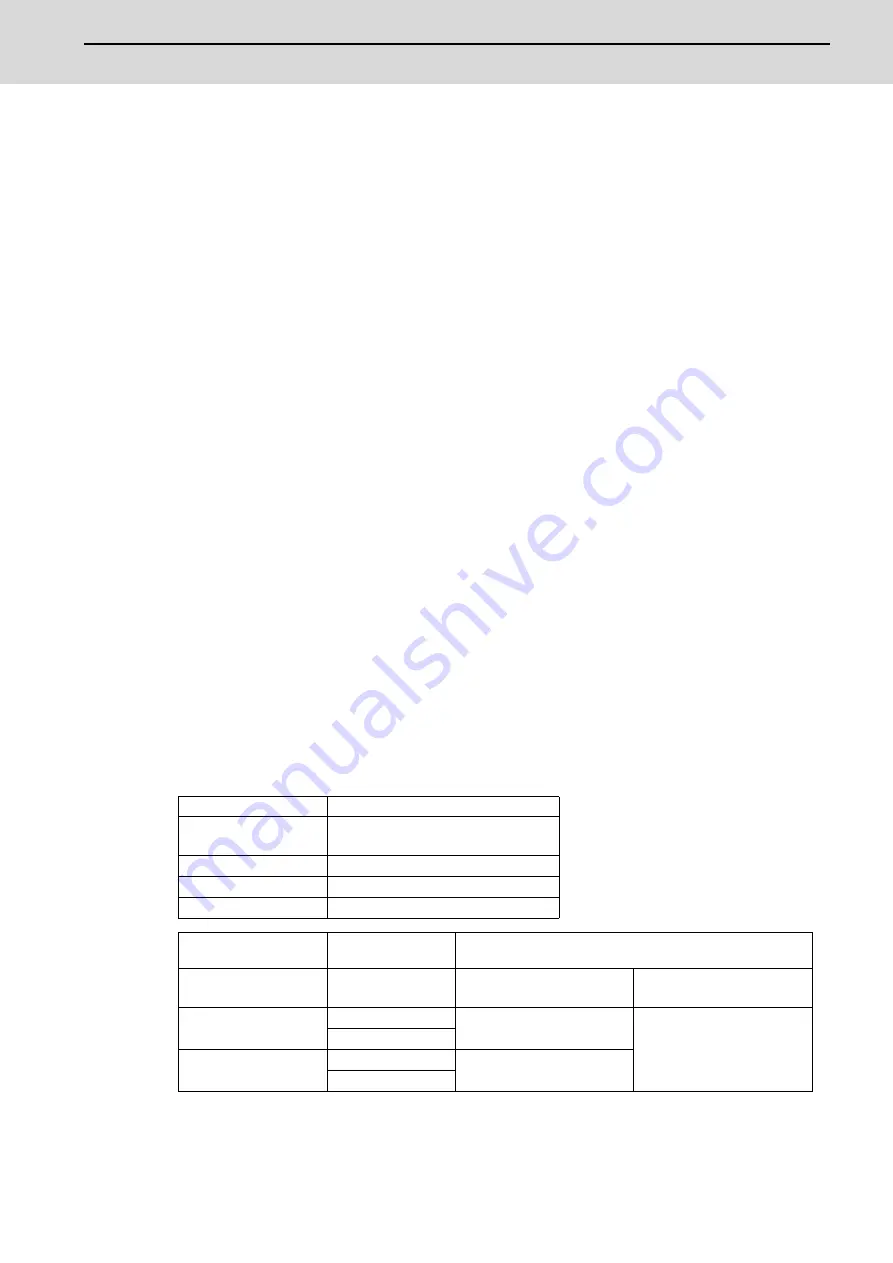
M800W/M80W Series Connection and Setup Manual
32 Setting the Deceleration Check
571
IB-1501268-K
32.6 Precautions
(1) When in-position check is valid, set the servo in-position width of the servo parameter.
(2) This function is invalid for the axes in the automatic machine lock.
(3) When the MSTB is commanded to the next block of the cutting commanded block, the MSTB code is output before
the completion of the cutting command deceleration. Confirm the DEN (motion command completion) signal with
PLC before the execution of the MSTB command which needs to be executed after the completion of the axis
movement.
(4) When the control axis in the synchronous/superimposition control exists in the part system for which in-position
check method has been set, the deceleration completion will be determined when the smoothing for all axes
reaches zero. (Same as the smoothing check method)
(5) When the thread cutting commands are issued consecutively, the deceleration check will not be performed at the
block joint.
(6) When "1" is set for "#1205 G0bdcc" (Acceleration and deceleration before G0 interpolation), the in-position width
will be the value of "#2224 SV024" (In-position detection width). "#2077 G0inps" (G0 in-position width) and ",I
command" programmable in-position check will be invalid.
(7) When the machine is locked and in pre-interpolation acceleration/deceleration, the control axis is always in the in-
position state. (The in-position signal of each axis stays ON.)
(8) During synchronous operation, in-position check method cannot be used.
(9) Deceleration check for opposite direction movement reversal
-
When deceleration check is valid (#1502 G0Ipfg = 1), deceleration check will be executed when the axis
reverses its movement to the opposite direction at the G1 -> G0 successive block regardless of whether G0
non-interpolation is ON or OFF.
-
When deceleration check is valid (#1502 G0Ipfg = 1), deceleration check will be executed when the axis
reverses its movement to the opposite direction at the G1 -> G0 successive block even in the fixed cycle.
-
In the G1 -> G28, G1 -> G29 or G1 -> G30 successive blocks, deceleration check will always be executed
when the G1 movement is completed, when movement to the intermediate point is completed and when
movement to the return point is completed. Note that if the simple zero point return "#1222 aux06/bit7" is valid,
G1 -> G0 deceleration check (#1502) will be followed when the G1 movement is completed and when
movement to the intermediate point is completed. (Deceleration check will always be executed when
movement to the return point is completed even in this case.)
(10) Deceleration check in movement including spindle/C-axis
-
The deceleration check for spindle/C-axis movement command is as described in the table below. That is
because a vibration and so on occurs in the machine when the position loop gain (#13002 PGN) is changed
during the axis movement.
(Note 1) When G1 command is issued, the in-position check is performed regardless of the deceleration
check parameter.
(Note 2) XX expresses all commands.
Parameter
Rapid traverse command
Inpos(#1193)
G0
→
XX
(G0+G9
→
XX)
0
Command deceleration check
1
In-position check
2
Smoothing check
Parameter
Parameter
Other than rapid traverse command
(G1: other than G0 command)
G1SmthChk(#1389)
AUX07/BIT-1
(#1223/BIT-1)
G1
→
G0
(G1+G9
→
XX)
G1
→
G1
0
0
In-position check
(Applicable only to SV024)
No deceleration check
1
1
0
Smoothing check
1
Summary of Contents for M800W Series
Page 1: ......
Page 4: ......
Page 9: ......
Page 21: ......
Page 23: ......
Page 25: ......
Page 27: ......
Page 29: ......
Page 39: ......
Page 40: ...1 IB 1501268 K 1 System Basic Configuration ...
Page 42: ...3 IB 1501268 K 2 General Connection Diagram ...
Page 49: ...M800W M80W Series Connection and Setup Manual 2 General Connection Diagram 10 IB 1501268 K ...
Page 50: ...11 IB 1501268 K 3 List of Configuration ...
Page 60: ...21 IB 1501268 K 4 General Specifications ...
Page 245: ...M800W M80W Series Connection and Setup Manual 4 General Specifications 206 IB 1501268 K ...
Page 246: ...207 IB 1501268 K 5 Installation ...
Page 275: ...M800W M80W Series Connection and Setup Manual 5 Installation 236 IB 1501268 K ...
Page 276: ...237 IB 1501268 K 6 Precautions for Connecting ...
Page 284: ...245 IB 1501268 K 7 Connection of Control Unit ...
Page 315: ...M800W M80W Series Connection and Setup Manual 7 Connection of Control Unit 276 IB 1501268 K ...
Page 316: ...277 IB 1501268 K 8 Connection of Personal Computer Unit ...
Page 322: ...283 IB 1501268 K 9 Connection of Graphic Control Unit ...
Page 328: ...289 IB 1501268 K 10 Connection of Keyboard Unit ...
Page 330: ...291 IB 1501268 K 11 Connection of Operation Panel I O Unit ...
Page 350: ...311 IB 1501268 K 12 Connection of Remote I O Unit ...
Page 386: ...347 IB 1501268 K 13 Connection of Side Memory I F Unit ...
Page 388: ...349 IB 1501268 K 14 Connection of Manual Pulse Generator ...
Page 392: ...353 IB 1501268 K 15 Connection of Synchronous Feed Encoder ...
Page 394: ...355 IB 1501268 K 16 Connection of Machine Operation Panel ...
Page 406: ...367 IB 1501268 K 17 Connection of Handy Terminal ...
Page 408: ...369 IB 1501268 K 18 Cable ...
Page 443: ...M800W M80W Series Connection and Setup Manual 18 Cable 404 IB 1501268 K ...
Page 444: ...405 IB 1501268 K 19 Setup Outline ...
Page 450: ...411 IB 1501268 K 20 Setting the Hardware ...
Page 482: ...443 IB 1501268 K 21 Setting Up with HMI Integrated Installer ...
Page 486: ...447 IB 1501268 K 22 Setting the Parameters and Date Time ...
Page 492: ...453 IB 1501268 K 23 Sequence Program Writing ...
Page 516: ...477 IB 1501268 K 24 Confirming the Basic Operation ...
Page 522: ...483 IB 1501268 K 25 Setting the Position Detection System ...
Page 544: ...505 IB 1501268 K 26 Setting the Tool Entry Prohibited Range ...
Page 560: ...521 IB 1501268 K 27 Setting the Machine Error Compensation ...
Page 578: ...539 IB 1501268 K 28 Setting the Position Switches ...
Page 582: ...543 IB 1501268 K 29 Setting the Backlash Compensation ...
Page 590: ...551 IB 1501268 K 30 Confirming the Spindle Operation ...
Page 594: ...555 IB 1501268 K 31 Setting the Handy Terminal ...
Page 600: ...561 IB 1501268 K 32 Setting the Deceleration Check ...
Page 612: ...573 IB 1501268 K 33 Synchronous Control and Multiple axis Synchronization Control ...
Page 628: ...589 IB 1501268 K 34 Adjust S analog Screen ...
Page 633: ...M800W M80W Series Connection and Setup Manual 34 Adjust S analog Screen 594 IB 1501268 K ...
Page 634: ...595 IB 1501268 K 35 Device Open Parameter Screen ...
Page 640: ...601 IB 1501268 K 36 SRAM Open Parameter Screen ...
Page 646: ...607 IB 1501268 K 37 Data Backup and Restoration ...
Page 652: ...613 IB 1501268 K 38 Appx 1 Setting the System Lock ...
Page 656: ...617 IB 1501268 K 39 Appx 2 Protection Setting ...
Page 664: ...625 IB 1501268 K 40 Appx 3 Displaying Original Logo On Standard Screen ...
Page 666: ...627 IB 1501268 K 41 Appx 4 EMC Installation Guidelines ...
Page 678: ...639 IB 1501268 K 42 Appx 5 Restrictions for Lithium Batteries ...
Page 686: ...647 IB 1501268 K 43 Appx 6 Precautions for Compliance to UL c UL Standards ...
Page 698: ......
Page 702: ......