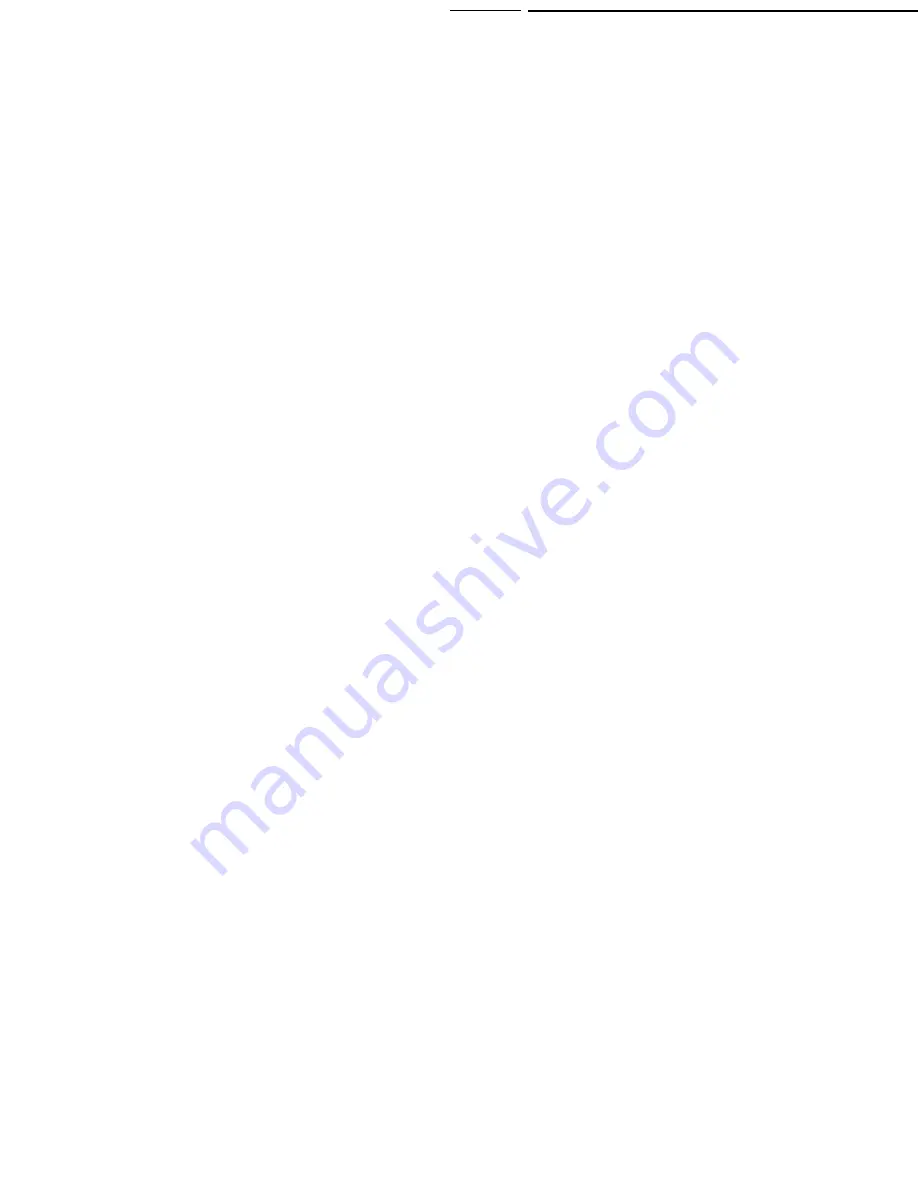
REFRIGERANT PIPING
REMOTE AIR COOLED CONDENSERS
For remote condenser application, such as an air
cooled condenser, the chillers, with and without
mounted receivers, are shipped containing a Refriger-
ant-22 holding charge. It is important that the unit be
kept tightly closed until the remote condenser is in-
stalled, piped to the unit and the high side evacuated.
Refrigerant piping,
to and from the remote unit,
should be sized and installed according to the latest
ASHRAE Guide. It is important that the piping be
properly supported with sound and vibration insulation
between tubing and hangerand that the discharge lines
be looped at the condenser and trapped at the com-
pressor to prevent refrigerant liquid from draining into
the compressor discharge manifold. Looping the dis-
charge line also provides greater line flexibility.
The discharge gas valve, liquid line solenoid,filter-
drier and moisture indicators are all provided as stan-
dard equipment with the SEASONPAK water chiller,
whether installed with remote or factory mounted re-
ceivers.
After the equipment is properly installed, the unit
may be charged with Refrigerant-22, then run at de-
sign load conditions, adding charge until the liquid
line sight-glass is clear, with no bubbles flowing to
expansion valve. Total operating charge will depend
on the air cooled condenser used and the length of
external piping, but generally will be equal to the
water cooled charge shown in Table 9, Page 26. With
S E A S O N T R O L l o w a m b i e n t c o n t r o l o n a i r c o o l e d
units, additional charge must then be added, as re-
quired (but not to exceed receiver pumpdown capacity)
UNIT LESS CONDENSER
SEASONPAK water chillers without condensers or
with mounted receivers require field piping to a re-
mote condenser of some type. As mentioned under the
R E M O T E C O N D E N S E R s e c t i o n a b o v e , r e f r i g e r a n t
piping should be sized and installed according to the
latest ASHRAE Guide. The design of refrigerant pip-
ing when using air cooled condensers involves a num-
ber of considerations not commonly associated with
other types of condensing equipment. The following
discussion is intended for use as a general guide to
sound, economical and trouble-free piping of air cool-
ed condensers.
On remote condenser applications, discharge line
mufflers are recommended. The mufflers should be in-
stalled as close to the compressor discharge as pos-
sible, If oil separators are used, they will usually
perform the same function as a muffler and will elim-
inate the need for one. A muffler wi II reduce discharge
line pulsations; particularly those which occur during
unloaded compressor operation
Discharge lines must be designed to handle oil
properly and to protect the compressor from damage
that may result from condensing liquid refrigerant in
the line during shutdown. Total friction loss for dis-
charge lines of
3
psi is considered good design. Care-
ful consideration must be given for sizing vertical
risers to insure that gas velocities are sufficient at
all operat,ing conditions to carry oil. If the velocity
in a vertical discharge riser is too low, considerable
oil may collect in the riser and the horizontal header,
causing the compressor to lose its oil and resultant
damage due to lack of lubrication.
Another danger is when the compressor load is in-
creased, the oil that had collected during reduced
loads may be carried as a slug through the system
and back to the evaporator, where a sudden increase
of oil concentration may cause slopover and damage
to the compressor.
Any horizontal run of discharge piping should be
pitched away from the compressor approximately 1/4"
per foot or more. This is necessary to move by gravity
any oil lying in the header. Oil pockets must be
avoided as oil needed in the compressor would col-
lect at such points and the compressor crankcase may
become starved.
It is recommended that any discharge lines coming
into a horizontal discharge header rise above the
center line of the discharge header. This is necessary
to prevent any oil or condensed liquid from draining
to the top heads when the compressor is not running.
In designing liquid line, it is important that the
liquid reach the expansion valve with a minimum of
flash gas since this gas will reduce the capacity of
the valve. Because “flashing” can be caused by a
pressure drop in the liquid lines, the pressure losses
due to friction and changes in static head should be
kept to a minimum.
The liquid line from the condenser to the receiver
MUST be sized for sewer flow operation (100 fpm/ve-
locity or less) and MUST be sloped to the receiver
with no traps in the line. Any shut off valve in this
line must have an orifice area equal to the inside area
of the line. Free drainage in this line is essential to
permit gas from the receiver to vent back to the con-
denser. Failure to adequately size and slope this line
wi II force liquid to back up into the condenser causing
high head pressure and bubbling sight glass.
A check valve should be installed in the liquid line
on installations that require operation at outside am-
bients below 60F. This prevents liquid migration to
the condenser and helps maintain a supply of refriger-
ant in the receiver for initial start up.
Typical Arrangements
Figure No. 11,
Page 9 illustrates a typical piping
arrangement involving a remote air cooled condenser
located at a higher elevation than the compressor and
receiver. This arrangement is commonly encountered
when the air cooled condenser is on a roof and the
compressor and receiver are on grade level or in a
basement equipment room.
In this case, the design of the discharge line is
very critical. If properly sized for full load condition,
the gas velocity might be too low at reduced loads to
carry oil up through the discharge line and condenser
coil. Reducing the discharge line size would increase
the gas velocity sufficiently at reduced load condi-
tions; however, when operating at full load, the line
might be greatly undersized and thereby create an ex-
cessive refrigerant pressure drop. This condition can
be overcome in one of the two following ways:
1. The discharge line may be properly sized for the
desired pressure drop at full load condition and an
oil separator installed at the bottom of the trap on
the discharge line from the compressor.
Page 8