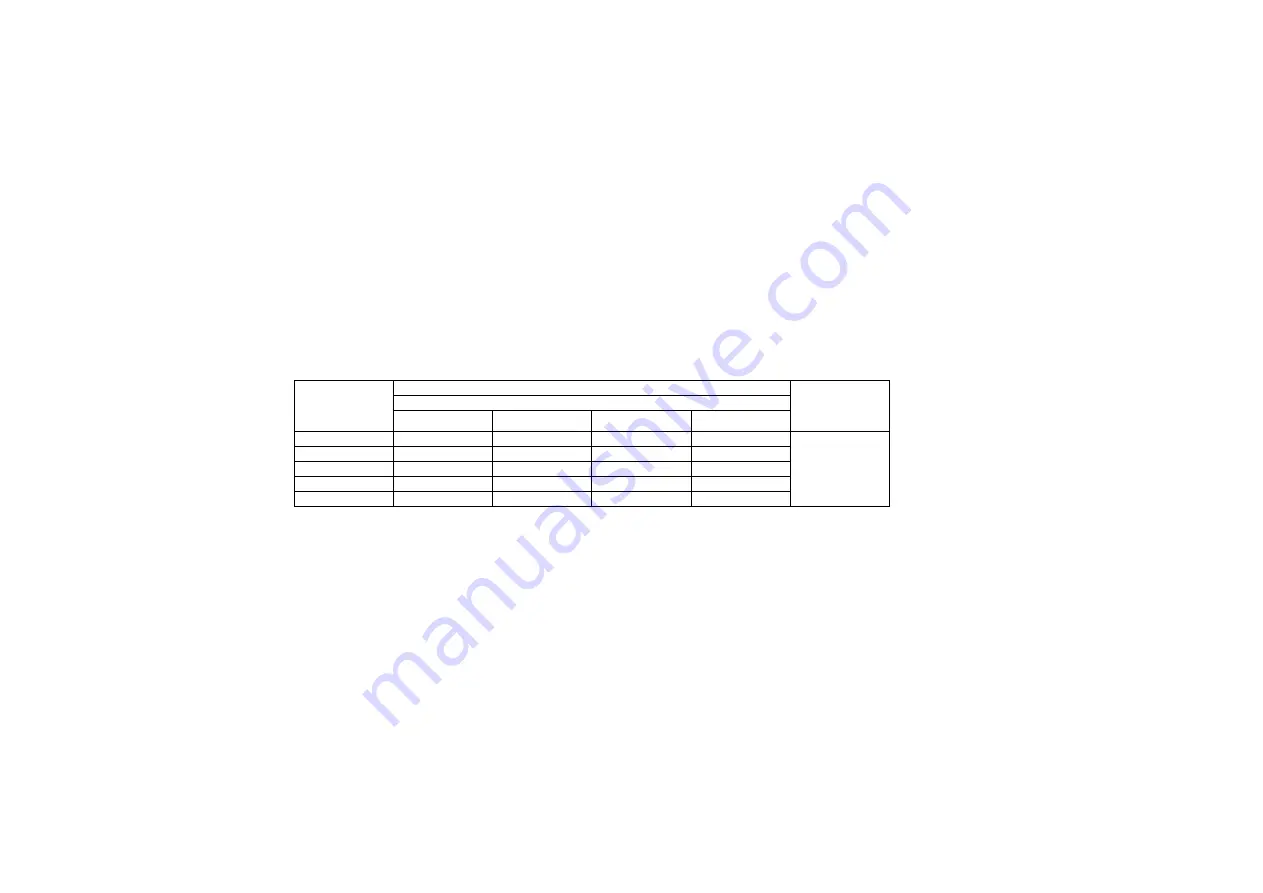
–10
9–
UG050W SELF-CONTAINED WATER-COOLED
NOTE:
These characteristics may vary depending on operating conditions.
Cycle Times
Freeze Time + Harvest Time = Total Cycle Time
Continued on next page …
Air Temp.
Entering
Condenser
°C
Freeze Time
Harvest Time
Times in minutes.
Water Temperature °C
10
15
21
32
10
16.32-18.56
1.4-3.5 min.
21
16.71-19.11
17.37-19.78
32
20.54-21.62
38
23.49-23.92
43
23.05-24.58
Summary of Contents for UG018A
Page 2: ......
Page 6: ...This Page Intentionally Left Blank ...
Page 12: ... 2 This Page Intentionally Left Blank ...
Page 20: ...10 Evaporator Spray Nozzles Toggle Switch Spray Bar Ice Chute ...
Page 36: ...26 dip switch Decrease Cube Size Factory Default Setting Increase Cube Size test button ...
Page 38: ...28 ...
Page 80: ...70 This Page Intentionally Left Blank ...
Page 128: ... 118 This Page Intentionally Left Blank ...
Page 135: ... 125 ...