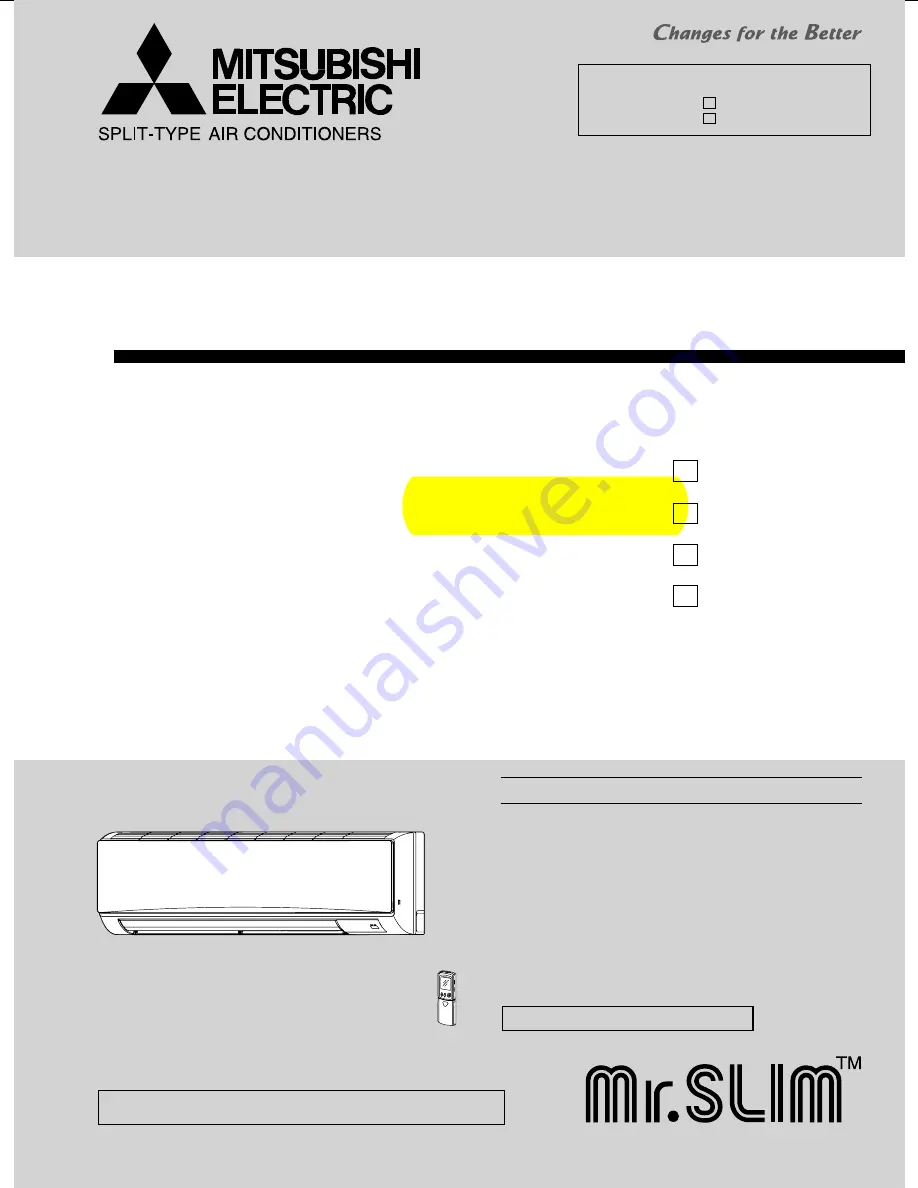
SERVICE MANUAL
CONTENTS
1. TECHNICAL CHANGES
·······································
3
2. PART NAMES AND FUNCTIONS ····················· 4
3. SPECIFICATION ················································ 5
4. OUTLINES AND DIMENSIONS ························ 7
5. WIRING DIAGRAM ············································ 8
6. REFRIGERANT SYSTEM DIAGRAM ··············· 9
7. SERVICE FUNCTIONS ··································· 10
8. MICROPROCESSOR CONTROL ··················· 12
9. TROUBLESHOOTING ····································· 19
10. DISASSEMBLY INSTRUCTIONS ···················· 32
Models
MSZ-D30NA MSZ-D30NA-
8
MSZ-D36NA MSZ-D36NA-
8
MSY-D30NA MSY-D30NA-
8
MSY-D36NA MSY-D36NA-
8
No. OBH501
REVISED EDITION-C
INDOOR UNIT
Outdoor unit service manual
MUZ-D
•
NA Series (OBH502)
MUY-D
•
NA Series (OBH502)
NOTE:
RoHS compliant products have <G> mark on the spec name plate.
PARTS CATALOG (OBB501)
Please void OBH501 REVISED EDITION-B.
Revision C:
• MSZ-D30/D36NA-
8
and
MSY-D30/D36NA-
8
have been added.
DAC-1
Summary of Contents for Mr.Slim MSY-D30NA
Page 41: ...7 MUZ D30NA MUZ D30NA U1 MUZ D36NA MUZ D36NA U1 5 WIRING DIAGRAM ...
Page 42: ...8 MUZ D30NA 1 MUZ D30NA U2 MUZ D36NA 1 MUZ D36NA U2 ...
Page 43: ...9 MUY D30NA MUY D36NA ...
Page 44: ...10 MUY D30NA 1 MUY D36NA 1 ...
Page 139: ...13 MUZ GE09NA MUZ GE12NA 5 WIRING DIAGRAM MUZ GE09NA2 MUZ GE12NA2 OBH549G ...
Page 140: ...14 MUZ GE09NAH MUZ GE12NAH MUZ GE09NAH2 MUZ GE12NAH2 OBH549G ...
Page 141: ...15 MUY GE09NA MUY GE12NA MUY GE09NA2 MUY GE12NA2 OBH549G ...
Page 142: ...16 MUZ GE15NA 1 MUZ GE15NA OBH549G ...
Page 143: ...17 MUZ GE15NAH MUZ GE15NA2 OBH549G ...
Page 144: ...18 MUY GE15NA MUZ GE15NAH2 OBH549G ...
Page 145: ...19 MUY GE15NA 1 MUY GE15NA2 OBH549G ...
Page 146: ...20 MUZ GE18NA MUZ GE18NA 1 OBH549G ...
Page 147: ...21 MUZ GE18NAH MUY GE18NA OBH549G ...
Page 148: ...22 MUY GE18NA 1 OBH549G ...
Page 149: ...23 MUZ GE24NA OBH549G ...
Page 150: ...24 MUY GE24NA OBH549G ...
Page 199: ...73 OBH549G ...