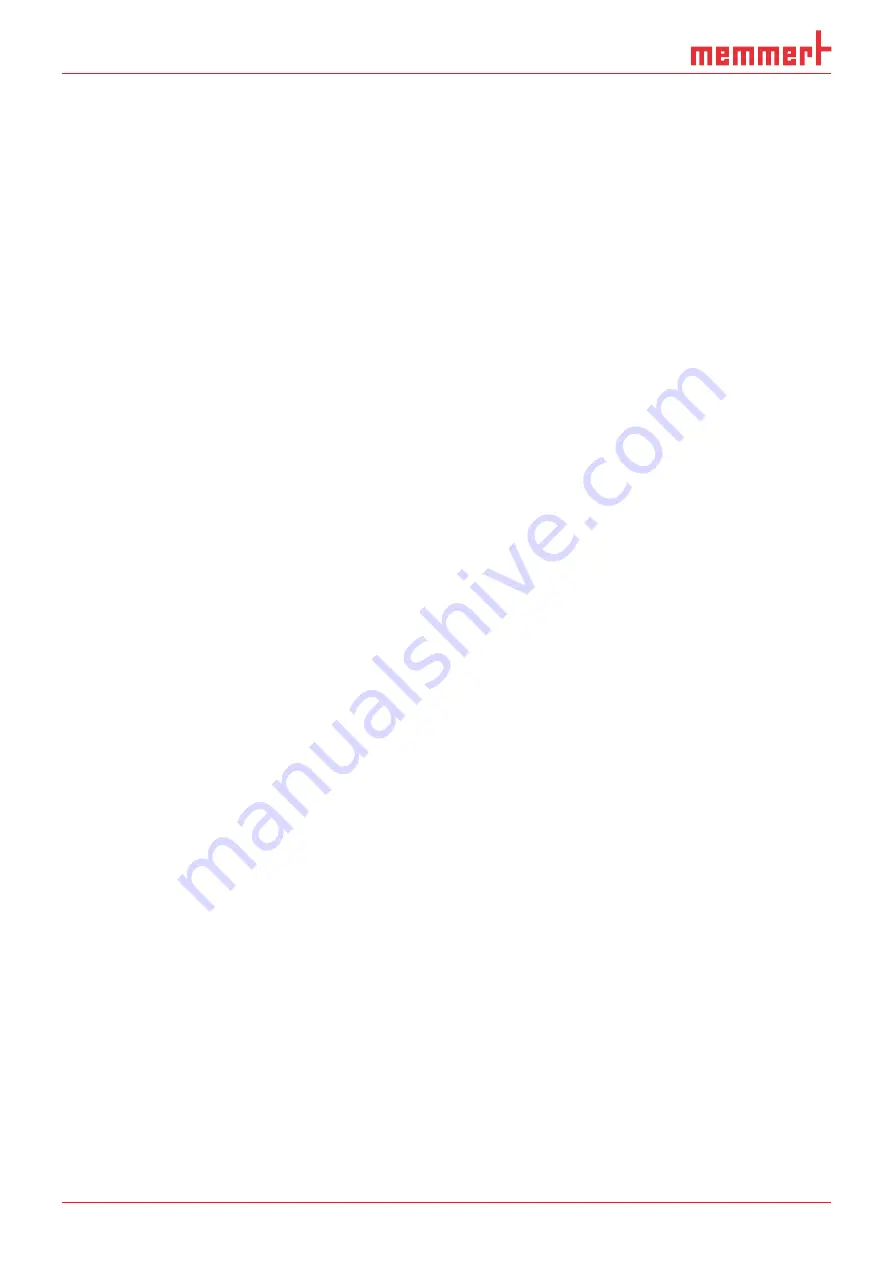
66
D39374 | Date 08/2018
Index
Switching off 43
Switching on 29
Switching output 14
T
Taking out of service 64
TB 39
Technical data 16
Temperature 34
Temperature deviation 55
Temperature limiter 39
Temperature monitor 37
,
39
Temperature monitoring
37
Temperature sensor 38
Thermoshelves 9
,
10
,
11
,
12
,
16
,
18
Tilt protection 23
Time 53
Timer 35
Timer mode 52
Transport 19
,
20
Transport damage 20
Troubleshooting 45
Turn control 33
TWW 38
TWW temperature monitor-
ing 38
Type plate 15
U
Unit 51
Unpacking 20
USB interface 14
,
61
USER ID 62
V
Vacuum pump 10
,
11
,
13
,
14
,
15
,
26
Vacuum pump connection
13
,
26
W
Warning messages 14
,
44
Weight 16
Summary of Contents for VO Series
Page 67: ......