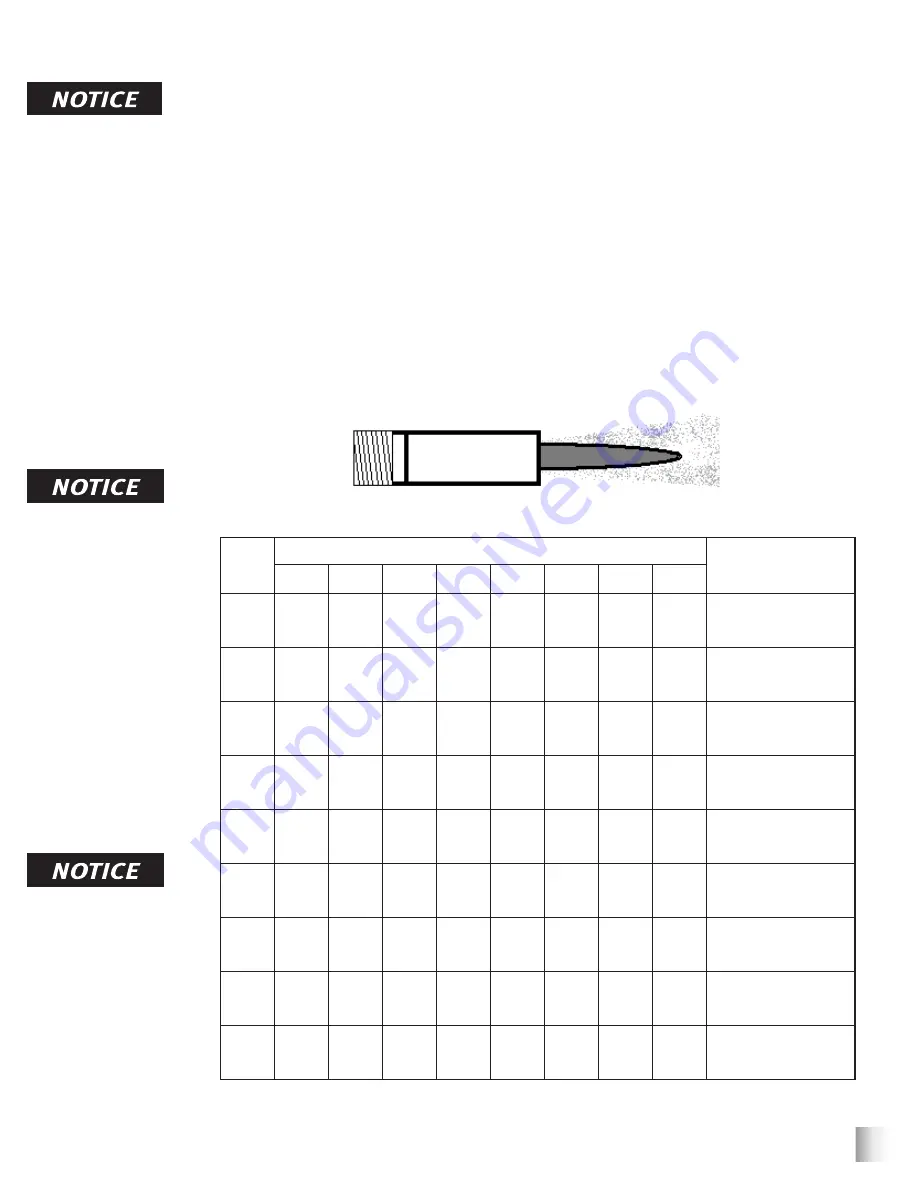
Blastmaster
®
Smart Box
6
Failure to comply with ANY NOTICE listed below could pose a hazard to personnel or property.
See Air & Abrasive Consumption Chart for estimated abrasive consumption rates and required air flow
(cubic feet per minute). Your system must meet these minimum requirements to ensure proper function and
performance.
When it comes to air & abrasive mixtures, more is not necessarily better. Optimum abrasive blasting efficiency
takes place when a lean air & abrasive mixture is used. To correctly set the abrasive metering valve, begin
with the valve fully closed and slowly increase the amount of abrasive entering the airstream. As you increase
the abrasive flow, watch for a “blue flame” at the exit of the abrasive blasting nozzle. Faster cutting, reduced
abrasive consumption and lower clean up costs, are benefits of the “blue flame”.
Abrasive blasting at optimal pressure for the abrasive used is critical to productivity. Example: For an abrasive
with an optimal abrasive blasting pressure of 100 psi at the abrasive blasting nozzle, one pound per square inch
of pressure loss will reduce abrasive blasting efficiency by 1.5%. A 10 psi reduction in air pressure will cause a
15% loss of efficiency. Use a Needle Pressure Gauge to identify pressure drops in your system. Consult with
your abrasive supplier for the requirements of your abrasive.
*Abrasive consumption is based on abrasive with a bulk density of 100 lbs per Cubic Foot
Air & Abrasive Consumption Chart*
Nozzle
Orifice
Pressure at the Nozzle (PSI)
Air (in cfm), Abrasive
& Compressor
Requirements
50
60
70
80
90
100
125
140
No. 2
(1/8ˮ)
11
67
2.5
13
77
3
15
88
3.5
17
101
4
18
112
4.5
20
123
5
25
152
5.5
28
170
6.2
Air (cfm)
Abrasive (lbs/hr)
Compressor Horsepower
No. 3
(3/16ˮ)
26
150
6
30
171
7
33
196
8
38
216
9
41
238
10
45
264
10
55
319
12
62
357
13
Air (cfm)
Abrasive (lbs/hr)
Compressor Horsepower
No. 4
(1/4ˮ)
47
268
11
54
312
12
61
354
14
68
408
16
74
448
17
81
494
18
98
608
22
110
681
25
Air (cfm)
Abrasive (lbs/hr)
Compressor Horsepower
No. 5
(5/16ˮ)
77
468
18
89
534
20
101
604
23
113
672
26
126
740
28
137
812
31
168
982
37
188
1100
41
Air (cfm)
Abrasive (lbs/hr)
Compressor Horsepower
No. 6
(3/8ˮ)
108
668
24
126
764
28
143
864
32
161
960
36
173
1052
39
196
1152
44
237
1393
52
265
1560
58
Air (cfm)
Abrasive (lbs/hr)
Compressor Horsepower
No. 7
(7/16ˮ)
147
896
33
170
1032
38
194
1176
44
217
1312
49
240
1448
54
254
1584
57
314
1931
69
352
2163
77
Air (cfm)
Abrasive (lbs/hr)
Compressor Horsepower
No. 8
(1/2ˮ)
195
1160
44
224
1336
50
252
1512
56
280
1680
63
309
1856
69
338
2024
75
409
2459
90
458
2754
101
Air (cfm)
Abrasive (lbs/hr)
Compressor Horsepower
No. 10
(5/8ˮ)
308
1875
68.5
356
2140
79.5
404
2422
90
452
2690
100.5
504
2973
112
548
3250
122
663
3932
146
742
4405
165
Air (cfm)
Abrasive (lbs/hr)
Compressor Horsepower
No. 12
(3/4ˮ)
432
2672
96
504
3056
112
572
3456
127
644
3840
143
692
4208
154
784
4608
174.5
948
5570
209
1062
6238
236
Air (cfm)
Abrasive (lbs/hr)
Compressor Horsepower
Inspect abrasive
blasting nozzle before
placing into service.
Damage to abrasive
blasting nozzle liner
or jacket may occur
during shipping. If you
receive a damaged
abrasive blasting nozzle,
contact your distributor
immediately for
replacement. Abrasive
blasting nozzles placed
into service may not
be returned. Abrasive
blasting nozzle liners
are made of fragile
materials and can be
damaged by rough
handling and striking
against hard surfaces.
Never use a damaged
abrasive blasting nozzle.
Replace abrasive
blasting nozzle if liner
or jacket is cracked
or damaged. Replace
abrasive blasting nozzle
if original orifice size
has worn 1/16” or more.
Determine abrasive
blasting nozzle wear by
inserting a drill bit 1/16”
larger than original size
of abrasive blasting
nozzle orifice. If the
drill bit passes through
abrasive blasting nozzle,
replacement is needed.
“Blue Flame”
AIR & ABRASIVE CONSUMPTION CHART