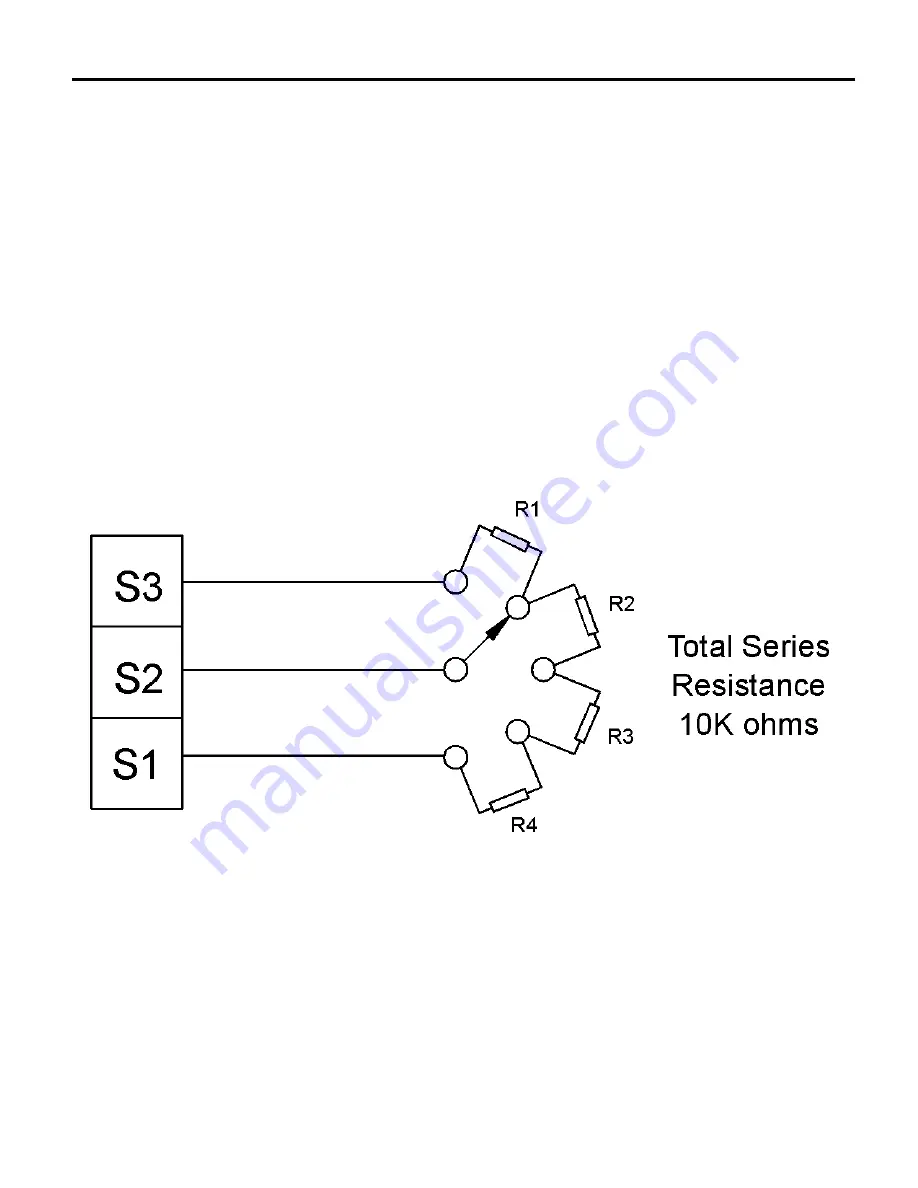
36
Application Notes
Figure 11. Multiple Fixed Speeds
Optional speed adjust potentiometer
connections
Multiple fixed speeds
Replace the speed adjust potentiometer with series resistors
with a total series resistance of 10K ohms (Figure 11). Add a
single pole, multi-position switch with the correct number of
positions for the desired number of fixed speeds.
250-0246r2_readers.qxd 6/7/01 10:51 AM Page 36
Summary of Contents for NRG-2Q Series
Page 1: ...User s Manual NRG 2Q Series Two Quadrant Regenerative PWM Drives for DC Brush Motors...
Page 12: ...6 Regenerative Drives Figure 2 Two Quadrant Operation...
Page 19: ...13 Installation Also see Dynamic brake resistor sizing page 23 Figure 3 NRG 2Q Connections...
Page 31: ...25 Operation Figure 7 Dynamic Braking Circuit Connection...
Page 57: ...Notes...
Page 58: ...Notes...