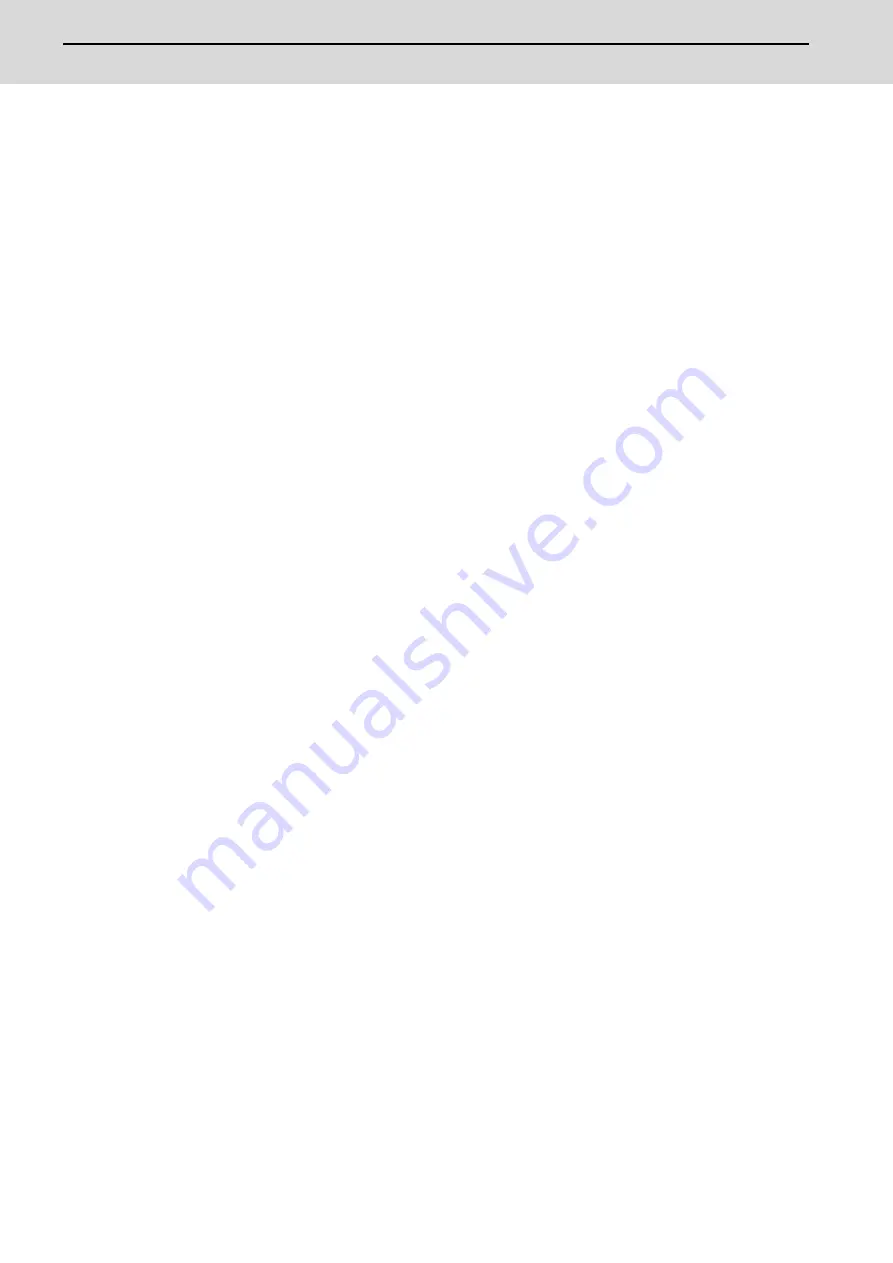
M800W/M80W Series Connection and Setup Manual
25 Setting the Position Detection System
502
IB-1501268-K
Grid point
The position encoder has a Z-phase that generates one pulse per rotation. The 0-point position of this Z-phase is the grid
point.
Thus, there is a grid point per rotation of the position encoder, and the machine has many grid points at a regular pitch.
The grid point can be set at intervals of grid space by setting the grid space (#2029 grspc). Thus, multiple grid points can
be set per encoder rotation.
Grid amount
The grid amount is the distance from where the near-point detection limit switch leaves the near-point dog to the grid
point (electrical zero point) as the dog-type reference position return is executed.
The grid amount can be confirmed on the DRIVE MONITOR screen.
After setting the grid mask, the grid amount shows the distance from the grid mask OFF to the grid point.
G28 rapid traverse rate (#2025 G28rap)
Set the feedrate for dog-type reference position return in manual operation and the automatic operation.
The rapid traverse rate (#2001 rapid) is applied for the feedrate during the high-speed reference position return.
G28 approach speed (#2026 G28crp)
Set the approach speed to the reference position after decelerating to a stop by the near-dog detection. Since the
approach speed is accelerated and decelerated in steps (no-acceleration/deceleration), the mechanical shock, etc. could
occur if the speed is too large. The G28 approach speed should be set between 100 and 300 mm/min., or within 500
mm/min. at the fastest.
Reference position shift amount (#2027 G28sft)
When shifting the reference position from the electrical zero point, set the shift amount.
The shifting direction can be set only in the reference position return direction.
If the reference position shift amount is "0", the grid point (electrical zero point) will be the reference position.
Grid mask amount (#2028 grmask)
The first grid point after the dog OFF is regarded as the electrical zero point.
If the grid point is at the position where the near-point dog is kicked OFF, the position of electrical zero point may be at
the grid point where the dog is kicked OFF or at the next grid point because of the delay of the limit switch operation. This
causes a deviation of reference position by the amount of the grid space. Thus, the position that the dog is kicked OFF
needs to be at the approximate center of the grid space.
Adjustments are made by setting the grid mask amount or changing the near-point dog.
Setting the grid mask has the same effect as lengthening the near-point dog. Refer to the previous procedures for setting
the grid mask amount.
Grid space (#2029 grspc)
Set the distance between grids.
Set either the ball screw pitch value (#2218 PIT) or the movement amount per motor rotation as the normal grid space.
To make the grid space smaller, set a divisor of the grid space.
<Calculation method for movement amount per motor rotation>
(1) When linear feed mechanism is a ball screw:
The movement amount per motor rotation = the motor side gear ration / the machine side gear ratio x the ball
screw pitch
(2) When linear feed mechanism is a rack and pinion:
The movement amount per motor rotation = the motor side gear ration / the machine side gear ratio x number
of pinion gear teeth x the rack pitch
(3) For the rotary axis:
The movement angle per motor rotation = the motor side gear ration / the machine side gear ratio x 360
Summary of Contents for M800W Series
Page 1: ......
Page 4: ......
Page 9: ......
Page 21: ......
Page 23: ......
Page 25: ......
Page 27: ......
Page 29: ......
Page 39: ......
Page 40: ...1 IB 1501268 K 1 System Basic Configuration ...
Page 42: ...3 IB 1501268 K 2 General Connection Diagram ...
Page 49: ...M800W M80W Series Connection and Setup Manual 2 General Connection Diagram 10 IB 1501268 K ...
Page 50: ...11 IB 1501268 K 3 List of Configuration ...
Page 60: ...21 IB 1501268 K 4 General Specifications ...
Page 245: ...M800W M80W Series Connection and Setup Manual 4 General Specifications 206 IB 1501268 K ...
Page 246: ...207 IB 1501268 K 5 Installation ...
Page 275: ...M800W M80W Series Connection and Setup Manual 5 Installation 236 IB 1501268 K ...
Page 276: ...237 IB 1501268 K 6 Precautions for Connecting ...
Page 284: ...245 IB 1501268 K 7 Connection of Control Unit ...
Page 315: ...M800W M80W Series Connection and Setup Manual 7 Connection of Control Unit 276 IB 1501268 K ...
Page 316: ...277 IB 1501268 K 8 Connection of Personal Computer Unit ...
Page 322: ...283 IB 1501268 K 9 Connection of Graphic Control Unit ...
Page 328: ...289 IB 1501268 K 10 Connection of Keyboard Unit ...
Page 330: ...291 IB 1501268 K 11 Connection of Operation Panel I O Unit ...
Page 350: ...311 IB 1501268 K 12 Connection of Remote I O Unit ...
Page 386: ...347 IB 1501268 K 13 Connection of Side Memory I F Unit ...
Page 388: ...349 IB 1501268 K 14 Connection of Manual Pulse Generator ...
Page 392: ...353 IB 1501268 K 15 Connection of Synchronous Feed Encoder ...
Page 394: ...355 IB 1501268 K 16 Connection of Machine Operation Panel ...
Page 406: ...367 IB 1501268 K 17 Connection of Handy Terminal ...
Page 408: ...369 IB 1501268 K 18 Cable ...
Page 443: ...M800W M80W Series Connection and Setup Manual 18 Cable 404 IB 1501268 K ...
Page 444: ...405 IB 1501268 K 19 Setup Outline ...
Page 450: ...411 IB 1501268 K 20 Setting the Hardware ...
Page 482: ...443 IB 1501268 K 21 Setting Up with HMI Integrated Installer ...
Page 486: ...447 IB 1501268 K 22 Setting the Parameters and Date Time ...
Page 492: ...453 IB 1501268 K 23 Sequence Program Writing ...
Page 516: ...477 IB 1501268 K 24 Confirming the Basic Operation ...
Page 522: ...483 IB 1501268 K 25 Setting the Position Detection System ...
Page 544: ...505 IB 1501268 K 26 Setting the Tool Entry Prohibited Range ...
Page 560: ...521 IB 1501268 K 27 Setting the Machine Error Compensation ...
Page 578: ...539 IB 1501268 K 28 Setting the Position Switches ...
Page 582: ...543 IB 1501268 K 29 Setting the Backlash Compensation ...
Page 590: ...551 IB 1501268 K 30 Confirming the Spindle Operation ...
Page 594: ...555 IB 1501268 K 31 Setting the Handy Terminal ...
Page 600: ...561 IB 1501268 K 32 Setting the Deceleration Check ...
Page 612: ...573 IB 1501268 K 33 Synchronous Control and Multiple axis Synchronization Control ...
Page 628: ...589 IB 1501268 K 34 Adjust S analog Screen ...
Page 633: ...M800W M80W Series Connection and Setup Manual 34 Adjust S analog Screen 594 IB 1501268 K ...
Page 634: ...595 IB 1501268 K 35 Device Open Parameter Screen ...
Page 640: ...601 IB 1501268 K 36 SRAM Open Parameter Screen ...
Page 646: ...607 IB 1501268 K 37 Data Backup and Restoration ...
Page 652: ...613 IB 1501268 K 38 Appx 1 Setting the System Lock ...
Page 656: ...617 IB 1501268 K 39 Appx 2 Protection Setting ...
Page 664: ...625 IB 1501268 K 40 Appx 3 Displaying Original Logo On Standard Screen ...
Page 666: ...627 IB 1501268 K 41 Appx 4 EMC Installation Guidelines ...
Page 678: ...639 IB 1501268 K 42 Appx 5 Restrictions for Lithium Batteries ...
Page 686: ...647 IB 1501268 K 43 Appx 6 Precautions for Compliance to UL c UL Standards ...
Page 698: ......
Page 702: ......