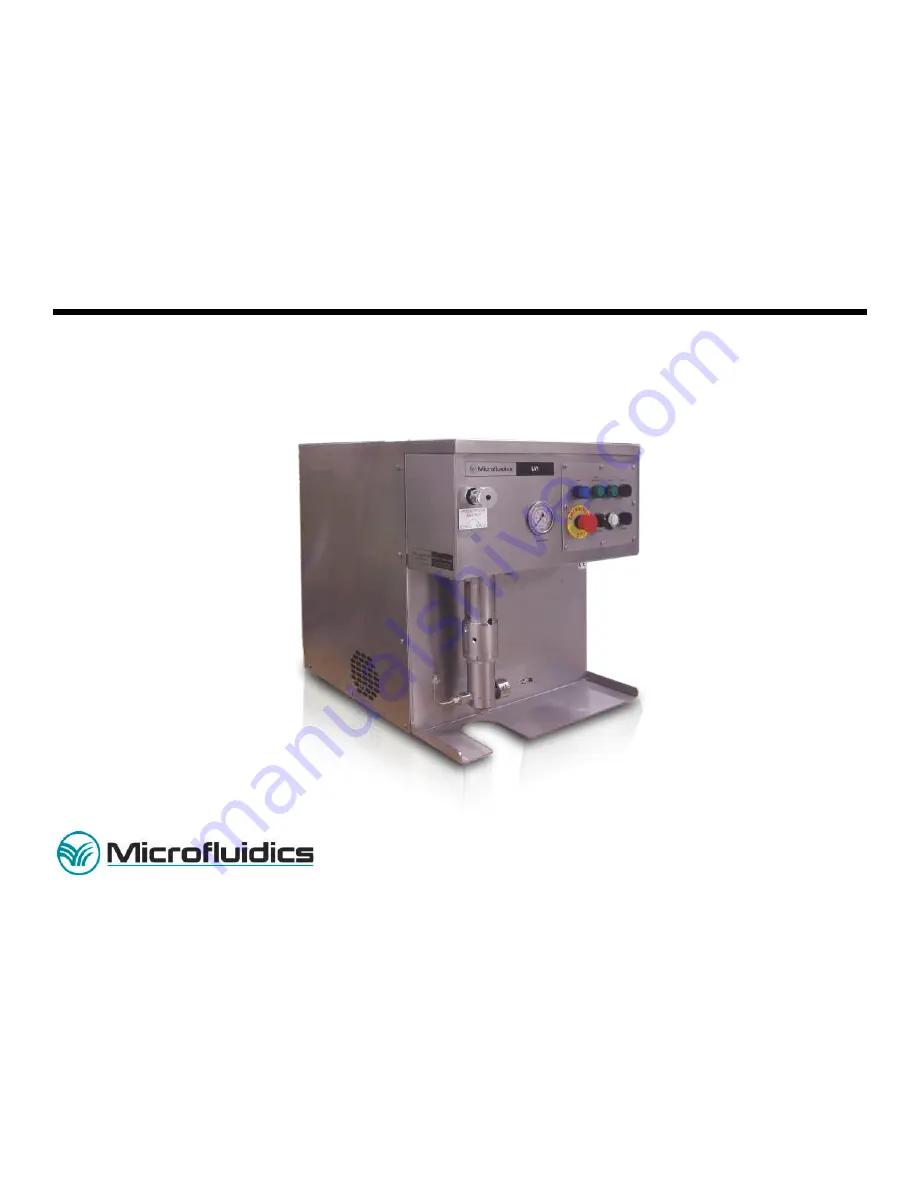
MODEL LV1 SERIES
MICROFLUIDIZER
®
PROCESSOR
User Manual
30 Ossipee Rd
P.O. Box 9101
Newton, MA 02464-9101
Phone 617-969-5452
Fax 617-965-1213
[email protected]
www.microfluidicscorp.com
Part No. 85.0098
MODEL LV1 SERIES
MICROFLUIDIZER
®
PROCESSOR
User Manual
30 Ossipee Rd
P.O. Box 9101
Newton, MA 02464-9101
Phone 617-969-5452
Fax 617-965-1213
[email protected]
www.microfluidicscorp.com
Part No. 85.0098