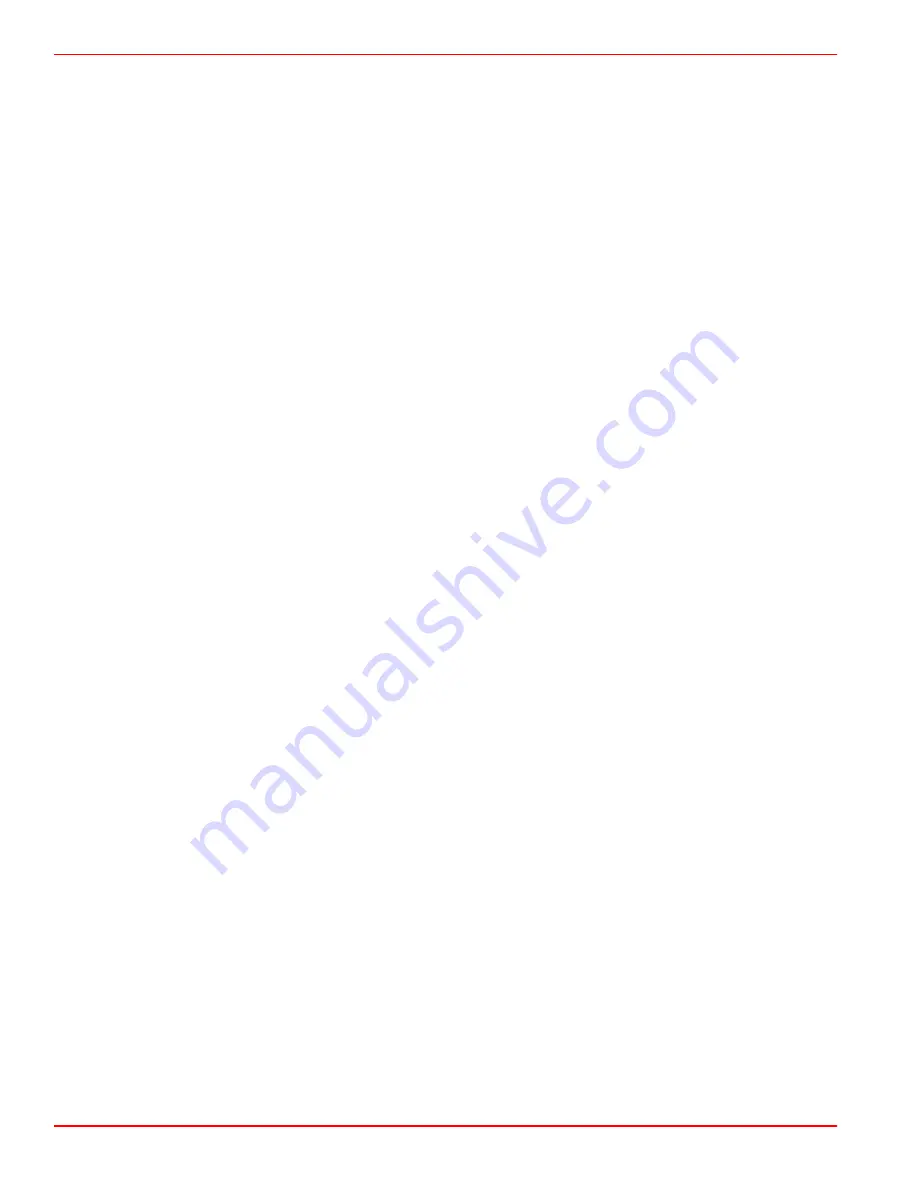
Pump Unit
Page 5A-20
90-8M0050731 MAY 2011
General Service Recommendations
There may be more than one way to disassemble or reassemble a particular part. It is recommended that the entire procedure be
read prior to repair.
IMPORTANT: Read the following before attempting any repairs.
Disassembly of a subassembly may not be necessary until cleaning and inspection reveals that disassembly is required for
replacement of one or more components.
Service procedure order in this section is a normal disassembly/reassembly sequence. It is suggested that the sequence be
followed without deviation to assure proper repairs. When performing partial repairs, follow the instructions to the point where the
desired component can be replaced, then proceed to reassembly and installation of that component in the reassembly part of this
section. Use the
Table of Contents
to find the correct page number.
Threaded parts are right‑hand (RH), unless otherwise indicated.
When holding, pressing, or driving is required, use soft metal vise jaw protectors or wood for protection of parts. Use a suitable
mandrel that will contact only the bearing race when pressing or driving bearings.
Whenever compressed air is used to dry a part, verify that no water is present in the air line.
Bearings
Upon disassembly of the gear housing, all bearings must be cleaned and inspected. Clean the bearings with solvent and dry with
compressed air. Air should be directed at the bearing so that it passes through the bearing. Do not spin the bearing with compressed
air, as this may cause the bearing to score from lack of lubrication. After cleaning, lubricate the bearings with High Performance
Gear Lubricant. Do not lubricate the tapered bearing cups until after inspection.
Inspect all bearings for roughness, catches, and bearing race side wear. Work the inner bearing race in and out, while holding the
outer race, to check for side wear.
When inspecting the tapered bearings, determine the condition of the rollers and the inner bearing race by inspecting the bearing
cup for pits, scoring, grooves, uneven wear, imbedded particles, and/or discoloration from overheating. Always replace the tapered
bearing and race as a set.
Inspect the gear housing for bearing races that have spun in their respective bores. If the race has spun, the gear housing must
be replaced.
Roller bearing condition is determined by inspecting the bearing surface of the shaft that the roller bearing supports. Check the
shaft surface for pits, scoring, grooves, imbedded particles, uneven wear, and/or discoloration from overheating. The shaft and
bearing must be replaced if the conditions described are found.
Shims
Keep a record of all shim amounts and their location during disassembly to aid in reassembly. Be sure to follow the shimming
instructions during reassembly, as gears must be installed to the correct depth and have the correct amount of backlash to avoid
noisy operation and premature gear failure.
Seals
As a normal procedure, all O‑rings and oil seals should be replaced without regard to appearance. To prevent leakage around oil
seals, apply Loctite 271 Threadlocker to the outer diameter of all metal case oil seals. When using Loctite on seals or threads,
the surfaces must be clean and dry. To ease installation, apply 2‑4‑C with Teflon on all O‑rings. To prevent wear, apply 2‑4‑C with
Teflon on the l.D. of oil seals.
Principles of Operation
NOTE: Due to running changes, some illustrations may not be exactly the same as your drive unit. Service procedures remain
the same unless otherwise noted.
Summary of Contents for 200 OptiMax Jet Drive
Page 5: ...Page iv ...
Page 30: ...General Information Notes 90 8M0050731 MAY 2011 Page 1C 5 ...
Page 43: ...General Information Notes Page 1C 18 90 8M0050731 MAY 2011 ...
Page 84: ...Ignition Notes 90 8M0050731 MAY 2011 Page 2A 3 ...
Page 89: ...Ignition Page 2A 8 90 8M0050731 MAY 2011 Electrical Plate Engine Harness 44731 1 2 3 4 5 6 ...
Page 147: ...Charging and Starting System Notes Page 2B 36 90 8M0050731 MAY 2011 ...
Page 153: ...Timing Synchronizing and Adjusting Notes Page 2C 6 90 8M0050731 MAY 2011 ...
Page 156: ...Fuel Pump Notes 90 8M0050731 MAY 2011 Page 3A 3 ...
Page 245: ...Direct Fuel Injection Notes Page 3B 82 90 8M0050731 MAY 2011 ...
Page 248: ...Oil Injection Notes 90 8M0050731 MAY 2011 Page 3C 3 ...
Page 261: ...Oil Injection Notes Page 3C 16 90 8M0050731 MAY 2011 ...
Page 277: ...Powerhead Page 4A 12 90 8M0050731 MAY 2011 Cylinder Head 14 44903 1 2 3 3 4 5 6 7 8 9 10 ...
Page 326: ...Powerhead 90 8M0050731 MAY 2011 Page 4A 61 Starboard Side Oil Hose Routing 45579 ...
Page 327: ...Powerhead Page 4A 62 90 8M0050731 MAY 2011 Port Side Oil Hose Routing 45580 ...
Page 339: ...Powerhead Notes Page 4A 74 90 8M0050731 MAY 2011 ...
Page 346: ...Cooling Notes 90 8M0050731 MAY 2011 Page 4B 7 ...
Page 349: ...Cooling Notes Page 4B 10 90 8M0050731 MAY 2011 ...