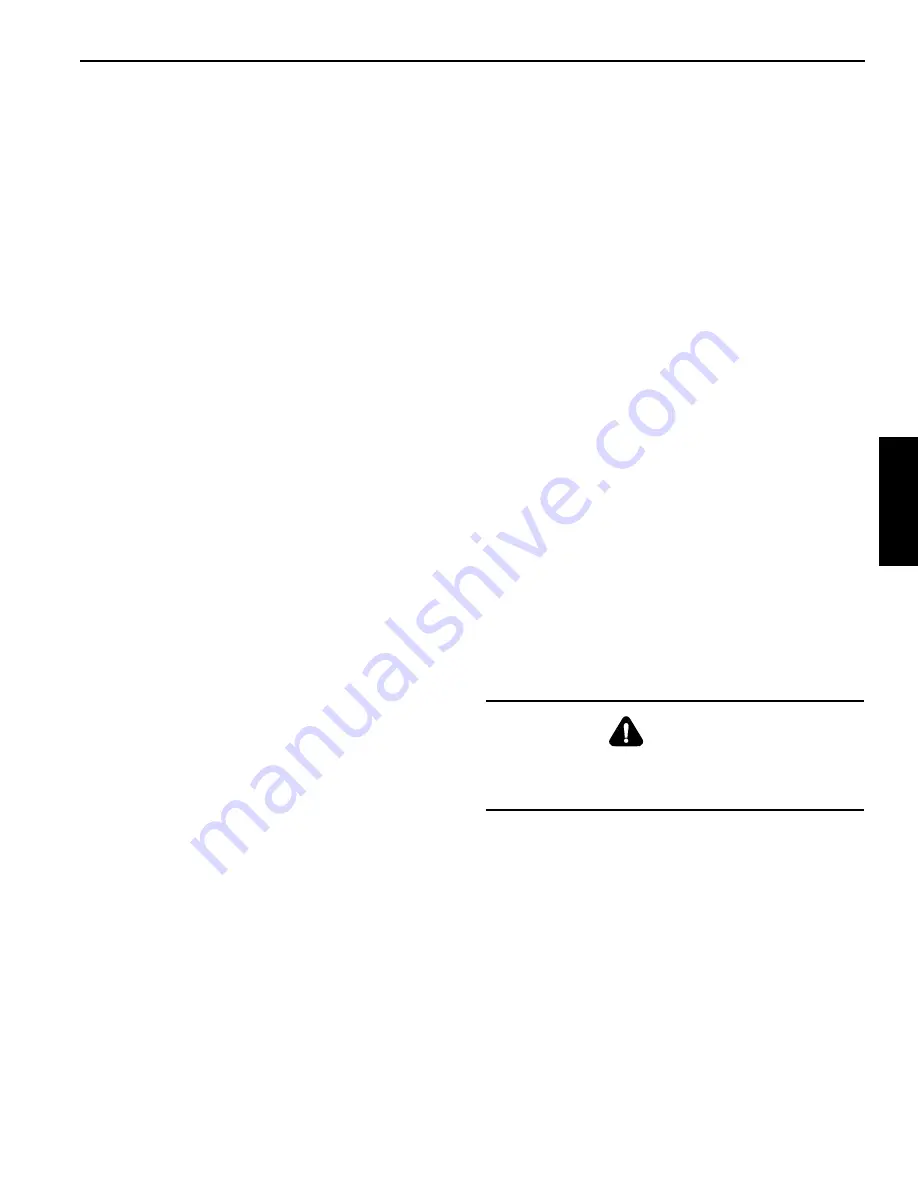
GROVE
3-61
TMS800E13 OPERATOR MANUAL
OPERATING CONTROLS AND PROCEDURES
3
Published 02-06-2014, Control # 495-00
PILE DRIVING AND EXTRACTION
By operating within the guidelines detailed below, pile driving
is an approved application for Grove brand mobile hydraulic
cranes. Because pile driving and extracting with the use of a
mobile hydraulic crane presents many variables and
unknowns, Grove crane owners must exercise discretion
when considering the use of a crane for this application.
It is not our intention to recommend specific types or makes
of pile driving and extracting equipment but rather to advise
crane owners of our operational requirements to help avoid
pile driving and extracting from having any detrimental effect
on the crane and invalidating the new machine warranty. The
following are the operating requirements that shall be used
during pile driving and extracting with a Grove mobile
hydraulic crane. These notes are in addition to the “notes to
lifting capacities” contained in the crane's in-cab load chart.
Operation of Pile Driving and Extracting
Equipment
•
All pile driving and extracting operations shall be
restricted to fully extended outriggers with all tires clear
of the ground.
•
The combined weight of the driver or extractor, piling,
leads, attachments, etc., shall not exceed 80% of the
published load chart values for on-outriggers operation.
•
The pile driver or pile extractor and attachments shall be
kept clear of the boom nose at all times.
•
The pile driver and piling shall be suspended from a
hoist cable with sufficient line speed to meet or exceed
the rate of descent of the driver and piling to preclude
impact loading or vibration from being induced into the
boom and crane structure.
•
Pile driving or extracting shall be restricted to over the
main boom only and shall not be permitted over a boom
extension or jib.
•
Pile extraction using only the crane's hoist line is unsafe
and not permitted since load values cannot be
accurately determined. Only pile extraction devices that
do not transmit vibration or shock loading into the crane
are permitted. All possible precautionary measures shall
be taken to prevent shock loads or vibration from being
imposed on crane components, either directly through
the hoist cable or indirectly from ground borne vibration.
•
The operator and other personnel associated with the
pile driving and pile extraction operation shall have read
and understood all safety standards applicable to crane
operations as well as being thoroughly trained in the
safe operation of pile driving and extracting equipment.
•
The load lines shall be kept vertical at all times during
pile driving and pile extraction operations.
Crane Equipment
•
Hoists shall be equipped with a cable follower to aid in
proper spooling of cable.
•
All cable retainer pins and cable guides/retainers shall
be in place.
•
All boom extensions or jibs must be removed from the
machine before pile driving or extraction begins.
•
All hoist hooks shall be equipped with a positive locking
latch.
Crane Inspection
•
In addition to the crane's frequent and periodic
inspections, dated daily records shall be maintained
showing inspections were performed on the crane
during the time it was used for pile driving or extraction.
•
All anti-two block warning devices and RCL systems
shall be inspected daily and verified to be functional.
•
All areas of the crane subject to fatigue shall be
inspected monthly, and before the crane is to return to
lifting service.
•
The boom shall be inspected daily to ensure all wear
pads remain in place. Cranes which utilize pinned boom
sections shall be inspected daily to ensure the pinning
mechanism operates properly and to check for undue
wear at the pins and pinning plates. The hoist cable shall
be inspected daily to ensure no chafing or wear is
occurring.
STOWING AND PARKING
When parking the crane, do the following.
1.
Remove the load from the hook.
2.
Remove or stow jibs if so equipped.
3.
Fully retract all boom sections.
4.
Lower the boom to normal travel position.
5.
Engage the swing brake, swing lock pin, and 360 degree
swing lock.
6.
Retract all stabilizer cylinders and outrigger beams.
7.
Turn the crane function power switch to the off position
(press bottom of switch).
DANGER
Never park crane near holes, on rocky surfaces, or on soft
spots. This may cause crane to overturn, resulting in
injury or death to personnel.
Reference Only