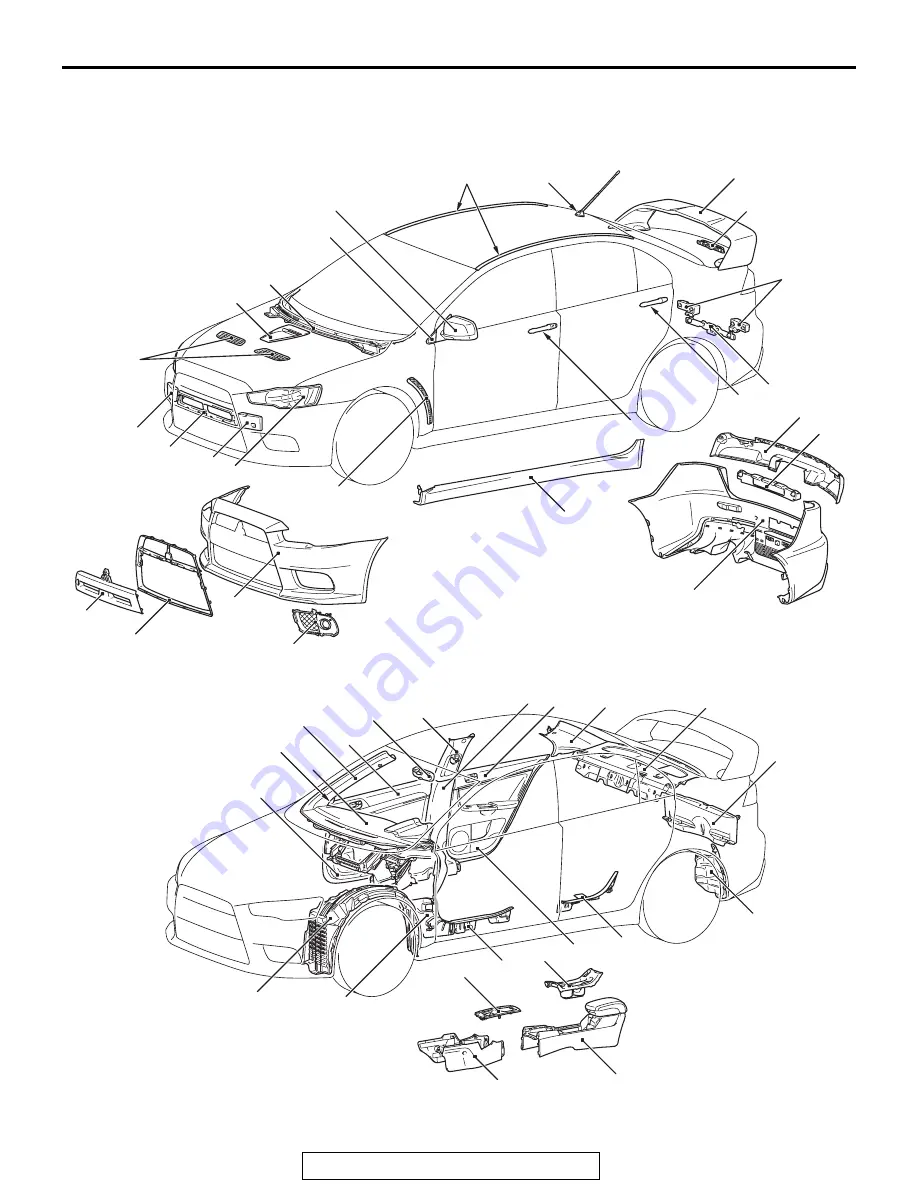
LOCATION OF SYNTHETIC-RESIN PARTS
TSB Revision
SYNTHETIC-RESIN PARTS
5-2
LOCATION OF SYNTHETIC-RESIN PARTS
M4050001001433
The location and material of each of the principal
synthetic-resin parts are shown below.
AB700997AB
29
33
6
11
28
1
13
10
4, 9
5
30
35
17
31
16
32
18
15
14
7
8
2
3
15
40
48
AB700998AB
42
23
24
12
36
37
19
34
26
25
27
21
20
22
38
43
39
41
46
44
45
47
Summary of Contents for Lancer Evolution 2008
Page 31: ...THEFT PROTECTION TSB Revision BODY CONSTRUCTION 1 29 LOCATIONS AC710510 D A B F E D AC E F C ...
Page 37: ...BODY DIMENSIONS AND MEASUREMENT METHODS TSB Revision BODY DIMENSIONS 2 3 NOTES ...
Page 41: ...TYPE A PROJECTED DIMENSIONS TSB Revision BODY DIMENSIONS 2 7 NOTES ...
Page 60: ...NOTES ...
Page 113: ...FENDER SHIELD TSB Revision WELDED PANEL REPLACEMENT 3 5 AB700994 J E C F B AB B G C H D ...
Page 166: ...NOTES ...
Page 177: ...5 1 GROUP 5 SYNTHETIC RESIN PARTS CONTENTS LOCATION OF SYNTHETIC RESIN PARTS 5 2 ...
Page 186: ...NOTES ...