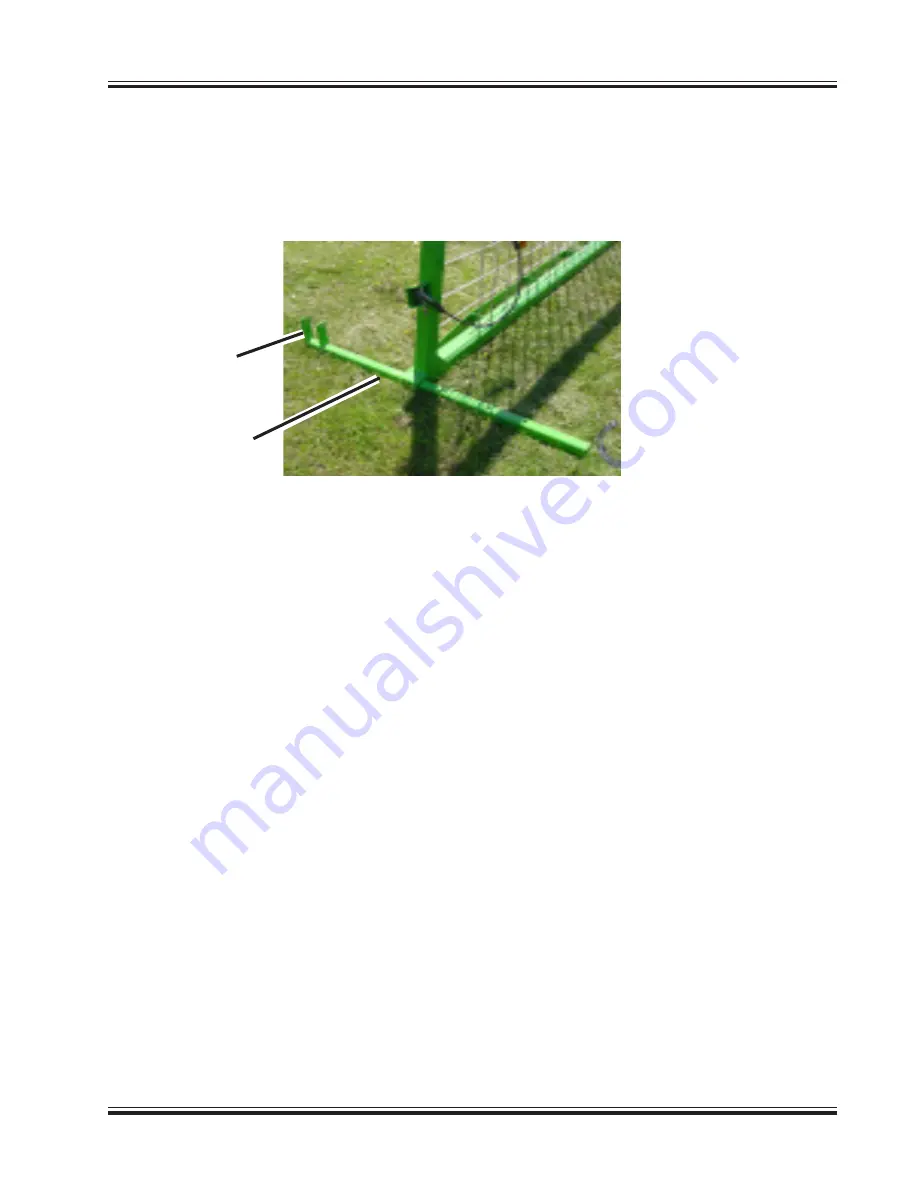
21
5.
Reassemble the bolt and nut into the support feet tabs. Remove the support feet from the
pockets in the tunnel. Insert the support feet into the pockets on the backstop with the tabs to
the rear of the backstop. The feet will help hold the backstop in the upright position.
NOTE:
After two loads are placed in the bag, remove the feet from the backstop and continue bag-
ging.
6.
Pull the bagger forward, giving yourself plenty of room to move the wheels and to install the
bag onto the tunnel.
Support Feet
In Backstop
Pockets
Tabs