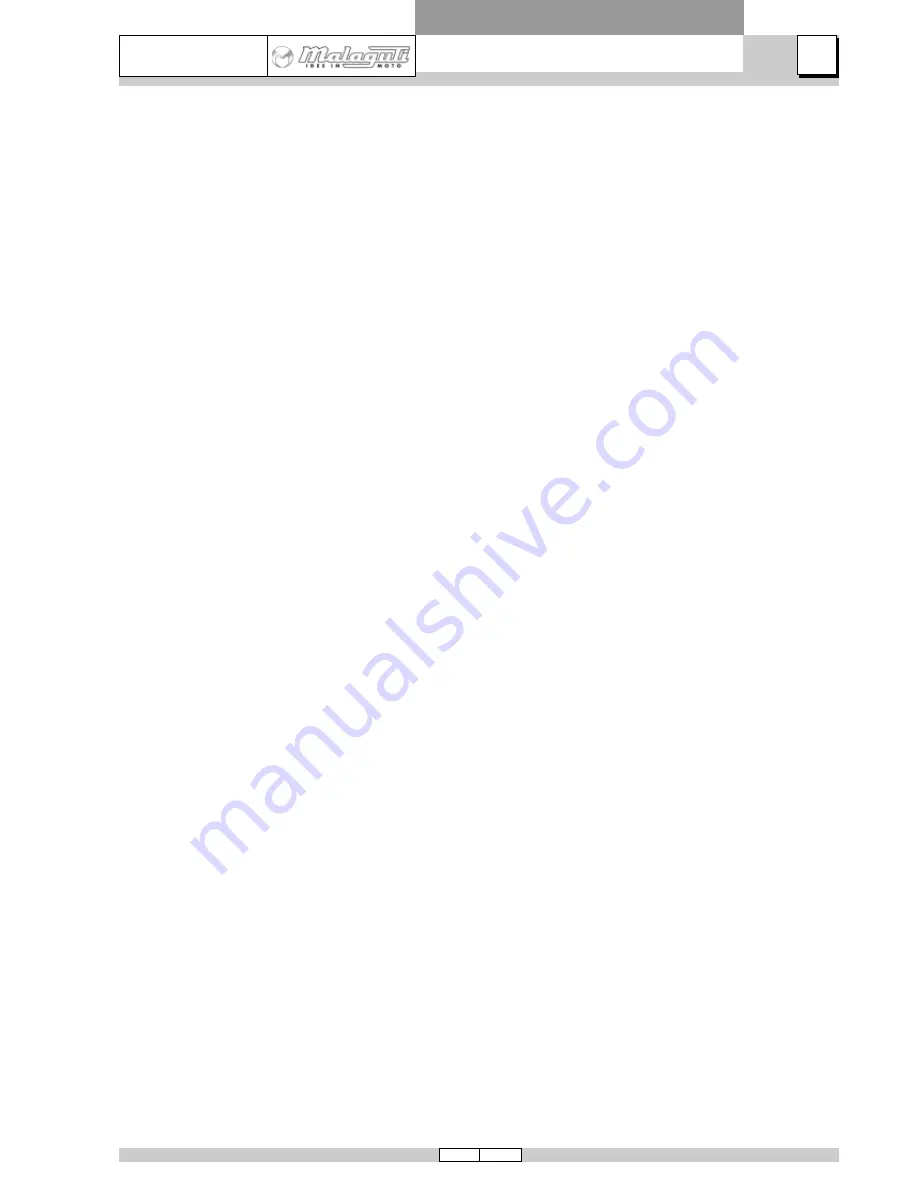
51
09/05
A
PASSWORD 250
FRAME AND RUNNING GEAR
5
ACCESSORIES
ACCESSORIES AVAILABLE
The scooter can be fitted with following accessories:
•
COLOUR COORDINATED TOP BOX
•
ELECTRONIC ANTI-THEFT DEVICE
•
WINDSHIELD
NOTE
The Malaguti spare parts catalogue is updated frequently. Contact MALAGUTI SpA for information
about new accessories for your “PASSWORD 250”.
• MALAGUTI Spa guarantees full compatibility of this scooter with genuine MALAGUTI MALBO accessories sold
through Authorised MALAGUTI Centres.
• MALAGUTI Spa is released from all liability for damage to the vehicle or to the user due to installation of non-original
accessories. Likewise, MALAGUTI Spa is released from all liability for damage to the vehicle or harm to the user due
to improper installation of accessories (including genuine original accessories). In this case all responsibility is borne
by the person/organisation that performed said installation.
• If you wish to fit electrical or electronic accessories, always make sure that they do not interfere with the normal
operation of the vehicle.
• If you wish to fit a non-approved part to the vehicle, contact MALAGUTI Spa before proceeding to find out if the
accessory is compatible with your vehicle.
ACCESSORIES