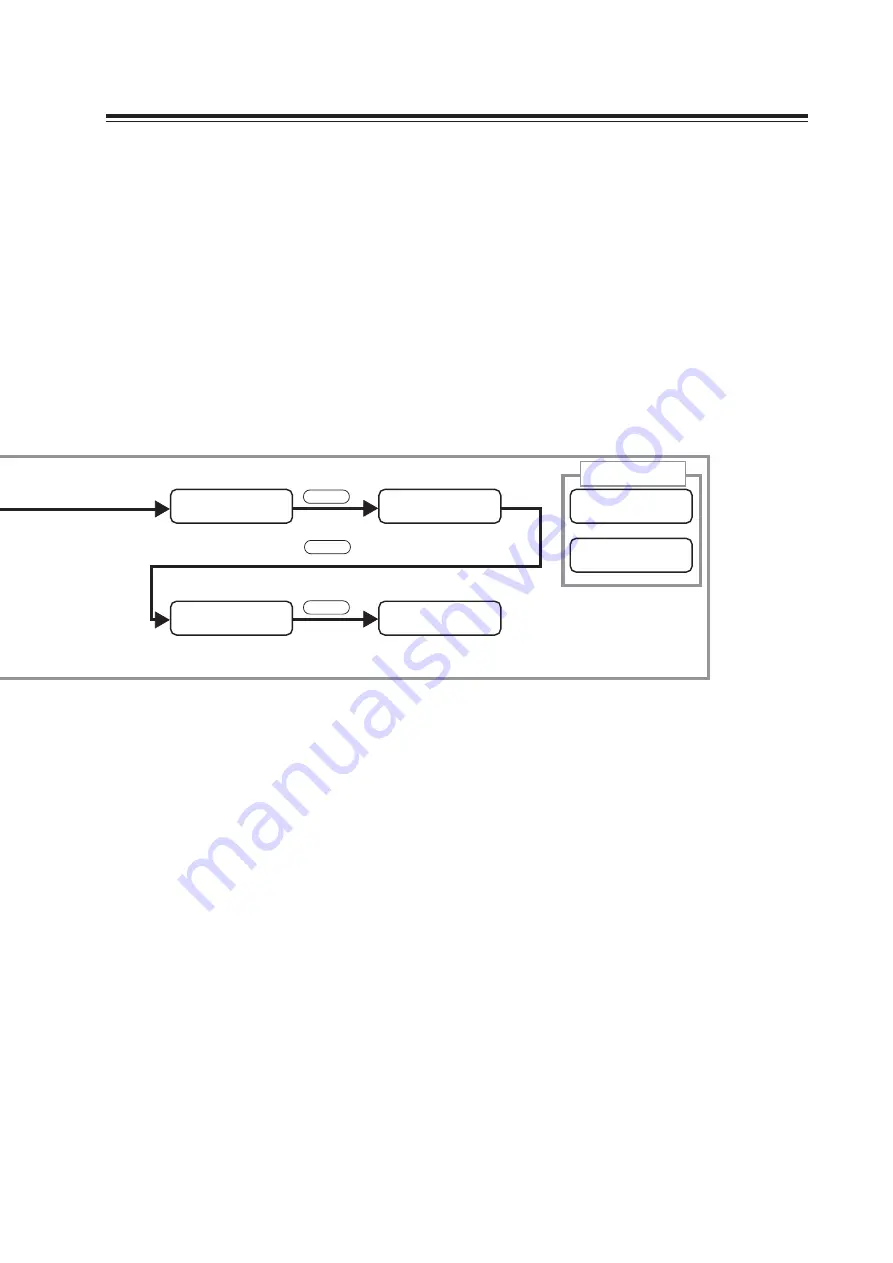
- A.17 -
ENTER
ENTER
Ink Type
Type :TPig
Ver1.00 MRL-IIC
SETUP<TYPE
∗
>
Display [V]Key
Error Info
Display [V]Key
Default Check NG
SET/LG/IK/MT/SV
Default Check OK
ENTER
12345678901234
12345678901234
12345678901234
12345678901234
If FUNC key
OR
X( ):Shows all currentry
occurred err
Display current set ink
Display FW ver and Command
X( ):Shows currently
SETUP condition
<
<
Function flowchart
Summary of Contents for DM2-1810
Page 2: ......
Page 18: ...xiv...
Page 72: ...3 20...
Page 98: ...5 18...
Page 108: ...6 10...
Page 116: ...A 8...
Page 117: ...A 9 Function flowchart...
Page 119: ...A 11 Filling 00 00 00 Display remaining time Function flowchart...
Page 129: ...A 21 TYPE Refresh Level3 TYPE mm inch mm X Level0 Level3 X inch Function flowchart...
Page 143: ...A 35...
Page 144: ...D201256 1 10 02082005...
Page 145: ......
Page 146: ...PrintedinJapan MIMAKI ENGINEERING Co Ltd TI TM...