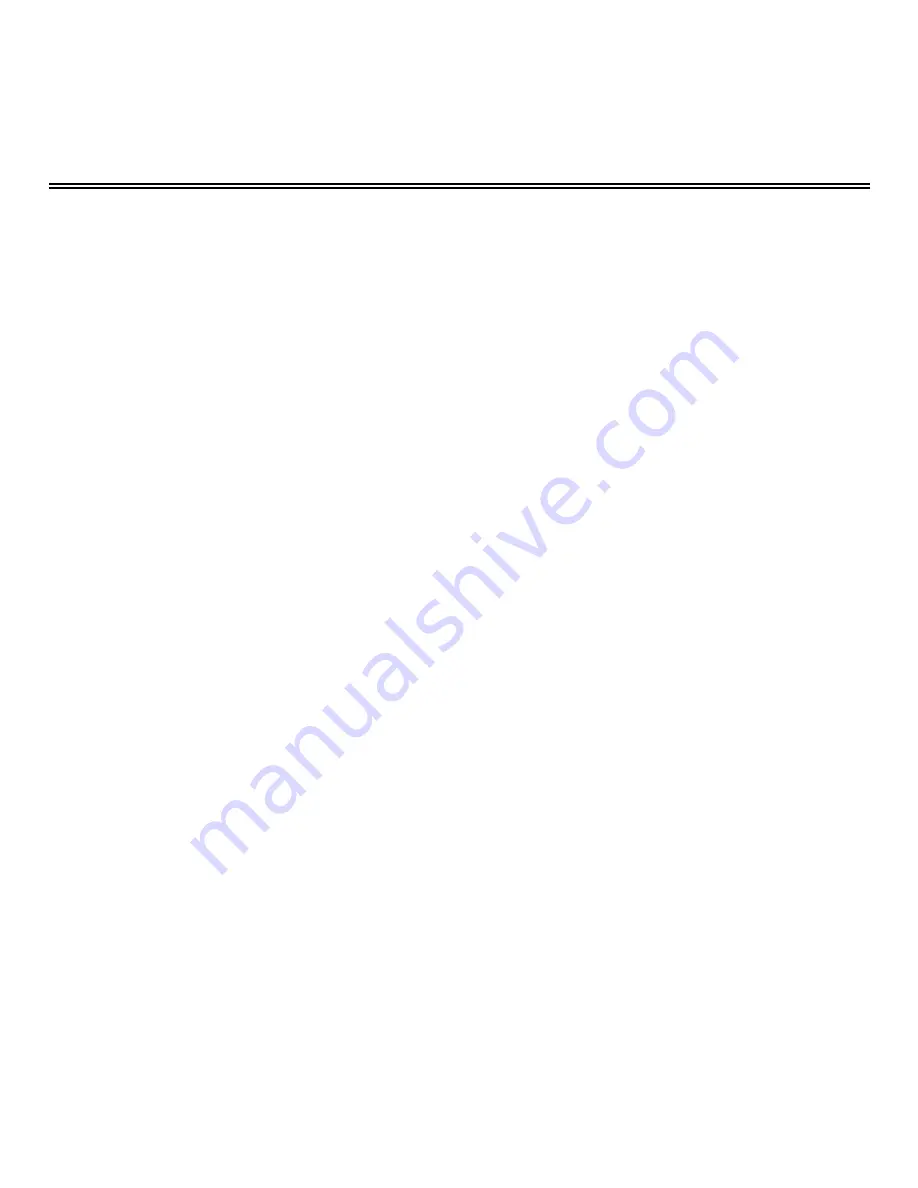
MSSMA407BE/85047V
È
DRIVE BASE COMPONENTS ON
HYDRO-CUSHION
®
MACHINES
Ê
General Description of Drive Mechanism
Major drive train components of the drive base include the following:
1. Drive motors: Wash, Drain, E-1 (low extract), E-2 (high extract) and Autospot. (The E1 motor is optional on
42" machines and standard on larger models except for 64" machines, which use one 2-speed extract motor.
Autospot is optional on divided cylinder machines and not applicable to open pocket machines.)
2. Belts and pulleys
3. Jackshaft (The jackshaft assembly is used on 52", 60", 64" and 72" machines only. On 42" and 48" machines,
the E2 (high extract) motor also serves as the jackshaft.)
4. Clutch and drum assembly
5. Gear reducer
6. Brake assembly (The brake is located on the drive base on 42" and 48" machines only. On larger models, it is
located elsewhere.)
7. Centrifugal switch
Ë
Concept of Drive Train Operation
—See FIGURE 1. During washing and inching, the cylinder is driven
by the wash motor through the gear reducer and the clutch, while the drain motor and the extract motors merely
coast. As soon as the drain valve opens, the wash motor is shut off and coasts with the extract motors, while the
drain motor drives the cylinder through the reducer and clutch. During extraction, both the wash and drain motors
are shut off, the clutch disengages, and the extract motor drives the cylinder through the jackshaft pulley and main
“V” belt drive. At the expiration of extract, the extract motor shuts off, the brake is applied, and either the drain or
wash motor (depending upon whether the drain valve is open or closed) starts and runs idle while the brake decel-
erates the machine. When the machine has slowed down sufficiently to actuate the centrifugal switch, the brake is
automatically released, and the clutch engages, returning the machine to wash or drain speed.
Ê
Advance Preparations for Drive Assembly Maintenance
The drive train on your Milnor
®
machine has been designed to give long, trouble-free service under continu-
ous use. Strict adherence to the lubrication schedule, proper belt tensioning, and the normal good practice of inspect-
ing your machine regularly for possible problems is the best way of prolonging service life.
Eventually, however, drive train components may require replacement. If this becomes necessary, the follow-
ing preparations and precautions will help to minimize down time:
1. Inspect belts regularly and purchase a replacement set for future use, before those on your machine become se-
verely worn. This is especially important for the main drive belts. Purchase a belt tension tester (see “V-
BELT TENSION ADJUSTMENTS”) and familiarize yourself with its use. It is also recommended to stock
an extra clutch tire.
2. Although any motor can fail with no prior warning, two signs of potential failure are 1) motor running slower
than normal and 2) motor emitting a loud or unusual noise. If either condition is detected, immediately
check for voltage fluctuations in your electrical supply. Fluctuations greater than 10% below or 10% above
those specified may cause the above symptoms and are extremely detrimental to the motor. If voltage fluc-
tuations are not detected, yet the symptom persists, then the motor will probably soon fail. A slow running
motor may indicate a bad rotor; whereas a loud or unusual noise likely indicates worn bearings. If possible,
make immediate repairs to avert complete failure. If this is not possible, make sure replacement parts will be
on hand when needed. Note however, that if a motor is allowed to fail, this is almost sure to require a new
or completely rebuilt motor.
3. Familiarize yourself with the various components of the drive base and with the procedures herein.
Gear re-
ducer
Wash motor
Drain
motor
E-2 mo-
tor
Brake (42" and 48" machines
only). Brake located else-
where on larger models.
A jackshaft (not shown) is
required on larger models
to support the jackshaft
pulley.
Jackshaft
pulley
E-1 mo-
tor
Centrifugal
switch
E1 motor is optional on
42" and 48" machines
and standard on larger
models
Clutch drum
(clutch tire in-
side)
Î
FIGURE 1
(MSSMA407BE)
Î
Drive Base: 42" and 48" Machines
(Shows Concept of Operation For All Hydro-cushion
®
Washers and Dye-extractors
®
)
Summary of Contents for 72044 WP2
Page 6: ......
Page 8: ......
Page 23: ...Section 1 Service and Maintenance ...
Page 40: ......
Page 42: ......
Page 43: ......
Page 44: ......
Page 64: ......
Page 65: ...Section 2 Shell and Door Assemblies ...
Page 70: ......
Page 72: ......
Page 76: ......
Page 79: ...Section 3 Drive Assemblies ...
Page 90: ......
Page 93: ......
Page 99: ......
Page 100: ......
Page 103: ......
Page 110: ......
Page 111: ...Section 4 Bearing Assemblies ...
Page 122: ......
Page 124: ......
Page 125: ...Section 5 Frame Pivots and Suspension ...
Page 126: ......
Page 134: ......
Page 138: ......
Page 140: ......
Page 143: ......
Page 146: ......
Page 147: ...Section 6 Control and Sensing Devices ...
Page 150: ......
Page 153: ...Section 7 Chemical Supply Devices ...
Page 156: ......
Page 158: ......
Page 159: ...Section 8 Water and Steam Piping and Assemblies ...
Page 160: ......
Page 169: ......
Page 173: ......
Page 178: ......
Page 179: ...Section 9 Pneumatic Piping and Assemblies ...
Page 183: ......
Page 184: ......
Page 185: ......
Page 188: ......
Page 195: ......