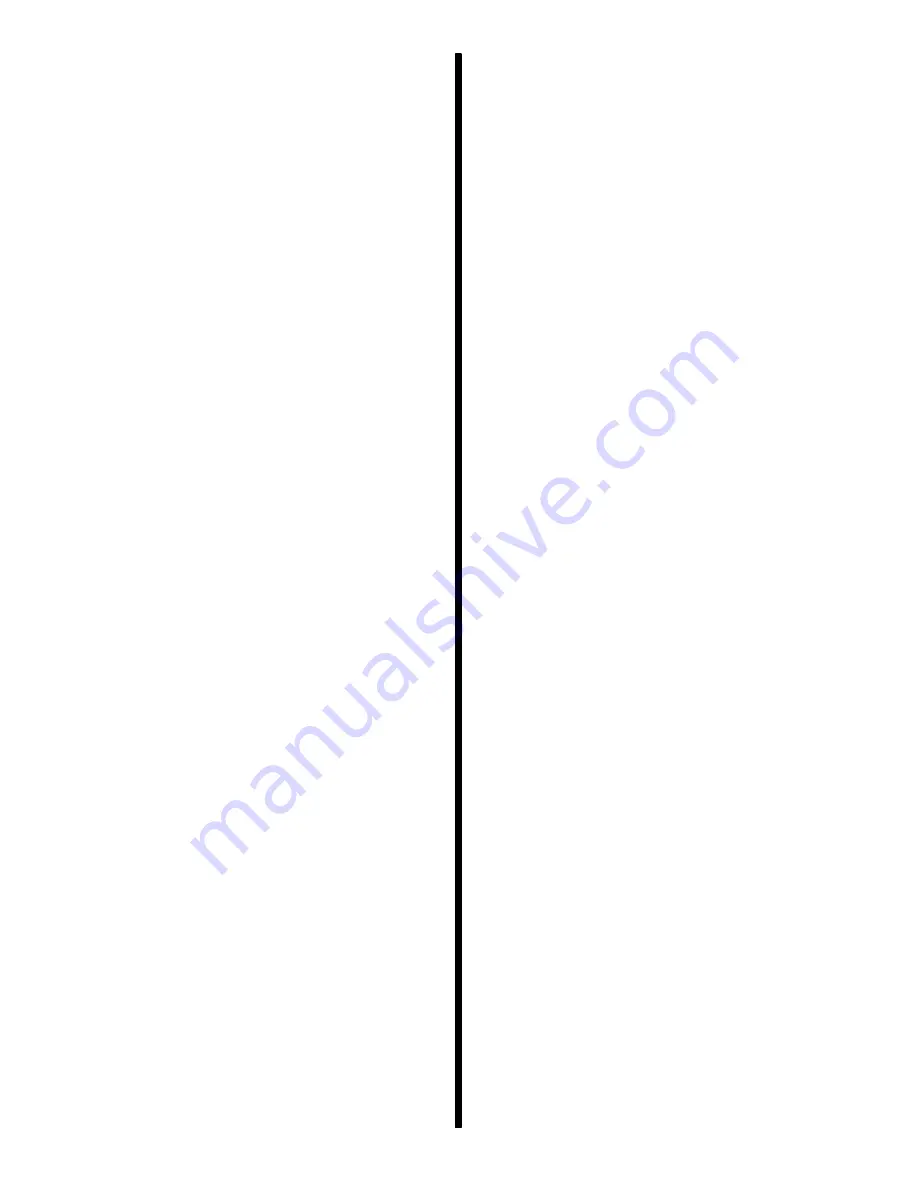
ENGINES - 3A - 13
90-816462 2-695
5. Repeat Steps 2-3-4 to adjust other valves.
6. Install valve covers, torque screws to 40 lb. in.
(4.5 N·m).
7. Adjust carburetor idle mixture and idle speed.
Check for leaks.
Hydraulic Valve Lifters
Hydraulic valve lifters require little attention. Lifters
are extremely simple in design. Normally, readjust-
ments are not necessary and servicing requires only
that care and cleanliness be exercised in the handling
of parts.
Locating Noisy Lifters
Locate a noisy valve lifter by using a piece of garden
hose approximately 4 ft. (1.2 m) in length. Place one
end of hose near end of each intake and exhaust
valve, with other end of hose to the ear. In this man-
ner, sound is localized, making it easy to determine
which lifter is at fault.
Another method is to place a finger on face of valve
spring retainer. If lifter is not functioning properly, a
distinct shock will be felt when valve returns to its
seat.
General types of valve lifter noise are as follows:
1. Hard rapping noise - usually caused by plunger
becoming tight in bore of lifter body so that return
spring cannot push plunger back up to working
position. Probable causes are:
a. Excessive varnish or carbon deposit, causing
abnormal stickiness.
b. Galling or “pickup” between plunger and bore
of lifter body, usually caused by an abrasive
piece of dirt or metal wedged between plung-
er and lifter body.
2. Moderate rapping noise - probable causes are:
a. Excessively high leakdown rate.
b. Leaky check valve seat.
c. Improper adjustment.
3. General noise throughout valve train - this will, in
most cases, be a definite indication of insufficient
oil supply or improper adjustment.
4. Intermittent clicking - probable causes are:
a. A microscopic piece of dirt momentarily
caught between ball seat and check valve
ball.
b. In rare cases, ball itself may be out of round
or have a flat spot.
c. Improper adjustment.
In most cases, where noise exists in one or more lift-
ers, all lifter units should be removed, disassembled,
cleaned in solvent, reassembled and reinstalled in
engine. If dirt, corrosion, carbon, etc., is shown to ex-
ist in one unit, it more likely exists in all the units; thus
it would only be a matter of time before all lifters
caused trouble.
Removal
1. Remove as previously outlined:
a. Rocker arm covers.
b. Intake manifold.
IMPORTANT: Keep valve push rod and hydraulic
lifter from each valve together as a matched set
and mark or store them so they can be reinstalled
in the same location later.
c. Rocker arm assemblies and push rods.
2. Remove fasteners from lifter retainers (restric-
tors) and remove retainers. Do not disturb lifters
at this time.
Summary of Contents for 13
Page 1: ...13 Printed in U S A 90 816462 2 695 1995 Brunswick Corporation GM 4 Cylinder MARINE ENGINES ...
Page 2: ...90 816462 2 695 0 ...
Page 7: ...1 A IMPORTANT INFORMATION GENERAL INFORMATION 72000 ...
Page 15: ...1 B 50617 IMPORTANT INFORMATION MAINTENANCE ...
Page 36: ...1 C IMPORTANT INFORMATION TROUBLESHOOTING ...
Page 74: ...2 A 50633 REMOVAL AND INSTALLATION 4 CYL ALPHA ONE DRIVE ...
Page 88: ...3 A 26790 ENGINE 181 CID 3 0L 4 CYLINDER GM ENGINE ...
Page 137: ...4 A 72079 ELECTRICAL SYSTEMS STARTING SYSTEM ...
Page 170: ...4 B 71855 ELECTRICAL SYSTEMS IGNITION SYSTEM ...
Page 197: ...ELECTRICAL SYSTEMS CHARGING SYSTEM 4 C 72078 ...
Page 237: ...4 D 72747 ELECTRICAL SYSTEMS INSTRUMENTATION ...
Page 250: ...4 E 72938 ELECTRICAL SYSTEMS WIRING DIAGRAMS ...
Page 264: ...5 A FUEL SYSTEM FUEL PUMP ...
Page 271: ...5 B 72681 FUEL SYSTEM MERCARB 2 BARREL CARBURETOR ...
Page 300: ...6 A 50628 COOLING SYSTEM SEAWATER COOLED MODELS ...
Page 309: ...6 B 73665 COOLING SYSTEM CLOSED COOLING MODELS ...
Page 325: ...C 6 EXHAUST SYSTEM MANIFOLD ...
Page 331: ...7 A 71317 POWER STEERING PUMP ...