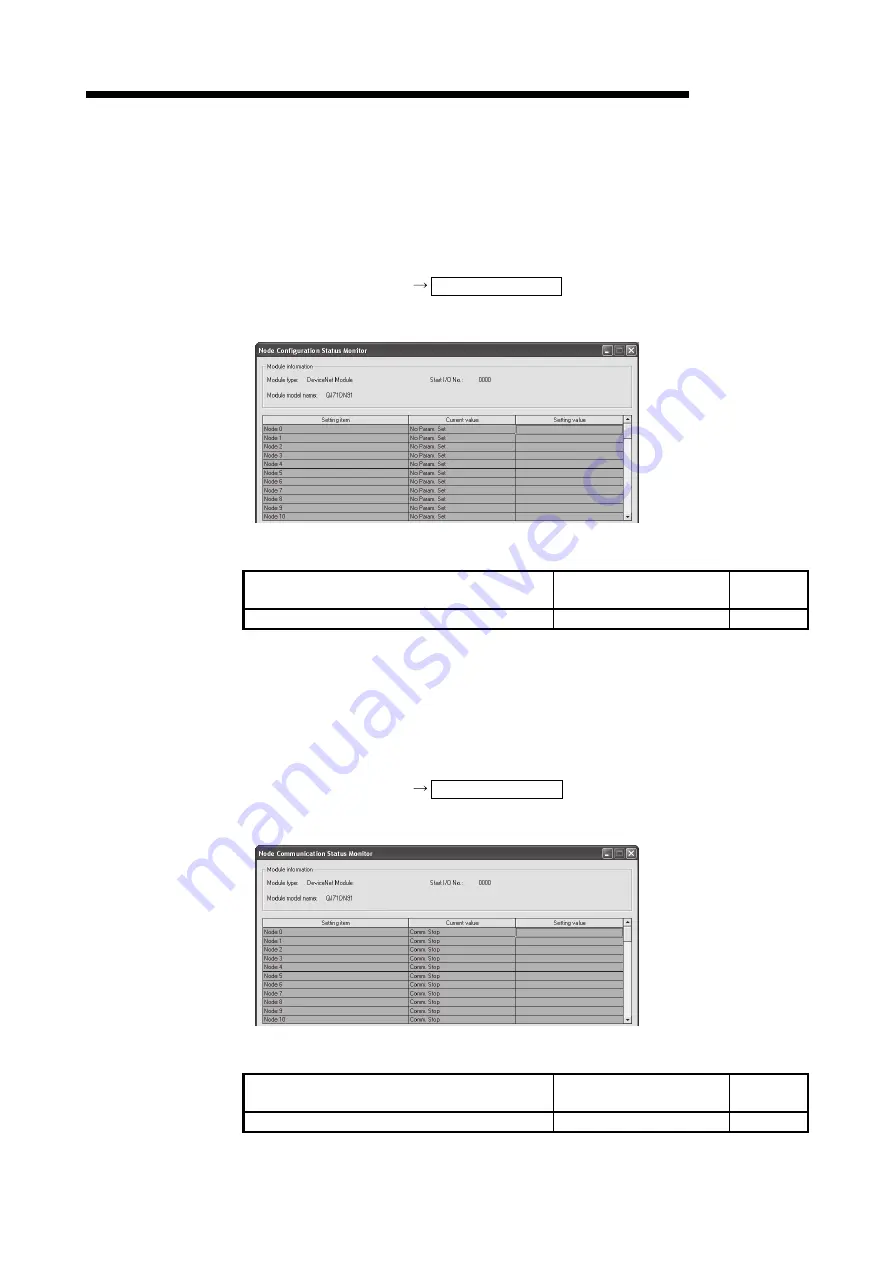
6 - 22 6 - 22
MELSEC-Q
6 UTILITY PACKAGE (GX Configurator-DN)
6.5.4 Node configuration status monitor
[Purpose]
Monitor the parameter setting status of each slave node.
[Operating procedure]
Monitor/Test screen Config. Status Mon.
[Setting screen]
[Setting items]
Item
Buffer memory address (Hex.)
Reference
section
Node 0 to Node 63
01B4
H
to 01B7
H
3.4.4
(1)
6.5.5 Node communication status monitor
[Purpose]
Monitor the I/O communication status of each slave node.
[Operating procedure]
Monitor/Test screen Comm. Status Mon.
[Setting screen]
[Setting items]
Item
Buffer memory address (Hex.)
Reference
section
Node 0 to Node 63
01BC
H
to 01BF
H
3.4.4
(2)
Summary of Contents for QJ71DN91
Page 1: ...DeviceNet Master Slave Module User s Manual QJ71DN91 GX Configurator DN SW1D5C QDNU E ...
Page 2: ......
Page 233: ......