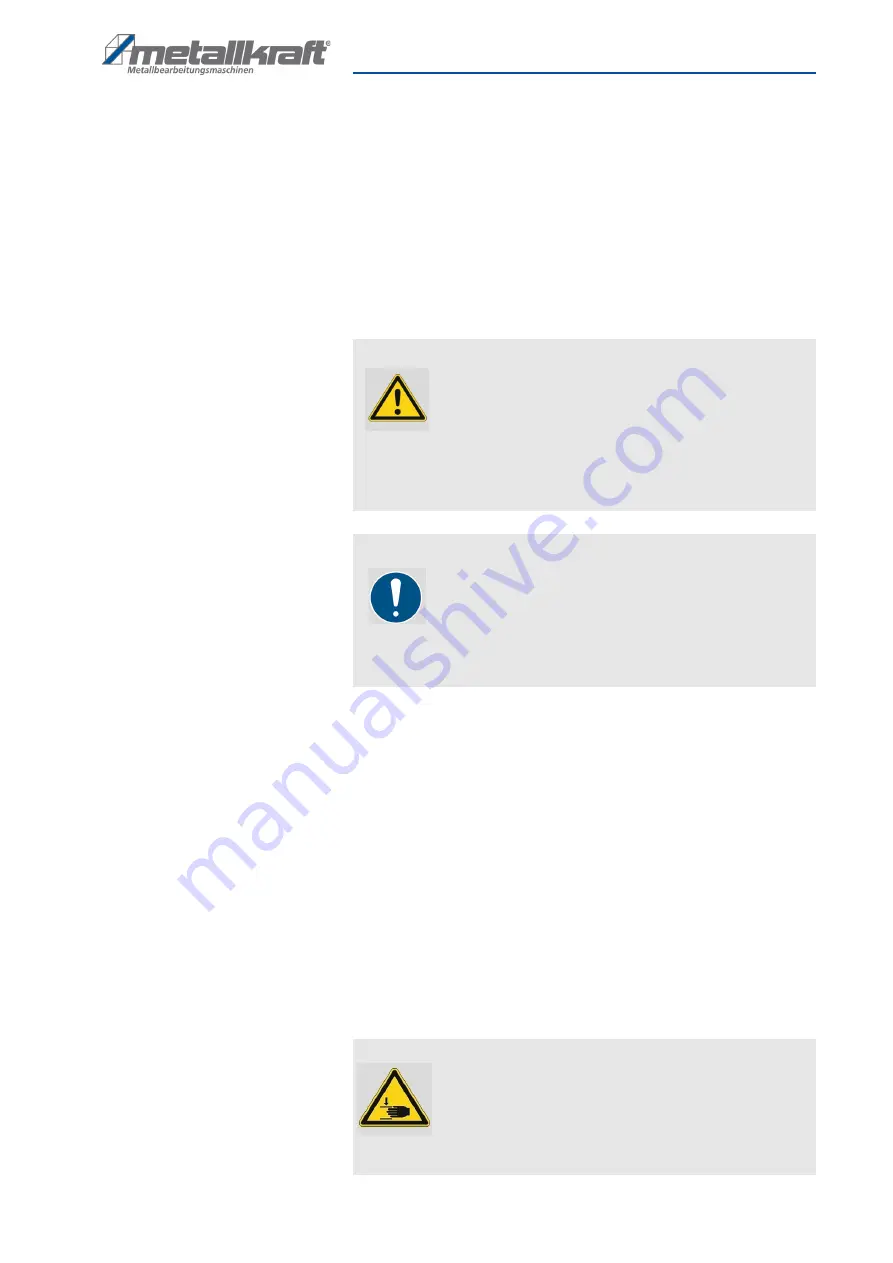
Assembly and connection
WPP Series | Version 1.02
15
6.1 Scope of delivery
- 2-piece prism set for inserting round material
- Winch for raising and lowering the table (at WPP 30)
7
Assembly and connection
7.1 Installation location
Design the work area around the workshop press in accordance with local
safety regulations.
In order to achieve good functionality and a long life of the workshop press,
the installation site should meet the following criteria.
- The ground must be level, firm and vibration-free.
- The foundation must not let any lubricant through.
- The installation or working area must be dry and well ventilated and
there must be no risk of fire or explosion.
- Do not operate machines that cause dust and chips near the workshop
press.
- There must be sufficient space for the operating personnel, for material
transport as well as for adjustment and maintenance work.
- The site must have good lighting. (Minimum value: 300 lux, measured at
the tool tip). With lower illuminance, additional lighting must be ensured,
for example by means of a separate workplace luminaire.
- Working temperature range + 10 ° C to + 50 ° C
Installation of the workshop press
WARNING!
Danger to life due to undersized buildings!
Overloading of ceiling structures leads to serious property
damage and bodily injury up to death!
- If the workshop press is placed on a self-supporting build-
ing ceiling, the dynamic loads due to the movements must
be taken into account - the foundation must bear the work-
shop press.
NOTE!
Property damage due to uneven ground!
An uneven surface causes deformations within the work-
shop press. This leads to an inaccurate machining of the
workpieces.
- Set up the workshop press on a flat, vibration-free and
even surface.
WARNING!
Risk of crushing!
The workshop press can tilt when setting up and cause
serious injuries.
- The workshop press must be set up by at least 2 people
together.
Summary of Contents for 4001015
Page 1: ...WPP 15 Operating instructions WPP 15 WPP S ERIES Hydraulic workshop press WPP 20 WPP 30 WPP 30...
Page 29: ...Spare parts WPP Series Version 1 02 29 Fig 16 Spare parts drawing 2 WPP 15 and 20 Hydraulic...
Page 30: ...30 WPP Series Version 1 02 Spare parts Fig 17 Spare part drawing 3 WPP 30...
Page 31: ...Spare parts WPP Series Version 1 02 31 Fig 18 Spare part drawing 4 WPP 30 Hydraulic...
Page 35: ...Notes WPP Series Version 1 02 35 15 Notes...
Page 36: ...www metallkraft de...