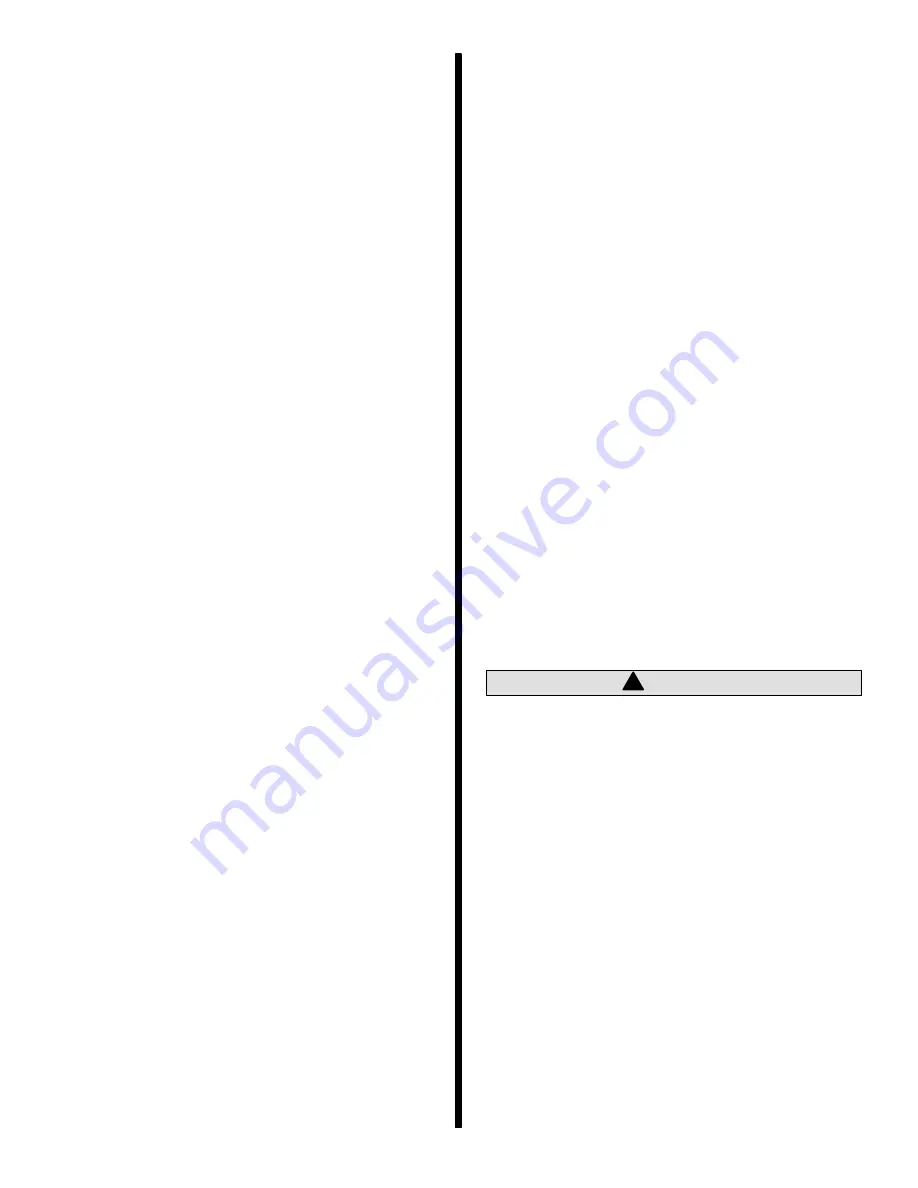
ENGINES - 3A - 23
90-816462 2-695
NOTE: A one-piece oil pan gasket may be reused if
it is still pliable and is not cracked, torn or otherwise
damaged.
4. Install oil pan. Starting from the center and work-
ing outward in each direction, tighten 1/4-20
threaded fasteners to 80 lb. in. (9 N·m) and
5/16-18 threaded fasteners to 165 lb. in. (19 N·m).
5. Install dipstick tube and dipstick.
6. Fill crankcase with required quantity of oil of spe-
cified viscosity. See Section 1B - “Maintenance.”
Oil Pump
The oil pump consists of two gears and a pressure
regulator valve enclosed in a two-piece housing. Oil
pump is driven by distributor shaft which is driven by
a helical gear on camshaft.
Removal
1. Remove oil pan as previously outlined.
2. Remove gasket carefully as the one-piece gasket
for the oil pan may be reused if still pliable and not
cracked, torn, etc.
3. Remove oil pump
Disassembly
1. Remove pump cover.
IMPORTANT: Mark gear teeth for reassembly with
same teeth indexing.
2. Remove idler gear and drive gear from pump
body.
3. Remove retaining pin, spring, and pressure regu-
lator valve from pump cover.
IMPORTANT: Do not remove pickup screen and
pipe assembly, unless replacement is necessary.
Loss of press fit condition could result in an air
leak and loss of oil pressure.
IMPORTANT: Do not disturb pickup screen on
pipe. This is serviced as an assembly.
4. If pickup screen and pipe assembly requires re-
placement, mount pump in a soft-jawed vise and
extract pipe from pump.
Cleaning and Inspection
1. Wash all parts in cleaning solvent and dry with
compressed air.
2. Inspect pump body and cover for cracks or exces-
sive wear.
3. Inspect pump gears for damage and excessive
wear.
4. Check for loose drive gear shaft in pump body.
5. Inspect inside of pump cover for wear that would
permit oil to leak past ends of gears.
IMPORTANT: Pump gears and body are not serv-
iced separately. If pump gears or body are dam-
aged or worn, replacement of entire oil pump as-
sembly is necessary.
6. Inspect pickup screen and pipe assembly for
damage to screen and pipe.
7. Check pressure regulator valve for fit.
Reassembly
!
CAUTION
Be careful of twisting, shearing or collapsing pipe
while installing in pump. Pickup screen must be
parallel to oil pan bottom when oil pump is in-
stalled.
If pickup screen and pipe assembly was removed,
mount pump in a soft-jawed vise, apply Quicksilver
Perfect Seal to end of new pipe and, using oil pump
suction pipe installer (J-21882), tap the pipe in place
with a hammer.
IMPORTANT: Oil internal parts liberally before in-
stallation.
1. Install pressure regulator valve and related parts.
2. Install drive gear in pump body.
3. Install idler gear in pump body with smooth side
of gear toward pump cover opening. Align marks
made in disassembly.
4. Fill gear cavity with engine oil.
Summary of Contents for 13
Page 1: ...13 Printed in U S A 90 816462 2 695 1995 Brunswick Corporation GM 4 Cylinder MARINE ENGINES ...
Page 2: ...90 816462 2 695 0 ...
Page 7: ...1 A IMPORTANT INFORMATION GENERAL INFORMATION 72000 ...
Page 15: ...1 B 50617 IMPORTANT INFORMATION MAINTENANCE ...
Page 36: ...1 C IMPORTANT INFORMATION TROUBLESHOOTING ...
Page 74: ...2 A 50633 REMOVAL AND INSTALLATION 4 CYL ALPHA ONE DRIVE ...
Page 88: ...3 A 26790 ENGINE 181 CID 3 0L 4 CYLINDER GM ENGINE ...
Page 137: ...4 A 72079 ELECTRICAL SYSTEMS STARTING SYSTEM ...
Page 170: ...4 B 71855 ELECTRICAL SYSTEMS IGNITION SYSTEM ...
Page 197: ...ELECTRICAL SYSTEMS CHARGING SYSTEM 4 C 72078 ...
Page 237: ...4 D 72747 ELECTRICAL SYSTEMS INSTRUMENTATION ...
Page 250: ...4 E 72938 ELECTRICAL SYSTEMS WIRING DIAGRAMS ...
Page 264: ...5 A FUEL SYSTEM FUEL PUMP ...
Page 271: ...5 B 72681 FUEL SYSTEM MERCARB 2 BARREL CARBURETOR ...
Page 300: ...6 A 50628 COOLING SYSTEM SEAWATER COOLED MODELS ...
Page 309: ...6 B 73665 COOLING SYSTEM CLOSED COOLING MODELS ...
Page 325: ...C 6 EXHAUST SYSTEM MANIFOLD ...
Page 331: ...7 A 71317 POWER STEERING PUMP ...