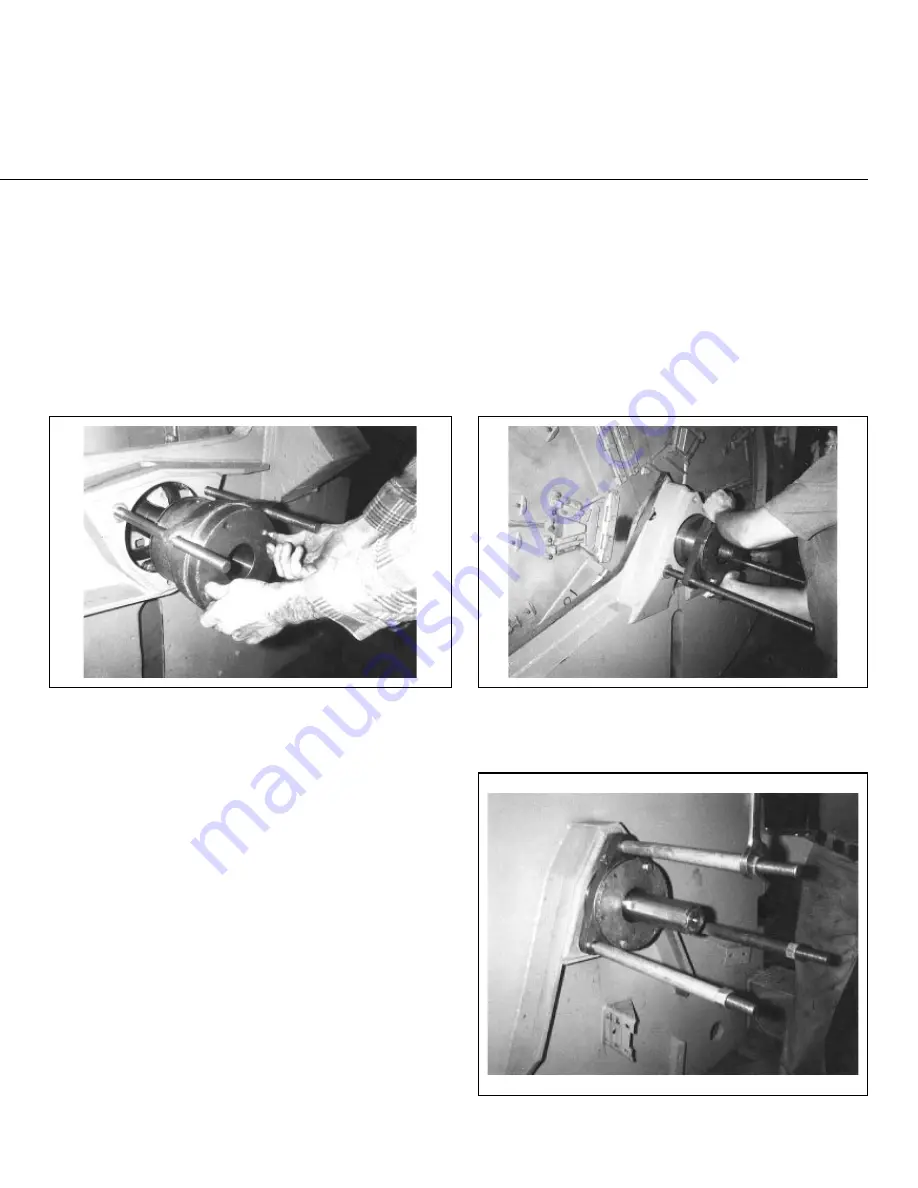
Ê
Replacing the Bearing Housing, Seal Sleeve,
and Seals (Front or Rear)
1. With the seal sleeve removed, press all old seals out of the bearing housing. Remove the large o-ring from the
outside of the housing. Thoroughly clean the bearing housing and flush out all grease passages to make cer-
tain they are unblocked. Remove the o-rings from the inside of the seal sleeve and clean the seal sleeve.
2. While the bearing housing is dissassembled, charge all grease passages with grease. This will assure that there
are no blockages.
3. Replace the o-rings in the seal sleeve and the large o-ring on the outside of the bearing housing. Replace with
new o-rings if the old ones are worn.
4. Press new seals into the bearing housing. You may gently work the seals in with a mallet and metal drift as
shown in FIGURE 5.
Each seal must be of the proper material and face the proper direction. The type of material
and direction the seal faces may differ from one seal to another within the same bearing
housing and also from one type of machine to another. It is essential to consult the Main
Bearing Assembly drawing for your machine for the proper part number and direction to
face each seal.
5. Slip the seal sleeve into the bearing housing as shown in FIGURE 6 below right, using care not to damage or
fold under any of the seal lips. Be sure to insert the sleeve in the proper direction (see Bearing Assembly draw-
ing).
NOTE: If both housings are being installed, install the rear housing first.
6. With two of the three temporary guide rods in position on the shell, place the bearing housing onto the guide
rods and install the seal sleeve setting fixture on to the bearing housing as shown in FIGURE 7. The seal
sleeve setting fixture prevents the seal sleeve from being pushed out of the housing as the housing is in-
serted into the shell. Note that the seal sleeve setting fixture and the bearing setting fixture are very similar,
but the seal sleeve setting fixture has a longer hub.
7. With a clean, lint free cloth, apply a coating of light machine oil to the outside of the housing, to assist in in-
stallation. Push the housing into the shell as shown in FIGURE 8. Once the housing is far enough into the
shell to support itself, place any shims back into position between the housing and the shell. Remove, then
replace guide rods if required to place shims under bearing housing pads.
8. Install the third guide rod, spacers if required, and hex-
nuts, using these to seat the housing fully, as shown
in FIGURE 9. Remove the seal sleeve setting fix-
ture.
9. Remove the guide rods and install the bearing housing
cap bolts. See “BOLT TORQUE REQUIRE-
MENTS” elsewhere, for proper torques.
10. With the grease gun, pump grease into the inner por-
tion of the bearing cavity, such that when the bear-
ing is installed, the space between the bearing and
the seals will be approximately 1/3 full of grease.
11 Proceed to “Measuring Unmounted Clearance . . .”
below, even if both the front and rear bearings are
being replaced. Once the rear bearing is installed,
the bearing housing replacement procedures may
then be repeated for the front (soil side) bearing hous-
ing.
Î
FIGURE 5
(MSSM0303AE)
Î
Installing Seals in
Bearing Housing
Î
FIGURE 6
(MSSM0303AE)
Î
Installing Seal Sleeve in
Bearing Housing
Î
FIGURE 7
(MSSM0303AE)
Î
Installing the Bearing Housing Setting
Fixture onto Housing (42" machine shown)
Î
FIGURE 8
(MSSM0303AE)
Î
Pushing the Bearing Housing into the
Shell (60" Rapid-load machine shown)
Î
FIGURE 9
(MSSM0303AE)
Î
Tightening the Bearing Housing
into the Shell (42" machine shown)
Summary of Contents for 72044 WP2
Page 6: ......
Page 8: ......
Page 23: ...Section 1 Service and Maintenance ...
Page 40: ......
Page 42: ......
Page 43: ......
Page 44: ......
Page 64: ......
Page 65: ...Section 2 Shell and Door Assemblies ...
Page 70: ......
Page 72: ......
Page 76: ......
Page 79: ...Section 3 Drive Assemblies ...
Page 90: ......
Page 93: ......
Page 99: ......
Page 100: ......
Page 103: ......
Page 110: ......
Page 111: ...Section 4 Bearing Assemblies ...
Page 122: ......
Page 124: ......
Page 125: ...Section 5 Frame Pivots and Suspension ...
Page 126: ......
Page 134: ......
Page 138: ......
Page 140: ......
Page 143: ......
Page 146: ......
Page 147: ...Section 6 Control and Sensing Devices ...
Page 150: ......
Page 153: ...Section 7 Chemical Supply Devices ...
Page 156: ......
Page 158: ......
Page 159: ...Section 8 Water and Steam Piping and Assemblies ...
Page 160: ......
Page 169: ......
Page 173: ......
Page 178: ......
Page 179: ...Section 9 Pneumatic Piping and Assemblies ...
Page 183: ......
Page 184: ......
Page 185: ......
Page 188: ......
Page 195: ......