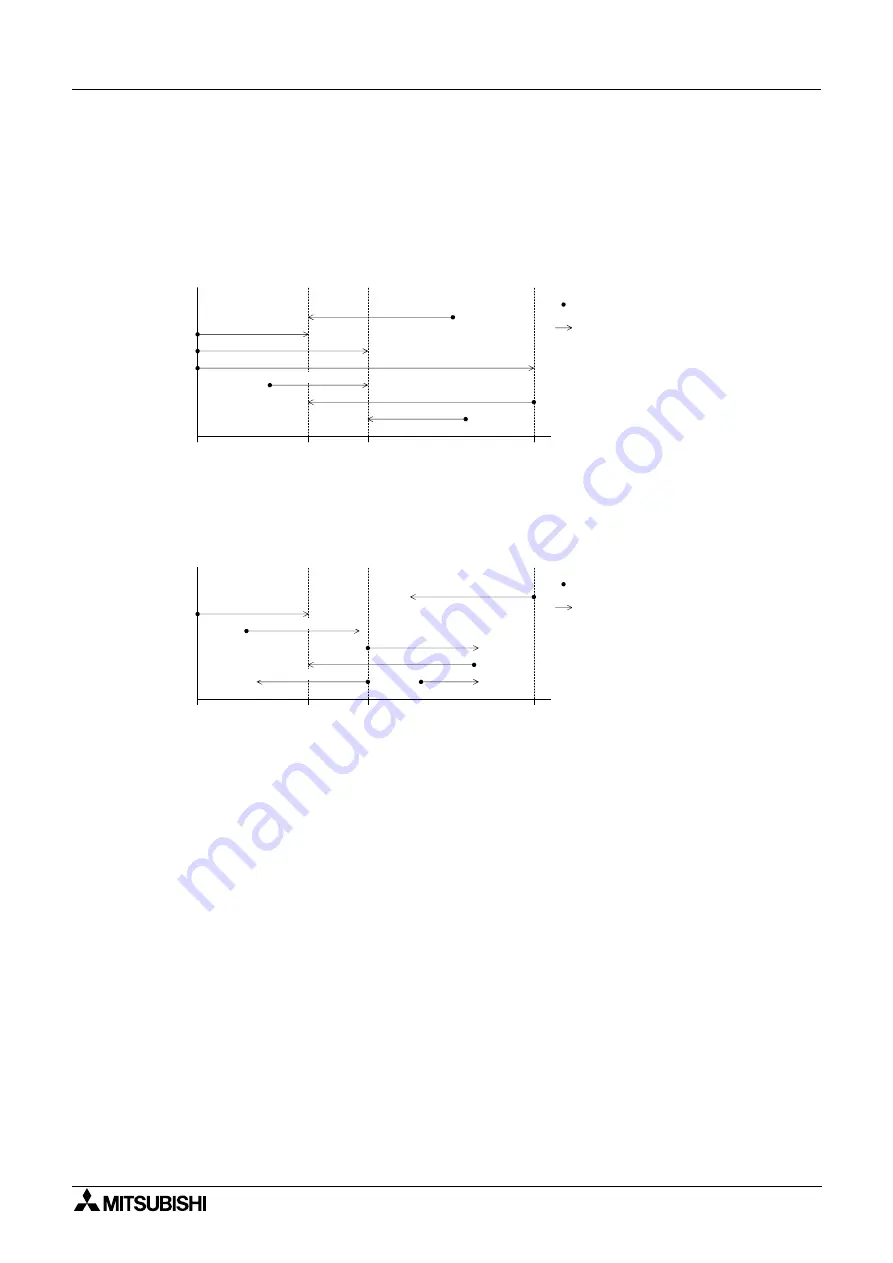
Positioning Control
Components of Positioning Control and Their Roles 3
3-11
3.3.2
Setting the target position
In positioning control, the target position can be set by the following two methods.
(Available command units are "mm", "inch", "degree" or "pulse".)
1) Absolute method
In this method, a point (absolute address) is specified for positioning while the zero point is
regarded as the reference. The start point is arbitrary.
2) Incremental method
In this method, positioning is performed through specification of the movement direction
and the movement quantity while the current stop position is regarded as the start point.
Address
100
Address 150
Address 100
Address 150
Address 150
Address 100
Address 300
300
Point C
150
Point B
100
Point A
0
Zero point
Start point
End point
Movement quantity -100
300
Point C
150
Point B
100
Point A
0
Zero point
Movement qu50
Movement quantity -150
Movement qu100
Movement qu100
Movement quantity
+100
Movement quantity
-100
Start point
End point
Summary of Contents for MELSEC-F
Page 1: ...Positioning Control Training Manual ...
Page 4: ...Positioning Control ii ...
Page 6: ...Positioning Control iv ...
Page 8: ...Positioning Control vi ...
Page 10: ...Positioning Control Contents viii ...
Page 12: ......
Page 20: ......
Page 26: ......
Page 38: ...Positioning Control Components of Positioning Control and Their Roles 3 3 12 ...
Page 40: ......
Page 46: ...Positioning Control Advanced Positioning 4 4 6 ...
Page 48: ......
Page 58: ......
Page 68: ......